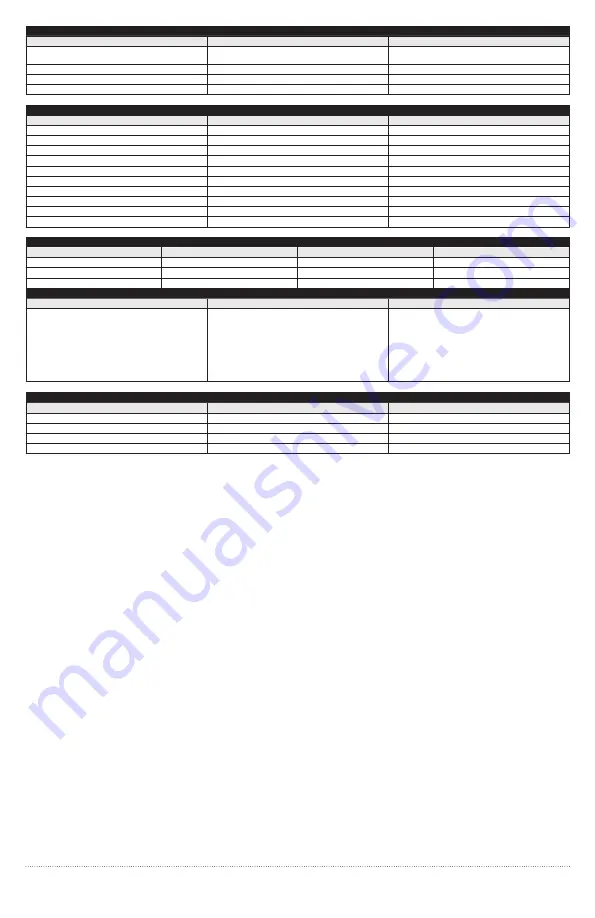
IFU . 3
FABRIC RESISTANCE TO PENETRATION OF INFECTIVE AGENTS
Test
Test method
EN Class*
Resistance to penetration by blood-borne pathogens using Phi-X174
bacteriophage
ISO 16604 Procedure C
6/6
Resistance to contamination by contaminated liquids
EN ISO 22610
6/6
Resistance to penetration by biologically contaminated aerosols
ISO/DIS 22611
3/3
Resistance to penetration by biologically contaminated dust
ISO 22612
3/3
* According to EN 14126:2003
PROTECTION AGAINST HEAT AND FLAME
Test
Test method
Result - EN Class*
Heat resistance at a temp of 180°C +/-5°C
ISO 17493
Pass
Heat resistance at a temp. of 260°C +/- 5°C
ISO 17493
Pass
Limited flame spread (surface ignition), Code letter A1
ISO 15025, Procedure A
A1, Index 3**
Convective heat, code letter B
ISO 9151
B1
Radiant heat, code letter C
ISO 6942, Method B
C1
Molten aluminium splash, code letter D
ISO 9185
D1
Molten iron splash, code letter E
ISO 9185
E2
Contact heat, code letter F
ISO 12127
F2
Electric arc - Open arc test method
IEC 61482-1-1
ATPV = 15 cal/cm
2
Electric arc - Box test method
IEC 61482-1-2
4kA - APC = Class 1
* According to EN ISO 11612:2015 ** According to EN ISO 14116:2015
PROTECTIVE CLOTHING FOR USE IN WELDING AND ALLIED PROCESSES
Test
Test method
EN Class*
Result*
Small molten metal splashes
ISO 9150
2/2
> 25 drops
Tear strength
ISO 13937-2
> 20 N
Pass
Electrical resistance
EN 1149-2
N/A
> 10
5
Ohm, Pass
SELECTION CRITERIA FOR CLOTHING FOR USE IN WELDING OR ALLIED PROCESSES (REFERENCE POINTS)
Type of welders' clothing
Selection criteria relating to the process
Selection criteria relating to the environmental conditions
Class 2
Manual welding techniques with heavy formation of spatters and drops, e.g.: Operation of machines, e.g.:
- MMA welding (with basic or cellulose- covered electrode);
- MAG welding (with CO
2
or mixed gases);
- MIG welding (with hight current);
- self-shielded flux cored arc welding;
- plasma cutting;
- gouging;
- oxygen cutting;
- thermal spraying.
- in confined spaces;
- at overhead welding/cutting or in comparable constrained positions.
N/A = Not applicable * According to EN ISO 11611:2015
WHOLE SUIT TEST PERFORMANCE
Test
Result
EN Class
Type 3: Jet test (EN ISO 17491-3)
Pass*
N/A
Type 4: High level spray test (EN ISO 17491-4, Method B)
Pass
N/A
Type 6: Low level spray test (EN ISO 17491-4, Method A)
Pass
N/A
Seams strength (EN ISO 13935-2)
> 300 N
5/6**
N/A = Not applicable * Test performed with taped hood ** According to EN 14325:2004
For further information about this garment and its performances, please contact your supplier or DuPont: dpp.dupont.com
RISKS AGAINST WHICH THE PRODUCT IS DESIGNED TO PROTECT:
This coverall is designed to offer chemical protection and protection against heat and flame based on the specific uses in
accordance with requirements of the standards and the classes for which the garment is certified. The standards and classes are displayed in the CE-label in the garment. It is designed to protect against short flame contact, small,
certain forms of heat transfer, molten metal splash, molten metal spatter from welding applications, thermal risk from electric arc and as an escape suit to potentially reduce skin burns or increase survival probability in the event of
a flash fire (conform to EN ISO 11612:2015 and EN ISO 11611:2015). It is typically used, depending on toxicity and exposure conditions, for protection against certain organic and inorganic liquids and intensive or pressurized liquid
sprays, where the exposure pressure is not higher than the one used in the Type 3 test method. This protective garment provides protection against intensive or pressurized liquid sprays (Type 3), intensive liquid sprays (Type 4)
and limited liquid splashes or sprays (Type 6). Fabric used for this coverall has passed all tests of EN 14126:2003. Under the exposure conditions, as defined in EN 14126:2003 and mentioned in the above table, the obtained results
conclude that the material offers a barrier against infective agents.
LIMITATIONS OF USE
: This garment is not intended for fire-fighting activities, and is designed to provide specific level of protection against certain chemicals, molten metals, molten metal spatter from welding
applications, electrical arc or thermal radiation based on the standards and classes met by the garment as displayed in the above tables and on the CE-label in the garment. The garment does not protect against all kind of electric arcs.
Deviations from the parameters in this document may result in more severe conditions. This garment is not intended to be used as electrical insulating protective clothing and does not provide protection against electrical shock. It
is designed and tested to help reduce injury during escape from a fire. It is intended to help reduce the potential for injury, but no protective apparel alone, can eliminate all risks of injury or death. Protective apparel must be used in
conjunction with general safety practices by trained personal. The level of protection against flame will be reduced if the protective clothing is contaminated with flammable materials. In the event of a molten metal splash the user
shall leave the working area immediately and take off the garment. In the event of a molten metal splash, the garment, if worn next to the skin, will not eliminate all risks of burn injury. An increase in the oxygen content of the air
will reduce considerably the protection of the welder’s protective clothing against flame. Extreme care should be taken when welding in confined spaces, e.g. if it is possible that the atmosphere may become enriched with oxygen.
The garment is not intended to give electrical protection (shock). It is only intended to protect against brief inadvertent contact with live parts of an arc welding circuit, and additional electrical insulation layers will be required where
there is an increased risk of electric shock; garments meeting the requirements of 6.10 of EN ISO 11611:2015 are designed to provide protection against short term, accidental contact with live electric conductors at voltages up to
approximately 100 V d.c. Additional partial body protection may be required, e.g. for welding overhead. The electrical insulation provided by clothing will be reduced when the clothing is wet, dirty or soaked with sweat. No garments
such as shirts, pants, undergarments or underwear which melt under heat, flame and arc exposures shall be worn underneath this coverall. The use of Nomex® or non-melting undergarments is recommended. The air trapped
between layers of material plays an important part in providing heat insulation. The protection is reduced in areas which are tight fitting or compressed by belt or straps. The coverall can only provide protection if interfaces between
this garment with other garments at the neck, wrists and ankles is adequate. The fabric used in this coverall is inherently antistatic on the inside surface only and the garment meets the surface requirements of EN 1149-5:2018
when measured according to EN 1149-3:2004 and EN 1149-2:1997. This shall be taken into consideration if the garment is grounded. The electrostatic dissipative performance of both the suit and the wearer needs to be continuously
achieved in such a way as the resistance between the person wearing the electrostatic dissipative protective clothing and the earth shall be greater than 10
5
Ohm and less than 10
8
Ohm e.g. by wearing adequate footwear/flooring
system, use of a grounding cable, or by any other suitable means. Always verify correct grounding via a test with a monitoring device. Electrostatic dissipative clothing shall not be opened or removed whilst in presence of flammable
or explosive atmospheres or while handling flammable or explosive substances. Electrostatic dissipative protective clothing is intended to be worn in Zones 1, 2, 20, 21 and 22 (see EN 60079-10-1 [7] and EN 60079-10-2 [8]) in which
the minimum ignition energy of any explosive atmosphere is not less than 0.016mJ. Electrostatic dissipative clothing shall not be used in oxygen enriched atmospheres, or in Zone 0 (see EN 60079-10-1 [7]) without prior approval
of the safety engineer. The electrostatic dissipative performance of the electrostatic dissipative protective clothing can be affected by wear and tear and possible contamination. Electrostatic dissipative protective clothing shall
permanently cover all non-complying materials during normal use (including bending and movements). In situations where static dissipation level is a critical performance property, endusers should evaluate the performance
of their entire ensemble as worn including outer garments, inner garments, footwear and other PPE. Further information on grounding can be provided by DuPont. Exposure to certain very fine particles, intensive liquid sprays or
splashes of hazardous substances may require garments of higher mechanical strength and/or barrier properties than those offered by this coverall. The user must ensure garment barrier compatibility to all chemical exposure risks
before use. The user shall use the attached hood drawstrings to pull tightly around the respirator, and cover the drawstrings behind the storm flap before closing it with the rugged hook and loop material. To achieve the claimed
chemical protection in certain applications, taping of the hood was necessary. Taping of the garment may negatively impact protective properties against heat and flame, thermal radiation, electric arc, metal splash and molten metal
spatter in welding applications. If tape is used, the wearer shall use a flame resistant/high temperature tape. Tape must not negatively impact doffing process in case of an emergency. This fabric offers little or no thermal insulation
to protect the wearer’s skin from prolonged exposure to hot or cold. The temperature range for the fabric and seams it well beyond the temperatures that the human skin can withstand without injury. The user shall perform a risk
analysis, including a verification of the barrier properties against the chemicals of concern, upon which he shall base his choice of PPE. He shall be the sole judge regarding the combination of the protective clothing with ancillary
equipment (boots, gloves, respiratory protective equipment, undergarments etc.) and for how long a protective garment can be worn on a specific job with respect to its protective performance, wearing comfort and heat stress. For
full body protection, the protective clothing shall be worn in the closed state. DuPont shall not accept any responsibility for improper use of its products.
PREPARING FOR USE
: Inspect this garment prior to use. In the event of defects, contamination, or damage, do not wear.
CLEANING AND MAINTENANCE
: For limited use only. Do not clean, neither for hygienic reasons. This garment can be worn until damaged, altered or contaminated. If the garment is contaminated during use,
it must be decontaminated prior to doffing and then discarded. If the garment is damaged during use, retreat immediately, undergo decontamination and then discard the garment.
STORAGE AND TRANSPORT
: This coverall may be stored at < 49 °C in the dark (cardboard box) with no UV light exposure. The shelf life of this coverall is 5 years if correctly stored.
DISPOSAL
: This coverall can be incinerated or buried in a controlled landfill. Disposal restrictions depend upon the contamination incurred during use and are subject to national or local legislation.
DECLARATION OF CONFORMITY
: Declaration(s) of conformity can be downloaded at: www.safespec.dupont.co.uk