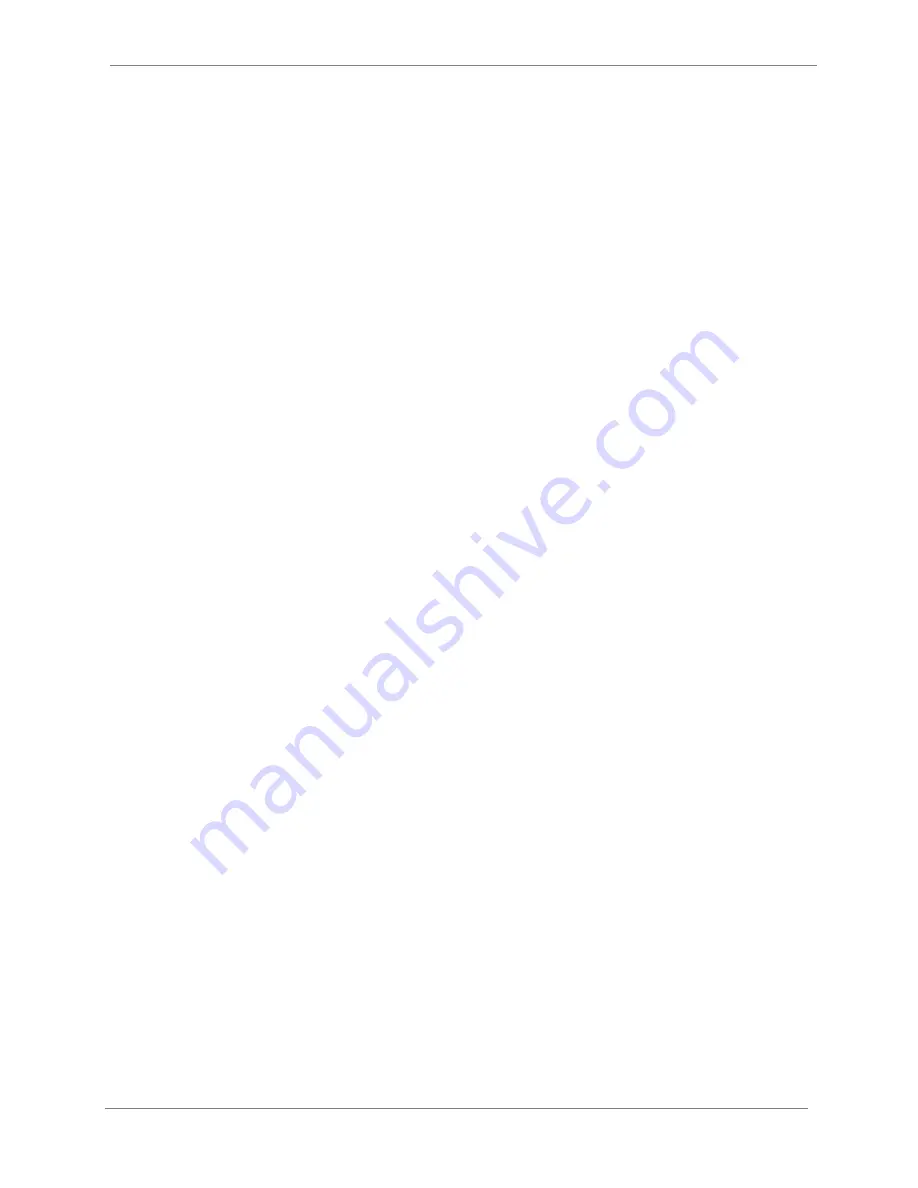
Rooster™
Sensor200 USER MANUAL
Rooster™
Sensor200 USER MANUAL 62360MN000-A00
12 of 40
Once Control Output is enabled, the user needs to enter or select:
1.
Setpoint, desired face velocity or volumetric flow (if volumetric flow is enabled) and
2.
Output
a.
0-20 mA
b.
4-20 mA
c.
0-5 V
d.
0-10 V
Proportional and integral terms are also available for the user to tune the output control loop.
The proportional gain, P term, determines the ratio of the output response to the error signal.
The user can adjust this value based on stability of the airflow. Proportional gain can be any
decimal value between 0 and 9999, and the default value for P term is 0.50.
The primary purpose of the integral term is to eliminate the small steady-state error between
process flow and the setpoint. It produces a correction based on the error over time. The
integral term can be any decimal value between 0 and 9999, and the default value for I term is
0.20.
Scaled Output
Scaled Output provides a control signal proportional to the face velocity or volumetric flow.
Scaled Output is typically used to change the position of a damper in a VAV (variable air
volume) system or control fan speed. Once Scaled Output is enabled, the user needs to enter or
select:
1.
Output
a.
0-20 mA
b.
4-20 mA
c.
0-5 V
d.
0-10 V
2.
Max Scale, upper limit of scale
For example, with:
▪
Output set to 0-5 V,
▪
Max Scale set to 10 m/s, and
▪
flow in the cabinet set such that 5 m/s is displayed on the Rooster
TM
the analog out voltage will be 2.5 volts.