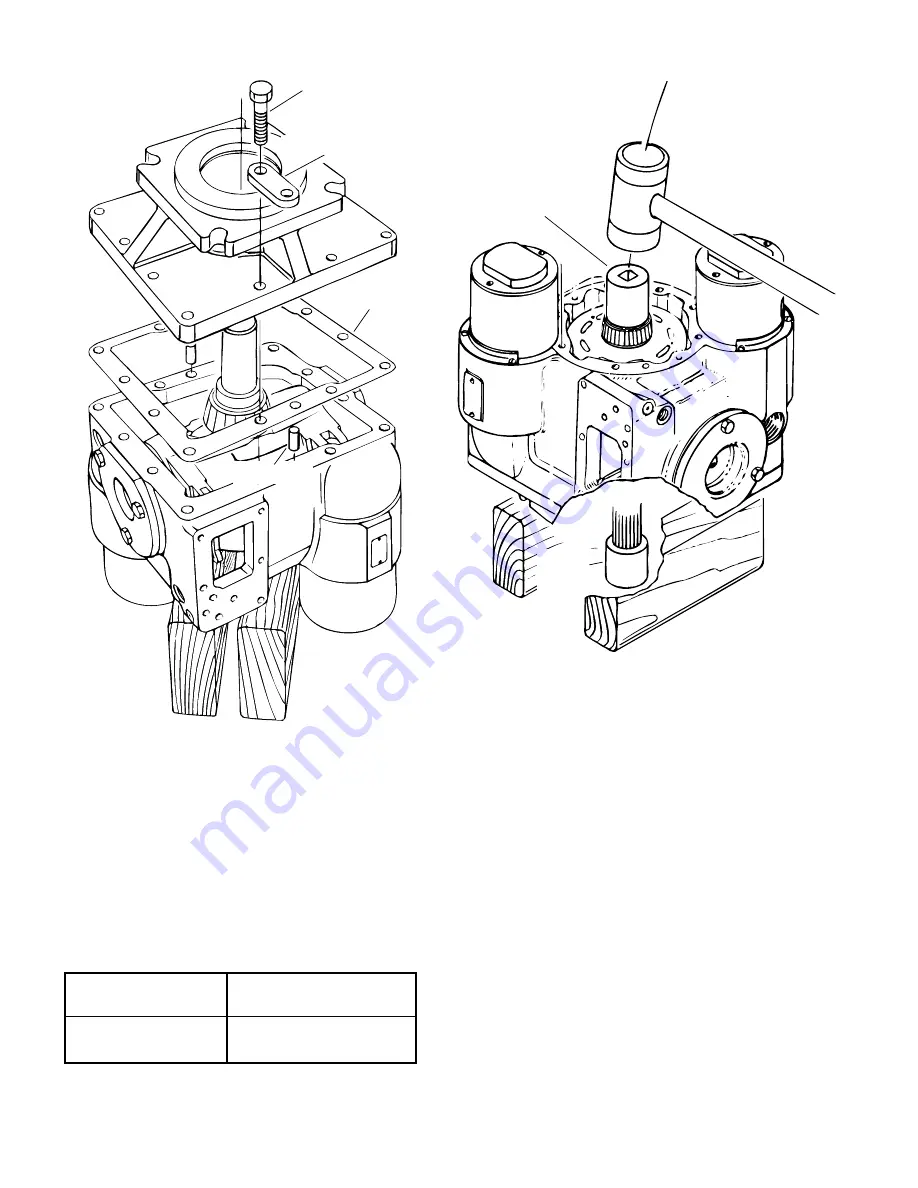
24
Dowel Pin
Shipping Strap
Bolt (12)
Gasket
Figure 31
84 Install two dowel pins in the holes in the mounting
flange surface of the motor housing.
85 Place a new mounting flange gasket on the motor
housing. Hold it in place with petroleum jelly.
86 Place the mounting flange on the motor.
87 Install the twelve mounting flange bolts. Remember
to install the shipping strap. Tighten the bolts to the
torque specified in the table below:
Model Number
Mounting Flange
Bolt Torque
33, 39
28 lb-ft [38 Nm]
46, 54, 64
44 lb-ft [60 Nm]
Bearing Cone Driver
Shaft
Support
Figure 32
88 Turn the motor over so the shaft is vertical and the
mounting flange is down.
89 Install and stake the servo sleeve retainers.
90 Support the motor’s shaft and use a bearing driver to
install the end cover bearing cone, see figure 32. Be
sure the bearing cone is seated against the shoulder of
the shaft.
Note: A detailed drawing of the bearing cone driver is
shown in the back of this manual.
91 Remove the shaft support.
Mounting Flange, End Cover Bearing and Shaft End Play
Содержание 1 Series
Страница 31: ...31 Notes...