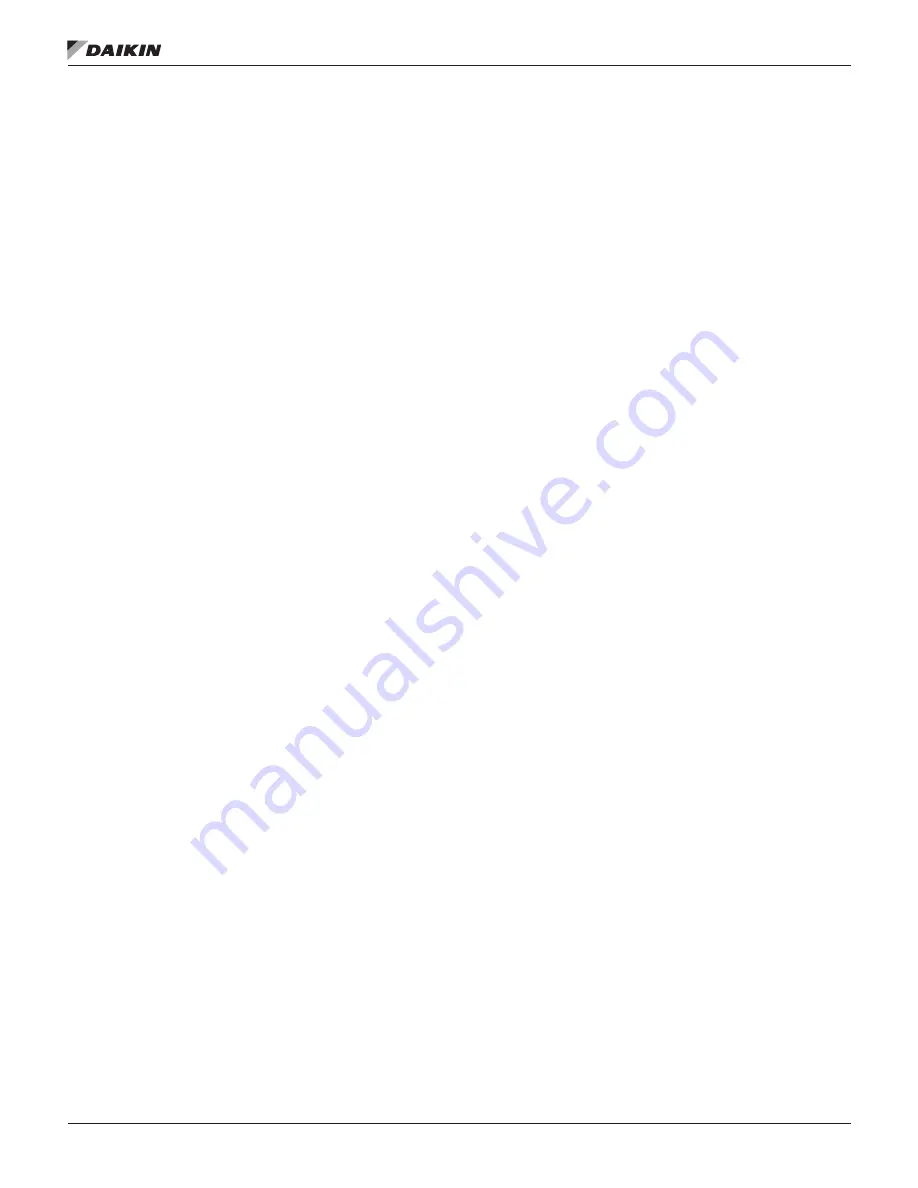
Maintenance
www.DaikinApplied.com 65
IOM 1281-2 • CENTRIFUGAL WATER CHILLERS
and vessels can rupture these parts if subjected to freezing
temperature.
Forced circulation of antifreeze through the water circuits is
one method of avoiding freeze up.
1.
Take measures to prevent the shutoff valve in the water
supply line from being accidentally turned on.
2. If a cooling tower is used, and if the water pump will be
exposed to freezing temperatures, be sure to remove the
pump drain plug and leave it out so any water that can
accumulate will drain away.
3. Open the compressor disconnect switch, and remove the
fuses. If the transformer is used for control voltage, the
disconnect must remain on to provide power to the oil
heater. Set the manual UNIT ON/OFF switch in the Unit
Control Panel to the OFF position.
4. Check for corrosion and clean and paint rusted surfaces.
5.
Clean and flush water tower for all units operating on a
water tower. Make sure tower blowdown or bleed-off is
operating. Set up and use a good maintenance program
to prevent “liming up” of both tower and condenser. It
should be recognized that atmospheric air contains
many contaminants that increase the need for proper
water treatment. The use of untreated water can result
in corrosion, erosion, sliming, scaling or algae formation.
It is recommended that the service of a reliable water
treatment company be used. Daikin Applied assumes no
responsibility for the results of untreated or improperly
treated water.
6. Remove condenser heads at least once a year to inspect
the condenser tubes and clean if required.
Annual Startup
A dangerous condition can exist if power is applied to a
faulty compressor motor starter that has been burned out.
This condition can exist without the knowledge of the person
starting the equipment.
This is a good time to check all the motor winding resistance
to ground. Semi-annual checking and recording of this
resistance will provide a record of any deterioration of the
winding insulation. All new units have well over 100 megohms
resistance between any motor terminal and ground.
Whenever great discrepancies in readings occur, or uniform
readings of less than 50 megohms are obtained, the motor
cover must be removed for inspection of the winding prior to
starting the unit. Uniform readings of less than 5 megohms
indicate motor failure is imminent and the motor should be
replaced or repaired. Repair before failure occurs can save a
great deal of time and labor spent in the cleanup of a system
after a motor burnout.
1. The control circuit must be energized at all times, except
during service. If the control circuit has been off and oil is
cool, energize oil heaters and allow 24 hours for heater
to remove refrigerant from the oil before starting.
2. Check and tighten all electrical connections.
3. Replace the drain plug in the cooling tower pump if it was
removed at shutdown time the previous season.
4. Install fuses in main disconnect switch (if removed).
5. Reconnect water lines and turn on supply water. Flush
condenser and check for leaks.
Repair of System
Pressure Relief Valve Replacement
Current condenser designs use two relief valves separated
by a three-way shutoff valve (one set). This three-way valve
allows either relief valve to be shut off, but at no time can both
be shut off. In the event one of the relief valves are leaking in
the two valve set, these procedures must be followed:
• If the valve closest to the valve stem is leaking, back
seat the three-way valve all the way, closing the port to
the leaking pressure relief valve. Remove and replace
the faulty relief valve. The three-way shutoff valve must
remain either fully back seated or fully forward to normal
operation. If the relief valve farthest from the valve stem
is leaking, front seat the three-way valve and replace the
relief valve as stated above.
• The refrigerant must be pumped down into the condenser
before the evaporator relief valve can be removed.
Pumping Down
If it becomes necessary to pump the system down, extreme
care must be used to avoid damage to the evaporator from
freezing. Always make sure that full water flow is maintained
through the chiller and condenser while pumping down. To
pump the system down, close all liquid line valves. With
all liquid line valves closed and water flowing, start the
compressor. Set the MicroTech II control to the manual load.
The vanes must be open while pumping down to avoid a surge
or other damaging condition. Pump the unit down until the
MicroTech II controller cuts out at approximately 20 psig. It is
possible that the unit might experience a mild surge condition
prior to cutout. If this should occur, immediately shut off the
compressor. Use a portable condensing unit to complete the
pump down, condense the refrigerant, and pump it into the
condenser or pumpout vessel using approved procedures.
A pressure regulating valve must always be used on the drum
being used to build the system pressure. Also, do not exceed
the test pressure given above. When the test pressure is
reached disconnect the gas cylinder.
Pressure Testing
No pressure testing is necessary unless some damage was
incurred during shipment. Damage can be determined upon
a visual inspection of the exterior piping, checking that no
breakage occurred or fittings loosened. Service gauges should
show a positive pressure. If no pressure is evident on the
gauges, a leak may have occurred, discharging the entire
refrigerant charge. In this case, the unit must be leak tested to
determine the location of the leak.
Leak Testing
Содержание WDC
Страница 4: ......
Страница 21: ...Installation www DaikinApplied com 21 IOM 1281 2 CENTRIFUGAL WATER CHILLERS Figure 16 Field Wiring Schematic...
Страница 22: ...IOM 1281 2 CENTRIFUGAL WATER CHILLERS 22 www DaikinApplied com Installation Figure 17 Compressor Control Box...
Страница 23: ...Installation www DaikinApplied com 23 IOM 1281 2 CENTRIFUGAL WATER CHILLERS Figure 18 Unit Control Box...
Страница 38: ...IOM 1281 2 CENTRIFUGAL WATER CHILLERS 38 www DaikinApplied com Operation Figure 39 Unit Detail View Screen...
Страница 72: ......