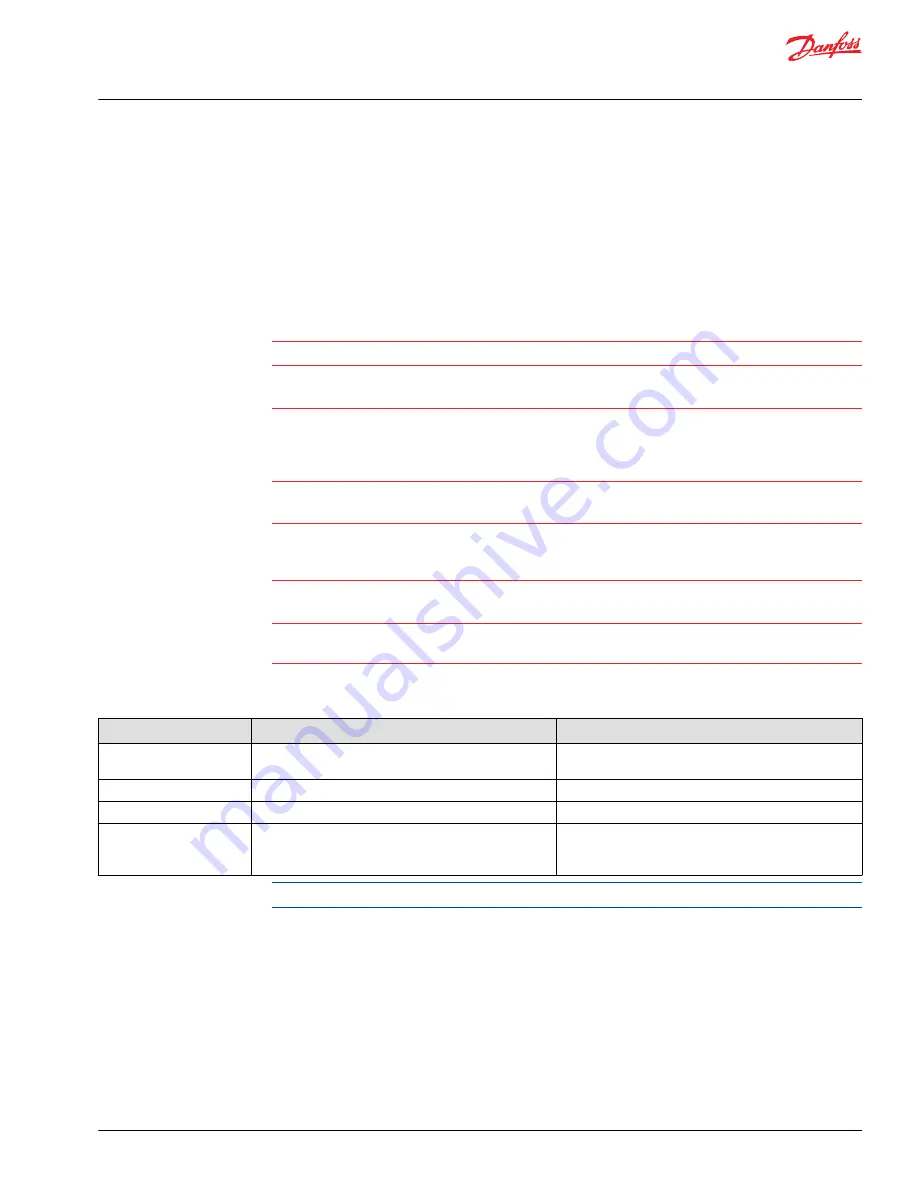
Overview
This section provides general steps to follow if you observe undesirable system conditions. Follow the
steps listed until you solve the problem. Some of the items are system specific. We reference the section
in this manual of more information is available. Always observe the safety precautions listed in safety
precautions related to your specific equipment.
Safety precautions
C
Caution
High inlet vacuum causes cavitation which can damage internal pump components.
W
Warning
Escaping hydraulic fluid under pressure can have sufficient force to penetrate your skin causing serious
injury and/or infection and may be hot enough to cause burns. Relieve pressure in the system before
removing hoses, fittings, gauges, or components. Seek immediate medical attention if you are cut or
burned by hydraulic fluid.
W
Warning
Unintended movement of the machine or mechanism may cause injury to the technician or bystanders.
To protect against unintended movement, secure the machine or disable/disconnect the mechanism
while servicing.
C
Caution
Contamination can damage internal components and void the manufacturer's warranty. Take
precautions to ensure system cleanliness when removing and reinstalling system components and lines
Electrical troubleshooting
Item
Description
Action
Control operates pump in
one direction only
Control coil failure.
Measure resistance at coil pins. Resistance should be 14.2W
(24V) or 3.66W (12V) at 20° C [70° F]. Replace coil.
No pump function
No power to controller.
Restore power to controller.
Erratic pump function
Electrical connection to pump is bad.
Disconnect connection, check wires, reconnect wires.
Erratic or no machine
function
External controller malfunction or hydraulic system
problem.
Verify external controller problem using spare controller.
Replace controller. Check hydraulic system fluid level/
pressures/filters/etc. Fix hydraulic system problems.
If available, use a manual override to check proper pump operation and verify electrical problem.
Service Manual
H1 45/53/60/68 Tandem Closed Circuit Axial Piston Pumps
Troubleshooting
©
Danfoss | June 2018
520L0928 | AX00000103en-US0303 | 29