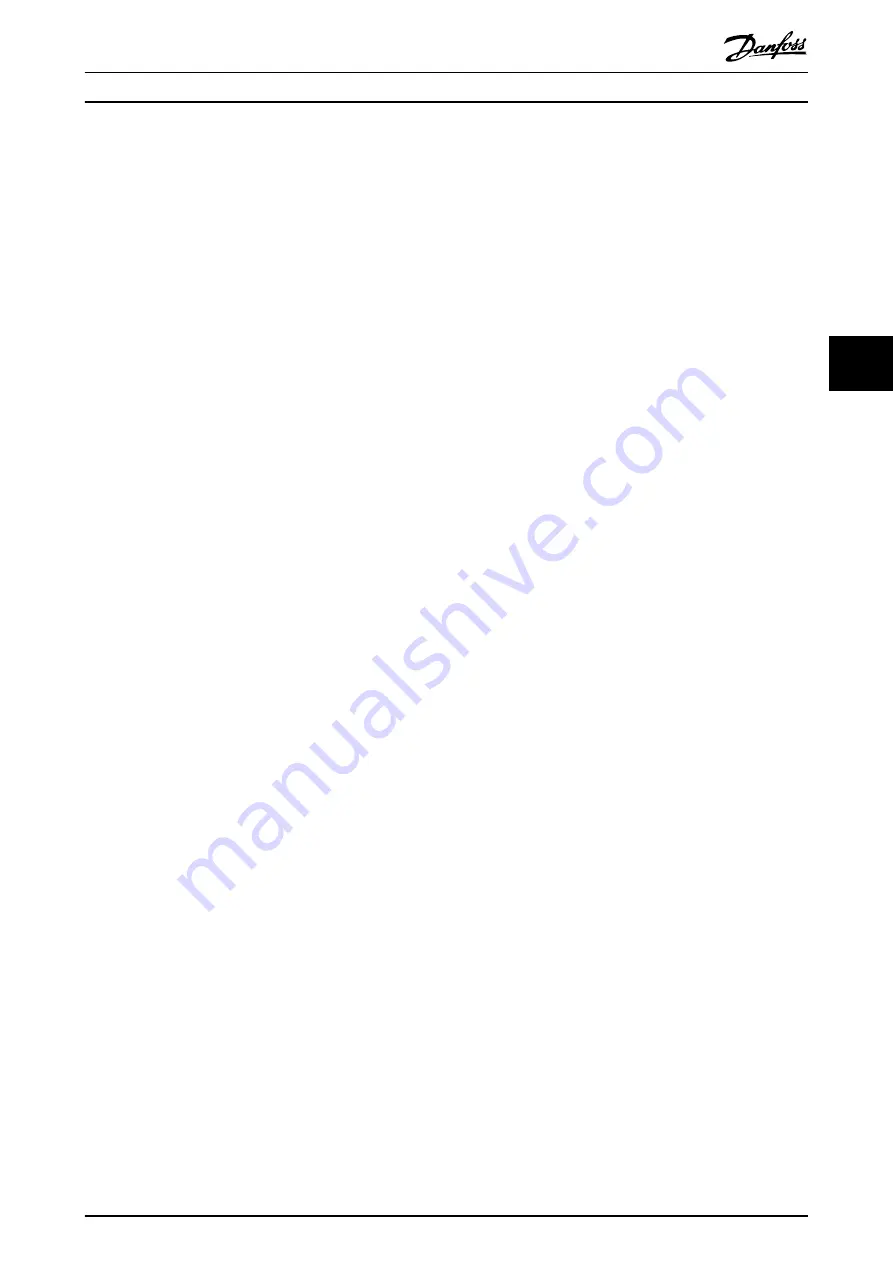
5.2.9 Frequency Bypass
In some applications, the system can have operational
speeds that create a mechanical resonance. This
mechanical resonance can generate excessive noise and
possibly damage mechanical components in the system.
The frequency converter has 4 programmable bypass-
frequency bandwidths. These bandwidths allow the motor
to step over speeds which induce system resonance.
5.2.10 Motor Preheat
To preheat a motor in a cold or damp environment, a small
amount of DC current can be trickled continuously into the
motor to protect it from condensation and a cold start.
This function can eliminate the need for a space heater.
5.2.11 4 Programmable Set-ups
The frequency converter has 4 set-ups which can be
independently programmed. Using multi-setup, it is
possible to switch between independently programmed
functions activated by digital inputs or a serial command.
Independent set-ups are used, for example, to change
references, or for day/night or summer/winter operation, or
to control multiple motors. The active set-up is shown on
the LCP.
Set-up data can be copied from frequency converter to
frequency converter by downloading the information from
the removable LCP.
5.2.12 DC Braking
Some applications can require braking a motor to slow or
stop it. Applying DC current to the motor brakes the motor
and can eliminate the need for a separate motor brake.
The DC brake can be set to activate at a predetermined
frequency or after receiving a signal. The rate of braking
can also be programmed.
5.2.13 High Breakaway Torque
For high inertia or high friction loads, extra torque is
available for starting. The breakaway current of 110% or
160% of maximum can be set for a limited amount of
time.
5.2.14 Bypass
An automatic or manual bypass is an available option. The
bypass allows the motor to operate at full speed when the
frequency converter is not operating and allows for routine
maintenance or emergency bypass.
5.2.15 Power Loss Ride-through
During a power loss, the frequency converter continues to
rotate the motor until the DC link voltage drops below the
minimum operating level, which corresponds to 15%
below the lowest rated drive voltage. Frequency converters
are rated for operation on 380–460 V, 550–600 V, and
some at 690 V. The power loss ride-through time depends
after the load on the frequency converter and the mains
voltage at the time of the power loss.
5.2.16 Overload
When the torque required to maintain or accelerate to a
determined frequency exceeds the current limit, the
frequency converter attempts to continue operating. It
automatically reduces the rate of acceleration or reduces
the output frequency. If the overcurrent demand is not
reduced enough, the frequency converter shuts down and
shows a fault within 1.5 s. The current limit level is
programmable. The overcurrent trip delay is used to
specify the time that the frequency converter operates in
current limit before shutting down. The limit level can be
set from 0–60 s, or for infinite operation, subject to the
frequency converter and motor thermal protection.
5.3 Safe Torque Off (STO)
The VLT
®
AutomationDrive FC 302 comes standard with
Safe Torque Off functionality via control terminal 37. The
STO function is also available on VLT
®
HVAC Drive FC 102
and VLT
®
AQUA Drive FC 202.
STO disables the control voltage of the power semicon-
ductors of the frequency converter output stage, which in
turn prevents it from generating the voltage required to
rotate the motor. When the Safe Torque Off (T37) is
activated, the frequency converter issues an alarm, trips
the unit, and coasts the motor to a stop. Manual restart is
required. The Safe Torque Off function can be used for
stopping the frequency converter in emergency stop
situations. In the normal operating mode when Safe
Torque Off is not required, use the regular stop function
instead. When automatic restart is used, the requirements
according to ISO 12100-2 paragraph 5.3.2.5 must be
fulfilled.
The Safe Torque Off function with VLT
®
AutomationDrive
FC 302 can be used for asynchronous, synchronous, and
permanent magnet motors. It is possible that 2 faults occur
in the power semiconductors. If 2 faults in the power
semiconductors occur while using synchronous or
permanent magnet motors, it can cause a residual rotation
in the motor. The rotation can be calculated to angle=360/
(number of poles). The application using synchronous or
permanent magnet motors must take this possibility into
consideration and ensure that this scenario is not a critical
Product Features
Design Guide
MG37N102
Danfoss A/S © 6/2016 All rights reserved.
19
5
5