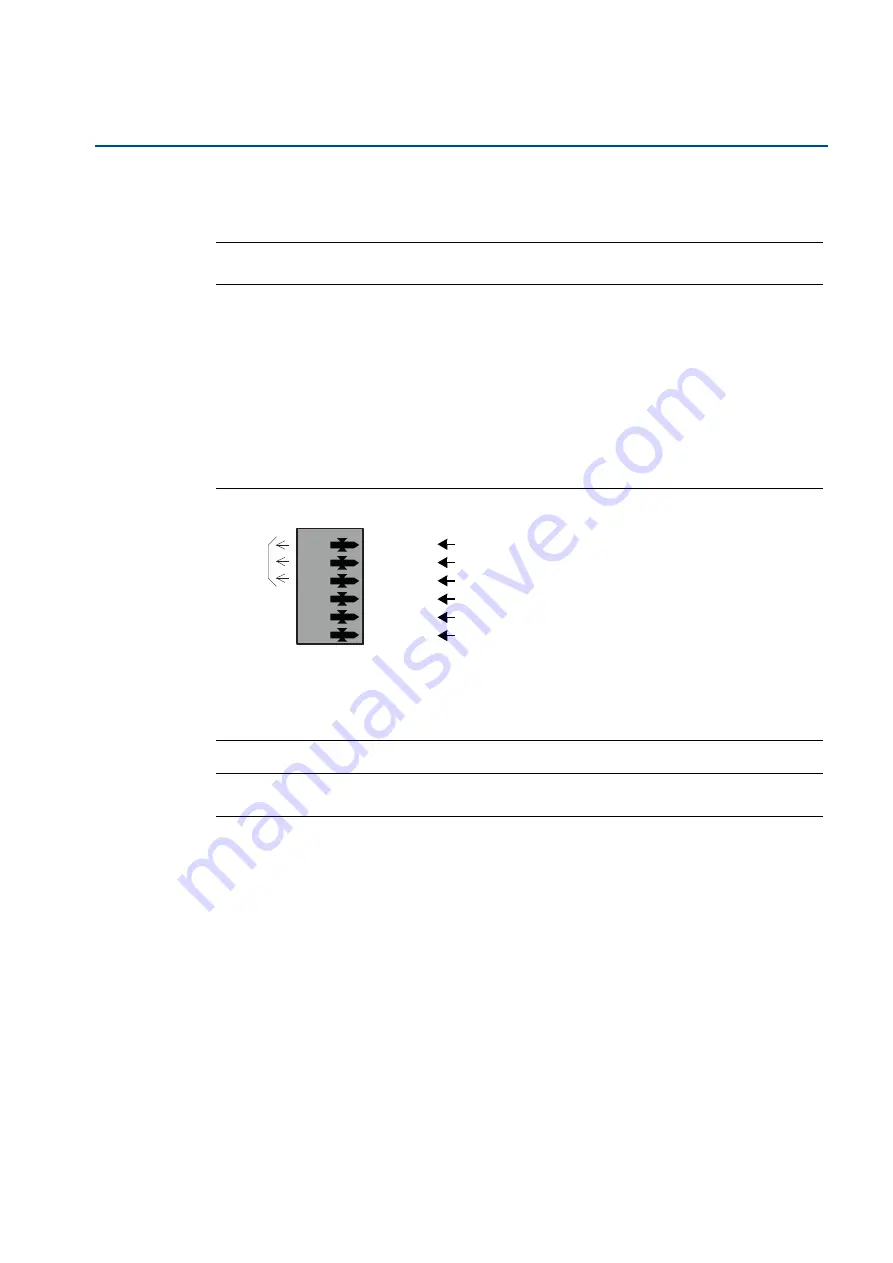
10
Installation and Operating Manual
IP227, Rev DA
Mobrey MCU200 Series
February 2020
the case of non-metallic sensors). If this continuity is broken, the control unit illuminates the
“FAULT” LED to indicate the sensor cable is damaged and changes the output relay to the
“ALARM” state.
Note
The separated nature of sensor types 442S and or 448S usually make this cable check unreliable.
Relay output and LED logic selection
A bank of six slide-switches is located towards the top of the PCB (
Figure 4 on page 8
).
Each switch is numbered and labelled to give brief function information (
Figure 5
).
The switches are used to set:
The relay output state logic (relative to the sensor state).
Associated time delays for state changes and LED colours.
Figure 5. Relay output and LED logic switch
Ex-factory position is to the right for all switches.
OSC = sensor oscillating.
E = relay energised.
NE = de-energised.
Note
Slide-switches are adjustable using a pencil. Ex-factory settings are with all switches to the right.
Procedure for setting the switches.
1.
Set the top three switches first. Examples are in
Figure 6
.
2.
Set the remaining switches in the following order, starting at the bottom and working
upwards.
a.
Switch number 6.
If the MCU200 relay is to be energised (E) when the sensor is oscillating (OSC),
set the No. 6 blue switch to the right (OSC=E). This is the preferred setting, to give a
de-energised relay in the ALARM state for a gap sensor as a low level alarm.
The opposite setting might be used for a sludge blanket detector, when an oscillating
sensor (OSC), which occurs in clear liquids, might preferably cause the relay to
de-energise (OSC=NE).
b. Switch number 5.
30 s
0.5 s
Switch 1
2 s
Switch 2
8 s
Switch 3
E = GREEN
Switch 4
Delay to NE
Switch 5
OSC. = E
Switch 6
E = RED
Delay to E
OSC. = NE