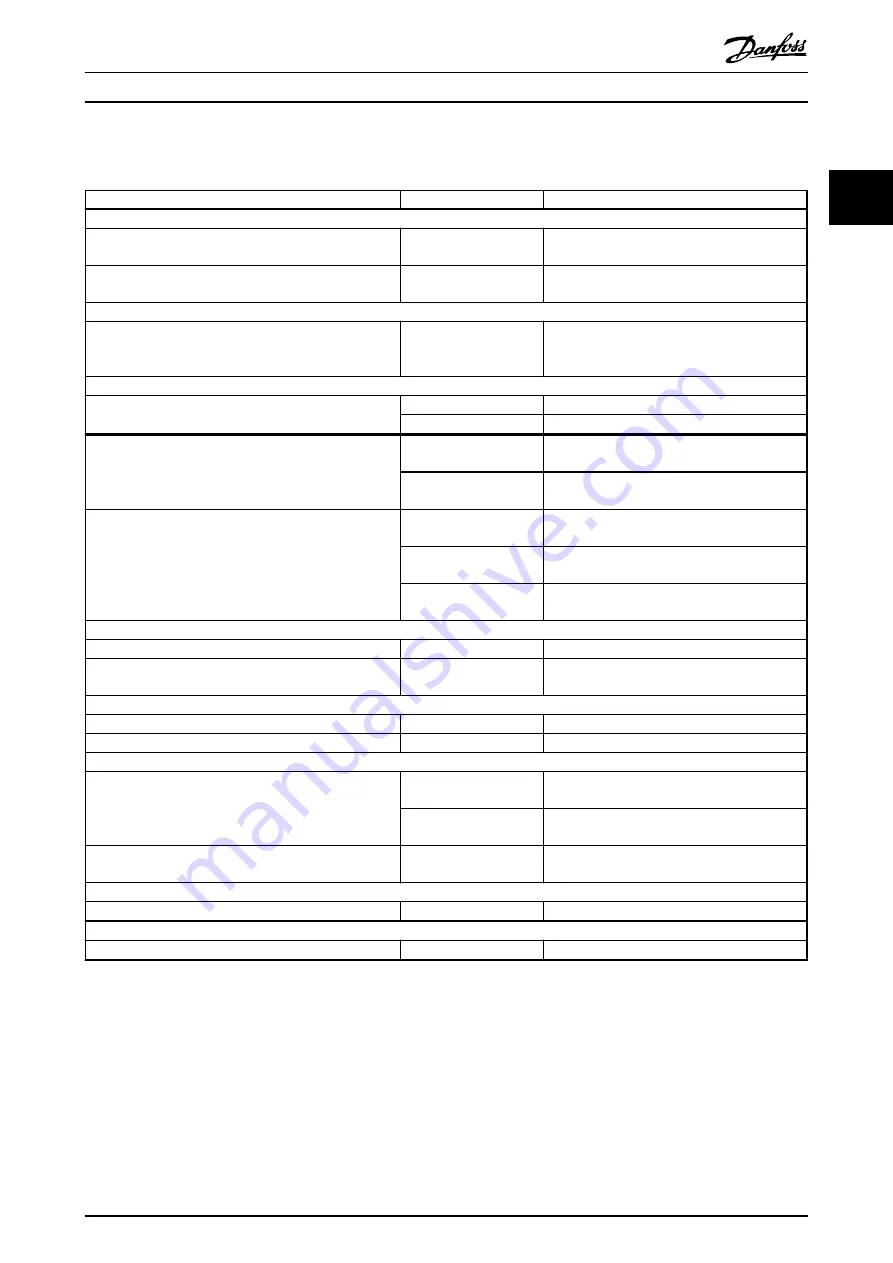
Follow the steps in
to programme the speed control (see explanation of settings in the
Programming Guide
)
In
it is assumed that all other parameters and switches remain at their default setting.
Function
Parameter number
Setting
1) Make sure the motor runs properly. Do the following:
Set the motor parameters using the data on the name
plate.
1-2* Motor Data
As specified by motor name plate.
Perform an Automatic Motor Adaptation.
1-29 Automatic Motor
Adaption (AMA)
[1] Enable complete AMA
2) Check the motor is running and the encoder is attached properly. Do the following:
Press [Hand On]. Check that the motor is running and note
in which direction it is turning (henceforth referred to as
the “positive direction”).
Set a positive reference.
3) Make sure the frequency converter limits are set to safe values:
Set acceptable limits for the references.
3-02 Minimum Reference
0
3-03 Maximum Reference
50
Check that the ramp settings are within frequency
converter capabilities and allowed application operating
specifications.
3-41 Ramp 1 Ramp Up
Time
default setting
3-42 Ramp 1 Ramp Down
Time
default setting
Set acceptable limits for the motor speed and frequency.
4-12 Motor Speed Low
Limit [Hz]
0 Hz
4-14 Motor Speed High
Limit [Hz]
50 Hz
4-19 Max Output
Frequency
60 Hz
4) Configure the speed control and select the motor control principle:
Activation of speed control
1-00 Configuration Mode
[1] Speed closed loop
Selection of motor control principle
1-01 Motor Control
Principle
[1] VVC
+
5) Configure and scale the reference to the speed control:
Set up analog input 53 as a reference source.
3-15 Reference 1 Source
Not necessary (default)
Scale analog input 53 0 RPM (0 V) to 50 RPM (10 V)
6-1* Analog Input 1
Not necessary (default)
6) Configure the 24 V HTL encoder signal as feedback for the motor control and the speed control:
Set up digital input 32 and 33 as encoder inputs.
5-14 Terminal 32 Digital
Input
[82] Encoder input B
5-15 Terminal 33 Digital
Input
[83] Encoder input A
Choose terminal 32/33 as speed PID feedback.
7-00 Speed PID Feedback
Source
[1] 24 V Encoder
7) Tune the speed control PID parameters:
Use the tuning guidelines when relevant or tune manually. 7-0* Speed PID Ctrl.
8) Finish:
Save the parameter setting to the LCP for safe keeping
0-50 LCP Copy
[1] All to LCP
Table 2.6 Programming Order for Speed PID Control
Product Overview
Design Guide
MG06B402
Danfoss A/S © 09/2014 All rights reserved.
31
2
2