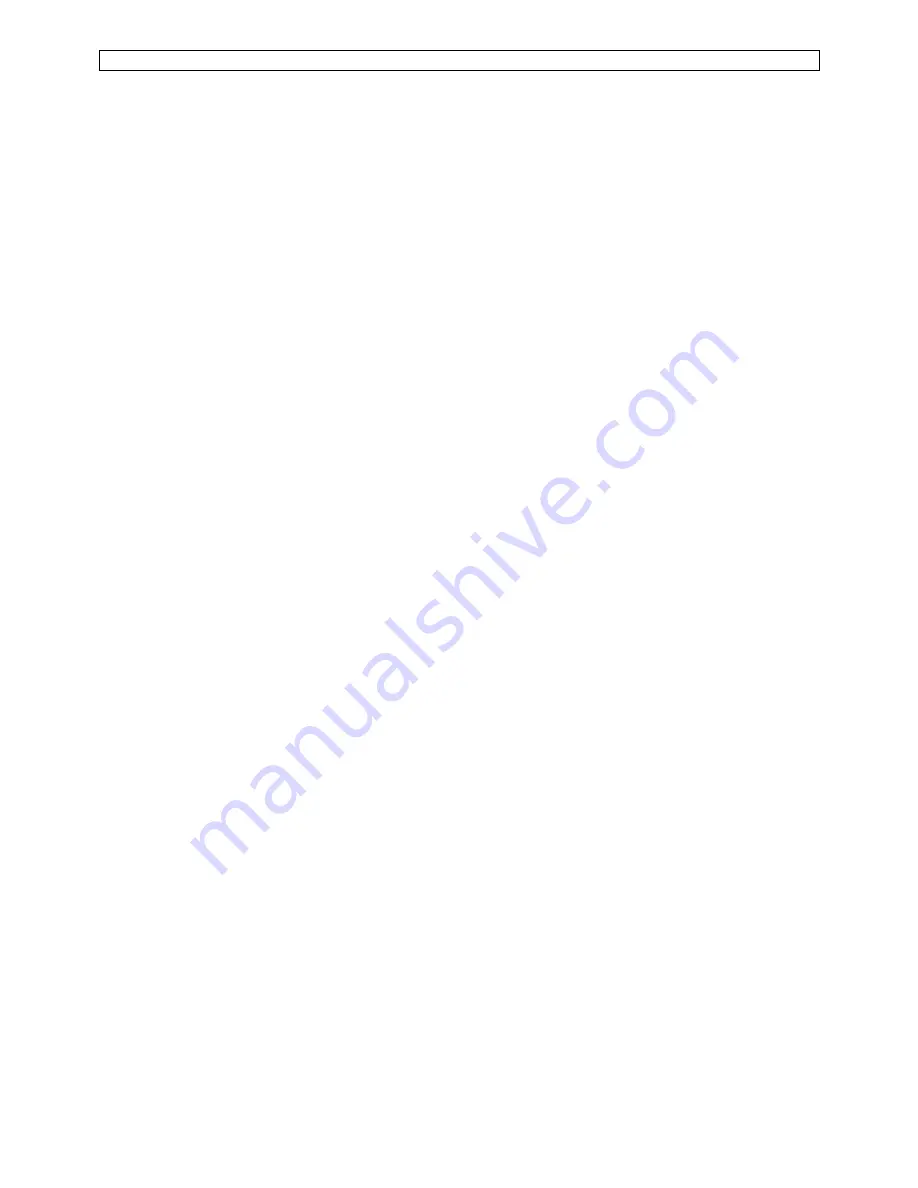
DPC Touch User Manual
12
Time control
fields display measured Tightening time and calculated Min and Max limits. Min and
Max values are calculated according to percentages defined in operating settings.
Tightening job
is a preset number to be selected for the current tightening position via 24V outputs
(direct or binary logic) if supported by the tool.
Retightening job
is similar to the Tightening job but it is used only for rework operation and it is
automatically selected after NG tightening (if retightening is enabled in operating settings).
Pick up positions
1 and 2 can be selected to allow to start the tool in a specific position or area
(outside position OK zone) in order to pick up a screw. Fastening OK signals and Motor run signals are
not effective on pick-up position.
Driver
1 and 2 selection is only applied to DOGA tools (GX, GY, DO, GA) connected through RJ45 port.
This selection allows enabling and disabling tools for each individual position.
Reset
button is used to reset current position data to default values. To delete a position press Reset
button one more time after resetting the position data to defaults.
NOTE
: there is no need to use APPLY button after modification of any of the above values. APPLY
button is only used to save current values from encoders for the current position.
A Fastening step can be programmed manually or automatically.
6.1.1 Manual programming of fastening step:
0.
Optional: Use Smart tolerance detection feature (refer to Smart tolerance detection below)
1.
Position the arm on the first screw.
Encoders monitoring fields are displaying the current position of the arm.
2.
Press APPLY button to save current position of the arm. Saved values from encoders will be
displayed in corresponding fields. If not satisfied with the result press APPLY button again to
rewrite saved values from encoders.
3.
Default tolerance values for the approaching Area and for the OK zone are applied. To
change default values refer to encoders
’
settings. Tolerance values can be adjusted manually
for each individual position or by using Smart tolerance detection feature.
4.
If necessary, define Tightening and Retightening programs to be used for the current
position, feeding point (see Pick Up positions in encoders
’
settings) and the screwdriver to be
used for this tightening position (used only for DOGA GX/GY/DO/GA tools).
5.
If necessary, enter Min and Max tightening time limits in corresponding fields. Tightening
time control is not used if limits are equal to 0.
6.
Press NEXT button to pass to the next position.
7.
Repeat 1-6 for each position.
8.
Activate Non-sequential mode if there is no need to keep strict tightening sequence.
NOTE:
in non-sequential mode,
retightenings can’t be managed.
9.
Press SAVE button to save the step or CANCEL button to quit programming without saving
changes.
Содержание DPC Touch
Страница 1: ... DPC Touch INSTRUCTIONS MANUAL ...
Страница 24: ...DPC Touch User Manual 25 9 3 Inputs wiring scheme ...
Страница 36: ...Doc 60290 12 17 ...