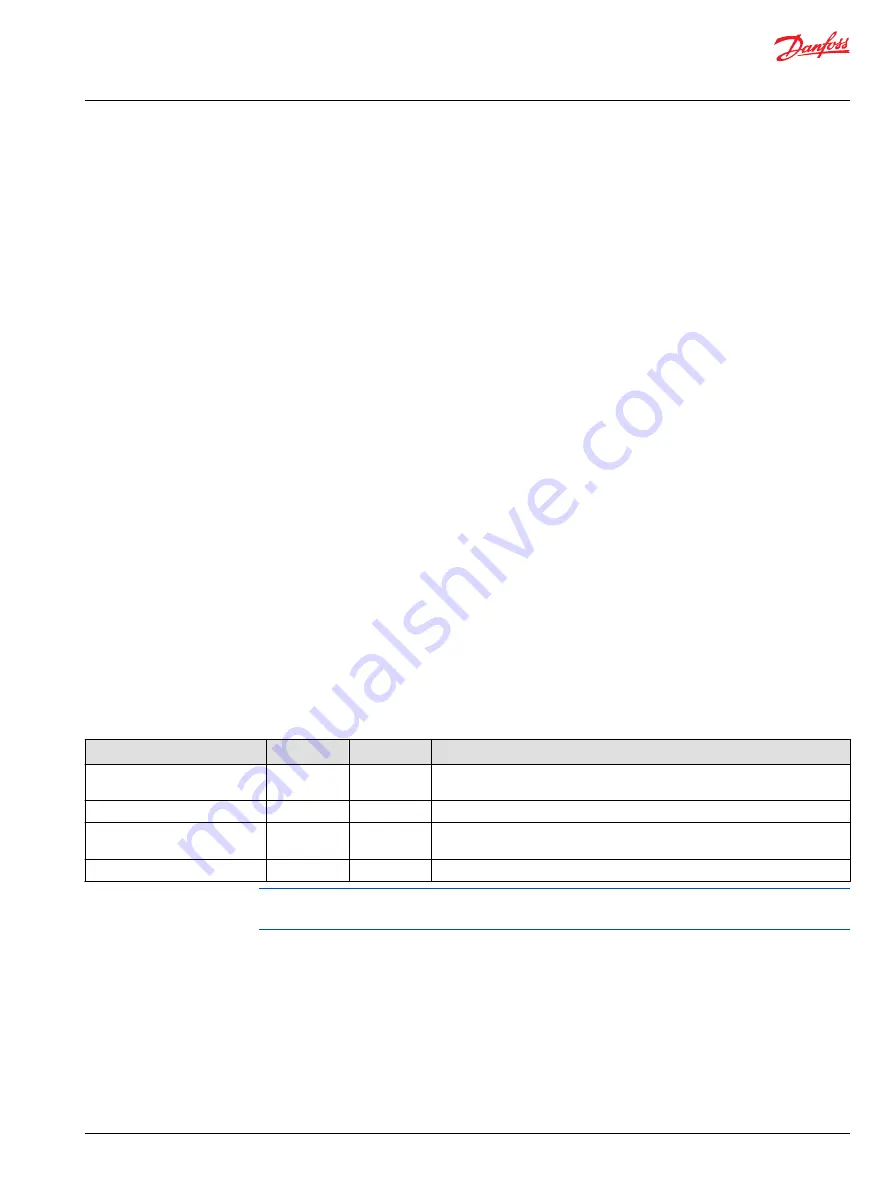
The auto-steering functionality always uses closed loop control, hence the steered wheel or articulation
angle is read back to the PVED-CL, and used for control purposes to ensure correct positioning.
The functionality available in the PVED to steer by any curvature set-point controller is defined by
mapping the External Set-point Controller and a Steered Wheel Sensor according to
on page 31. As soon as these parameters are set, it is ready to run, but it is strongly recommended
to have a steering wheel sensor to disengage auto-steering just by turning the steering wheel.
Alternatively the power supply must be interrupted, or guidance message flagged as ‘Not intended for
steering’.
Trimming the System
To optimize the system functionality, ensure the parameters above were set correctly. If this was not
enough, try changing the parameters below.
Kp This parameter is closely related to valve capacity, stroke volume and amplifies the error between set-
point and current position. The optimum value for Kp is found when a non-lagging, accurate, non-
oscillating steering actuation without overshoot is achieved at:
•
Extreme low and high oil viscosities as specified in
•
Low and near max steering pressure when driving at low, high vehicle speed and reversed gear
The default value fits to steering systems with a lock-to-lock time of 2 seconds at max port flow.
Qm Sets the maximum port flow. It effects the speed of the steering actuator to move towards the set
point position. Negative values of Qm are interpreted as the positive equivalent.
The default value is set equal to the inherent max port flow capacity of the valve and will therefore not
have any effect.
Ampl Factor that ‘amplifies’ the set-point. Used if the steered angle is always too small or too larger. It
applies to both sides, hence if the angle is too large left, and too small right, this factor cannot solve it –
that will probably be a steered wheel sensor calibration error.
ClosedLoopXspOffset Spool position offset which is added to spool position command to eliminate any
spool overlap. The offset ensures that the spool is always operated in a range where the valve outputs a
flow. This is especially important for auto-steering applications where any control error shall generate a
flow to correct the error.
Symbol
Index
Default
Value range
Kp
508
50
0 to 200
(0.00 to 2.00 % flow capacity of the valve for 0.1 % positional error)
Qm
5y27
1000
0 to 1000 (0.0 to 100.0% of max port flow)
Ampl
5y37
1000
0 to 2000
(Factor 0.001; Setpoint from 0 to 2 times the setpoint message value)
ClosedLoopXspOffset
748
0
0 to 1000 (0 to ±7 mm)
Kp and ClosedLoopXspOffset correlates. By increasing ClosedLoopXspOffset, the proportional gain may
be reduced. It is recommended to first set ClosedLoopXspOffset to 20 and then tune Kp.
Noise due to Frequent Pressure Build-up
Eliminating noise is accomplished by stopping the controller to respond to minor deviations between set
point and current actuator position. The spool inside the valve is set in neutral when the port flow
command has been within a threshold value (Qth) for a given time (Tclpout). The spool is reactivated
again when port flow command exceeds the threshold value.
Tclpout Sets the time delay (ms) before the main spool is set in neutral.
Qth Sets the threshold value for port flow command when the controller is in steady state.
Operation Manual
PVED-CL Controller for Electro-Hydraulic Steering, Version 1.38
Auto-steering
©
Danfoss | May 2016
11025583 | AQ00000216en-US0302 | 95