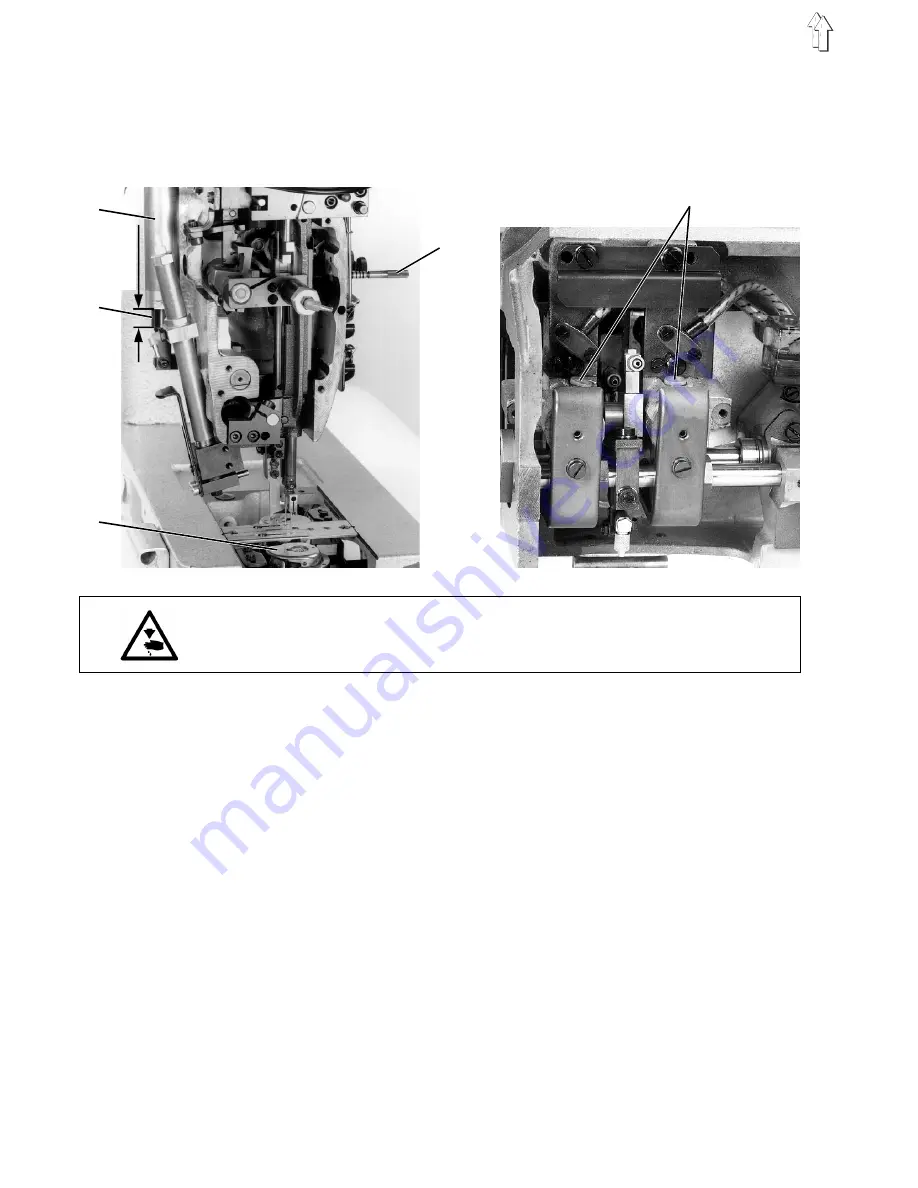
11.5 Looping Stroke
The looping stroke is the path of the needle bars from lower dead
center up to the point at which the hook points lie at the center of the
needle.
The looping stroke is 2 mm.
It is set with the arresting pin 4 (Order no. 0211 000700).
Caution Risk of Injury !
Turn the main switch off.
Set the looping stroke only with the main switch turned off.
–
Remove the folder and needle plate.
–
Remove the tops of the bobbin case 3 with the bobbins.
–
Swing the needles to the center of the needle hole.
Here clamp a suitable spacer 2 (13.5 mm thick) between the
cylinder 1 and its piston rod.
–
Tilt the machine head to the back.
–
Remove the plastic plugs 5.
–
Remove the screws found under the plastic plugs 5.
–
Tilt the machine head forward.
–
Push the arresting pin 4 through the drilled hole in the machine
arm.
The arresting pin 4 must catch in the groove of the arm shaft crank.
–
Turn the hook manually until the hook points lie at the center of the
needle.
–
Tilt the machine head to the back.
–
Tighten the first of the screws found under the plastic plugs 5.
–
Remove the arresting pin 4.
–
Tighten the second of the screws found under the plastic plugs 5.
–
Press the plastic plugs 5 into the drilled holes again.
–
Remove the spacer 2.
1
2
3
13
,5
mm
4
5
50
Содержание 745-22
Страница 17: ...8 7 6 5 1 2 3 4 17 ...
Страница 19: ...1 2 3 4 7 8 9 10 5 6 19 ...
Страница 25: ...745 22 745 23 745 24 5 4 3 4 3 4 25 ...
Страница 27: ...745 22 745 23 745 24 7 9 2 6 5 7 9 1 2 3 4 5 6 7 8 9 5 mm 10 11 12 13 14 15 27 ...
Страница 43: ...1 2 3 4 5 6 7 8 0 2 mm 9 10 43 ...
Страница 79: ...2 3 4 5 y 7 1 8 6 9 10 1 2 3 4 5 79 ...