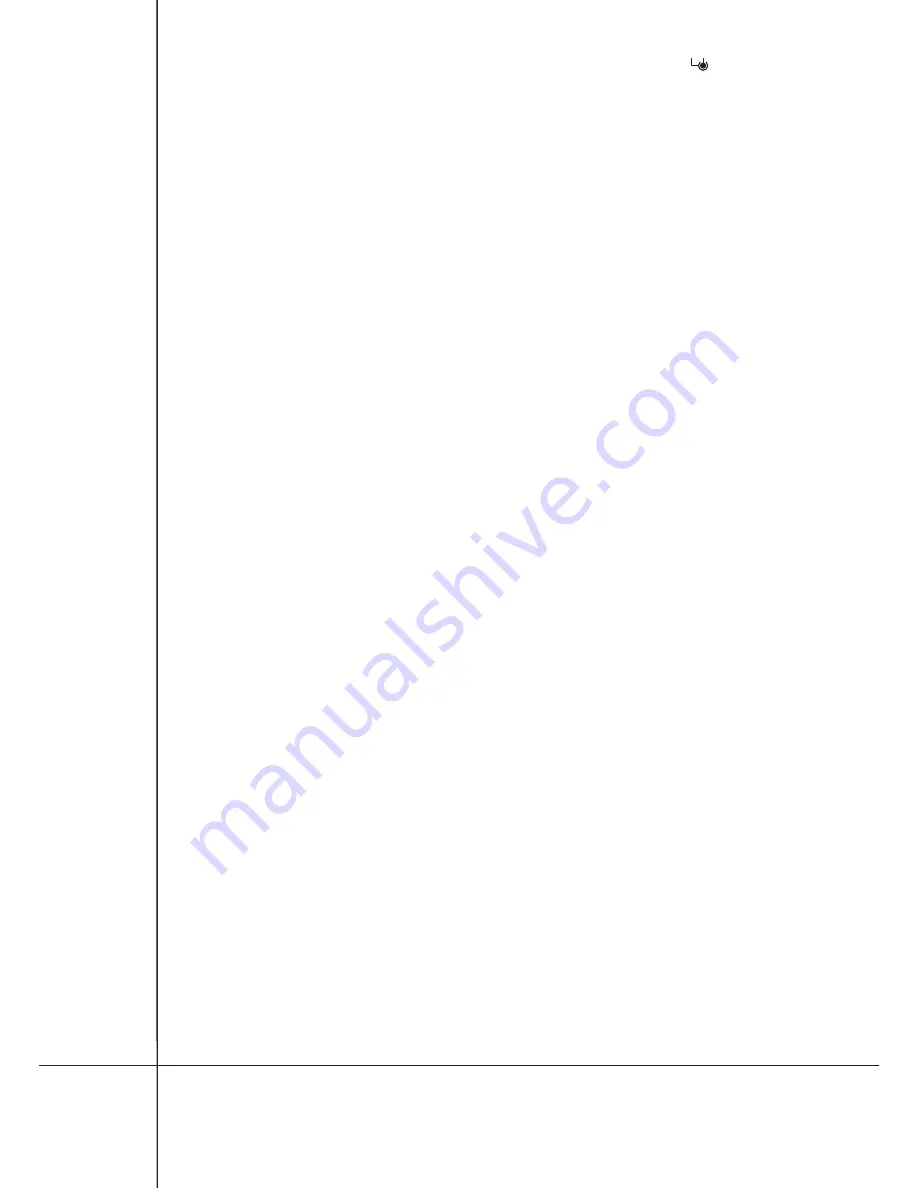
4.3.13. Connector for TRX radio card and clamps for connecting radio aerial (14, fig.1)
The driver has radio card TRX series connector and aerial input of the radio receiver. Connection and
description of the card is in TRX card manual.
5. Driver operation description
After switching the power supply of the driver, there is an automatic change into OPERATION MODE. In
operation mode, the current state of inputs is signaled by LED diodes (16, fig. 1)
The programming takes place with the help of the LED L1 diode and PROG/STOP and P/P buttons which
are on the driver board (6.7 fig. 1), groups of DIP-SWITCH micro switches (11 fig. 1), JP1 jumper and PW
potentiometer (9 and 8 fig. 1). The control panel learns the operation times and pause during the procedure of the
programming. Programming procedure includes repeated operation with using the P/P button or remote
control if such was assigned. Important remarks before the programming:
4
Connect the power supply to the control panel and check if inputs work correctly by inspecting appropriate
diodes (diodes of NC contacts must shine).
4
Remove all the obstacles from the gate operation zone.
4
Diodes of the limit switch must be lighted when the gate is half opened. When the gate is moving to the closed
position the LED FCC diode must go out, the second FCA diode must go out when the gate reaches opened
position.
4
In order conduct the successful process of the driver programming keep the following order:
4
analyse tables with individual settings of DIP-SWITCHes and to choose appropriate functions, see tab. 1;
4
programme operation time of the gate;
4
make possible regulations of the traction force with the PW potentiometer;
4
check the accuracy of operation and repeat the programming if needed.
6.1. SIMPLE mode of learning
It is simple and fast form of setting times of closing, opening, auto-closing. Slowing times before total
opening and closing are set automatically. Programme according to following steps (fig. 3):
4
manually place the gate in the middle of the way (1, fig.3).
4
press PROG/STOP button and hold it pressed for about 3 seconds, until L1 diode does not light constantly (2,
fig.3). Driver is in the programming mode.
4
Press P/P button. The gate will start moving in direction toward closing (3, fig.3). If the gate moves on the
direction towards opening it is necessary to change the direction of engine operation and limit switch
operation, see pt. 4.3.2-4.3.3.
4
the gate reaches closed position (4, fig.3) and it starts opening automatically (5, fig.3), stopping at the
outermost opening position (6, fig.3). The driver starts remembering the auto-closing time ( see tab.1).
4
when the demanded pause time is complete, press P/P button. The motor will start closing (7, fig.3), finishing at
the outermost closing position. L1 diode turns off, the end of programming procedure (8, fig.3)
6.2. EXTENDED mode learning
This procedure requires a little bit more involvement in the process the learning from the installer, than
in the case of the simple mode. The installer is able to set additionally the times of slowing down at opening and
closing according to personal needs. In order to set different zones of slowing down, act in the following way (fig.
3):
4
manually place the gate in the middle of the way (1, fig.3).
4
press PROG/STOP button and hold it pressed for about 5 seconds, until L1 diode does not light constantly (2,
fig.3).
Driver is in the programming mode.
4
Press P/P button. The gate will start moving in direction toward closing (3, fig.3). If the gate moves on the
direction towards opening it is necessary to change the direction of engine operation and limit switch operation,
see pt. 4.3.2-4.3.3.
4
the gate reaches closed position (4, fig.3) and it starts opening automatically (5, fig.3).
4
while opening, before the full opening of the gate press P/P button in the position of required slowing down (6a,
fig.3). The gate stops for a moment and then continues and finishes the opening.
4
after stopping at the outermost opening position
the driver starts remembering the auto-closing time
(6,
fig.3).
4
when the demanded pause time is complete, press P/P button. The motor will start closing (7, fig.3).
6. Programming of SWIFT6-CB driver
8
Содержание SWIFT6
Страница 2: ......