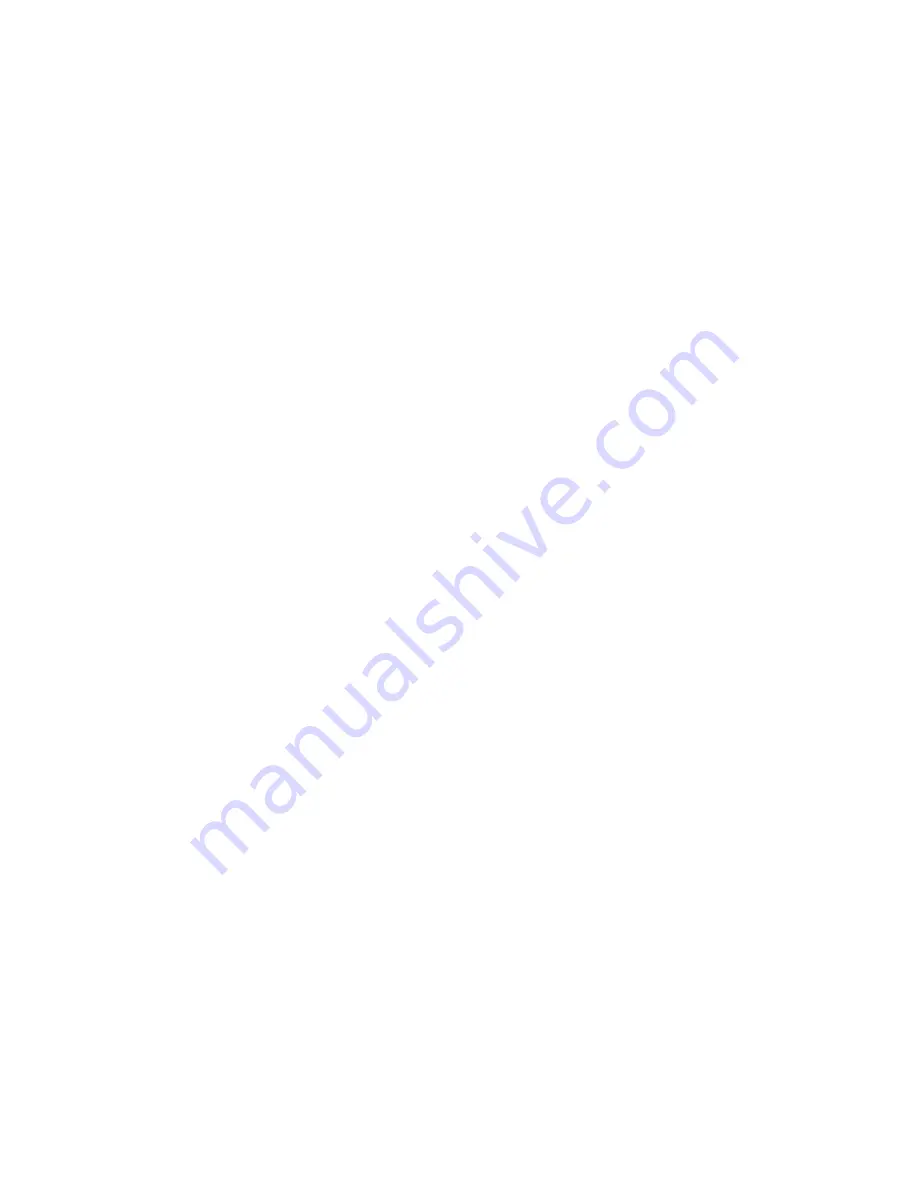
leading and trailing ignition under light load. Under full load, the engines generally make best power with
closer to zero degrees of split. A rotary will run on just the leading or trailing ignition, but a power loss
will occur. Keep this in mind when trying to diagnose ignition wiring problems.
•
Rotor 1
Leading: Coil Channel A1
Trailing: Coil Channel A2
Coil Channel A1 and A2 are split by the value in the Dual Plug Timing Split.
•
Rotor 2
Leading: Coil Channel B1
Trailing: Coil Channel B2
Coil Channel B1 and B2 are split by the value in the Dual Plug Timing Split.
C.7. Dual Plug Engines
4 cylinder only
For dual plug engines, there are two spark plugs per cylinder. Although it may seem that you
should connect both towers of one coil to the two spark plugs of one cylinder, this is NOT the case. Doing
so would require one coil to fire two spark plugs that are on the compression stroke, which would have a
very negative effect on spark energy. Instead, the coils must be wired so that each cylinder will have two
coils for its two spark plugs. Refer to the example of the 6-cylinder Porsche Dual Plug engine (
Figure
C.2.3
) to see how the wiring should be done.
Since most dual plug cylinder heads have a hemispherical design, the spark for both plugs on an
individual cylinder should occur at the same instant for optimum flame-front propagation. However, with
non-hemispherical dual plug heads, it may be desired to experiment with staggering the spark timing from
one plug to the next. To do this, the Dual Plug Timing Split Table can be used. The values entered into
this table represent the timing split (in degrees) between the two spark plugs on a particular cylinder. When
this is done, the flame front will begin at different areas of the cylinder at different times, resulting in an
uneven flame propagation. Consequently, it is recommended that most dual plug applications NOT use the
Dual Plug Timing Split.
C.8. Spark Plug Wire Selection
The
TECgt
outputs an extremely high-energy charge for the ignition coils. Resistor (carbon) core
wires work best with this charging method, since they absorb electrical noise generated by the coil firing
events. Use 8mm or larger RFI and EMI suppression wire with GM boots. We recommend using a carbon
core-style suppression wire with a resistance of 3,000 to 5,000 ohms per foot.
SOLID CORE WIRES
SHOULD NEVER BE USED
. Do not be misled by spark plug wire manufacturers claiming to give you a
“power increase” from their wire. The bottom line is that with our charging method, different spark plug
wires simply do not make a difference in terms of spark energy. However, there is a huge difference in
noise generated by different spark plug wire types (solid core wires generate a very high amount of noise
with our system).
Quoted from Magnecor’s Website:
“What is not generally understood (or is ignored) is that the potential 45,000 plus volts (with alternating
current characteristics) from the ignition coil does not flow through the entire the length of fine wire used
for a spiral conductor like the 1 volt DC voltage from a test ohmmeter, but flows in a magnetic field
surrounding the outermost surface of the spiral windings (skin effect). The same skin effect applies
equally to the same pulsating flow of current passing through carbon and solid metal conductors. A
spiral conductor with a low electrical resistance measured by a 1 volt DC ohmmeter indicates, in reality,
nothing other than less of the expensive fine wire is used for the conductor windings!
______________________________________________________________________________________
TECgt Manual Version 2.0
- Page 48 -
©2008 Electromotive, Inc.