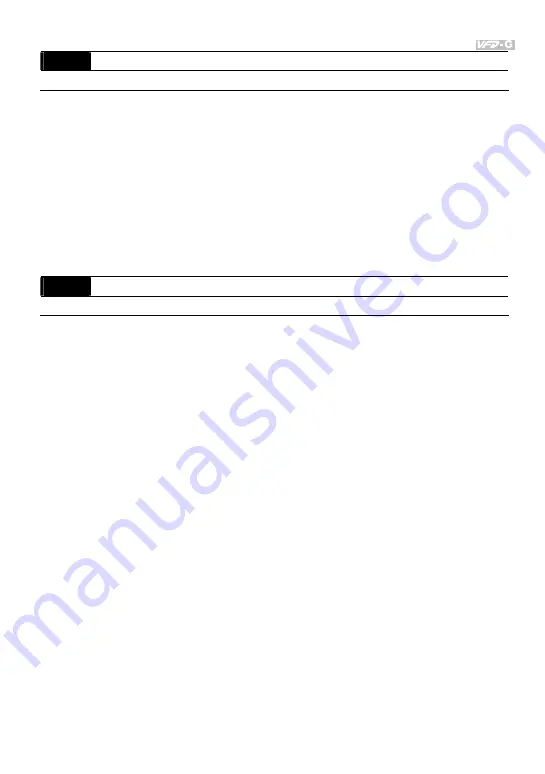
Chapter 4 Parameters
|
Revision July 2008, EG03, SW V1.06
4-59
07 - 03
No-load Current of Motor
Unit: 1
Settings
1~99%
Factory Setting: 30%
This parameter sets the no-load current of the motor.
Pr.7-03 = (no load current / drive rated current)
Example: If the rated current of the AC drive is 150A and no-load current of the motor is 40A,
then Pr.7-03 should be set to 27%.
This parameter is used with slip compensation Pr.7-04 and Pr.7-05. An incorrect setting will
cause the function to work incorrectly and may damage the motor and drive.
If the no-load current of the motor is unavailable, it may be found by running the motor with no
load and reading the current on the keypad display.
07 - 04
Auto Slip Compensation Gain
Unit: 0.1
Settings
0.0~3.0
Factory Setting: 0.0
This parameter is set to auto slip compensation gain.
Rotor speed of the motor (output frequency of AC drive) can’t synchronize due to induction
motor characteristic. The difference between synchronization speed and rotor speed is called
slip frequency. Slip frequency is in direct proportion with output torque and output current.
Therefore, slip compensation could make rotor speed and master frequency command the
same according output current (lo).
The equation of slip compensation is (07-05) X (07-04) X (Io-(07-03)) / ((07-02)-(07-03)). If
rated current of AC drive is 150A, full-load current of the motor is 120A, no-load current is 40A,
rated slip frequency is 5Hz and output current of AC drive is 100A. At this time, slip
compensation is (07-04) X 5 X (100-40) / (120-40) = 3.75 X (07-04). If 07-04 is set to 1.0 and
the compensation is 3.75. If master frequency command is set to 50Hz and output frequency is
53.75.
Output frequency after compensation is limited by 01-07 upper bound frequency. When using
slip compensation, 01-07 should be set to the suitable value.
When PID feedback control, slip compensation function will be disabled.
Unsuitable setting value may cause over compensation.
Содержание AC Motor Drive VFD-G
Страница 1: ......
Страница 2: ......
Страница 3: ......
Страница 17: ...Chapter 1 Introduction 1 8 Revision July 2008 EG03 SW V1 06 For 150 215HP Frame G Step 1 Step 2 Step 3 Step 4...
Страница 18: ...Chapter 1 Introduction Revision July 2008 EG03 SW V1 06 1 9 For 250 300HP Frame H Step 1 Step 2 Step 3 Step 4...
Страница 23: ...Chapter 1 Introduction 1 14 Revision July 2008 EG03 SW V1 06 This page intentionally left blank...
Страница 45: ...Chapter 2 Installation and Wiring 2 22 Revision July 2008 EG03 SW V1 06 This page intentionally left blank...
Страница 51: ...Chapter 3 Keypad and Start Up 3 6 Revision July 2008 EG03 SW V1 06 This page intentionally left blank...
Страница 141: ...Chapter 4 Parameters 4 90 Revision July 2008 EG03 SW V1 06 This page intentionally left blank...