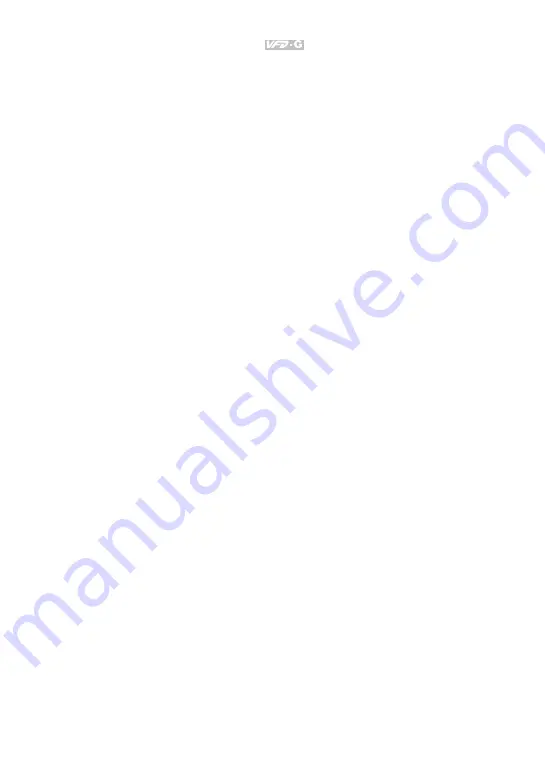
Appendix C How to Select the Right AC Motor Drive
|
C-4
Revision July 2008, EG03, SW V1.06
C.2 General Precaution
Selection Note
1.
When the AC Motor Drive is connected directly to a large-capacity power transformer
(600kVA or above) or when a phase lead capacitor is switched, excess peak currents
may occur in the power input circuit and the converter section may be damaged. To avoid
this, use an AC input reactor (optional) before AC Motor Drive mains input to reduce the
current and improve the input power efficiency.
2.
When a special motor is used or more than one motor is driven in parallel with a single
AC Motor Drive, select the AC Motor Drive current
≥
1.25x(Sum of the motor rated
currents).
3.
The starting and accel./decel. characteristics of a motor are limited by the rated current
and the overload protection of the AC Motor Drive. Compared to running the motor D.O.L.
(Direct On-Line), a lower starting torque output with AC Motor Drive can be expected. If
higher starting torque is required (such as for elevators, mixers, tooling machines, etc.)
use an AC Motor Drive of higher capacity or increase the capacities for both the motor
and the AC Motor Drive.
4.
When an error occurs on the drive, a protective circuit will be activated and the AC Motor
Drive output is turned off. Then the motor will coast to stop. For an emergency stop, an
external mechanical brake is needed to quickly stop the motor.
Parameter Settings Note
1.
The AC Motor Drive can be driven at an output frequency up to 400Hz (less for some
models) with the digital keypad. Setting errors may create a dangerous situation. For
safety, the use of the upper limit frequency function is strongly recommended.
2.
High DC brake operating voltages and long operation time (at low frequencies) may
cause overheating of the motor. In that case, forced external motor cooling is
recommended.
3.
Motor accel./decel. time is determined by motor rated torque, load torque, and load inertia.
Содержание AC Motor Drive VFD-G
Страница 1: ......
Страница 2: ......
Страница 3: ......
Страница 17: ...Chapter 1 Introduction 1 8 Revision July 2008 EG03 SW V1 06 For 150 215HP Frame G Step 1 Step 2 Step 3 Step 4...
Страница 18: ...Chapter 1 Introduction Revision July 2008 EG03 SW V1 06 1 9 For 250 300HP Frame H Step 1 Step 2 Step 3 Step 4...
Страница 23: ...Chapter 1 Introduction 1 14 Revision July 2008 EG03 SW V1 06 This page intentionally left blank...
Страница 45: ...Chapter 2 Installation and Wiring 2 22 Revision July 2008 EG03 SW V1 06 This page intentionally left blank...
Страница 51: ...Chapter 3 Keypad and Start Up 3 6 Revision July 2008 EG03 SW V1 06 This page intentionally left blank...
Страница 141: ...Chapter 4 Parameters 4 90 Revision July 2008 EG03 SW V1 06 This page intentionally left blank...