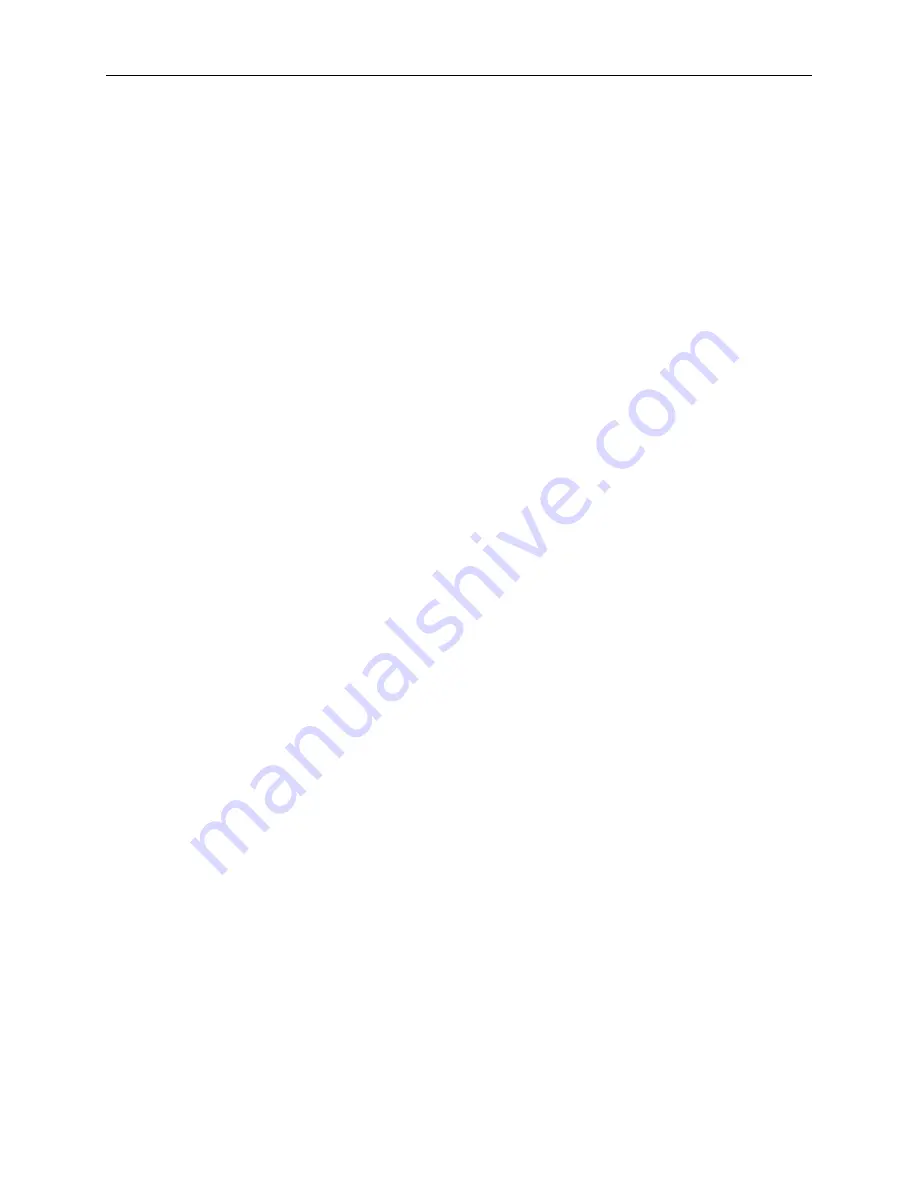
Operation 25
adjustable by turning the Conveyor timer knob, which is located to the right of
the Power switch under the product tray.
NOTE: If there is too much tension on the film while the bag is being
sealed, the seals will be more likely to be weak or blow out in the
seal area while moving through the shrink tunnel.
10. As packages are readied and sealed at the L-sealer, previous packages are
shrink-sealed in the shrink tunnel and then exit the tunnel at the far end, where
they may be placed in accumulation bins or passed to a plant conveyor line for
further processing as required.
When production is finished or at the end of a production cycle, perform an orderly shut-
down of the system. First turn off the shrink tunnel Heater Bank toggle switch, then turn
off the L-sealer Power toggle switch. Wait for the shrink tunnel to cool to required cool-
down temperature before turning off the shrink tunnel toggle Power switch, and (if
required) shut off power at the main power lever only after the shrink tunnel has
reached cool-down temperature.
CAUTION!: When shutting down the shrink tunnel, be sure to turn the
Heater Bank switch to Off and wait for the tunnel to cool down,
then turn off the Power toggle switch for the shrink tunnel.
(Refer to the procedure for setting the cool-down temperature.
Temperature will be displayed on the shrink tunnel
temperature control.) Once cool-down temperature is reached
and motors have shut down, then shut off the toggle power
switch.
Содержание Combination EC Series
Страница 1: ...EC Combination Series Semi Automatic L Sealer Tunnel User Guide EC2016T EC2016TK EC2028T EC2028TK ...
Страница 2: ......
Страница 4: ......
Страница 73: ...Appendix A Electrical Schematic 73 Electrical Schematic L Sealer ...
Страница 81: ......