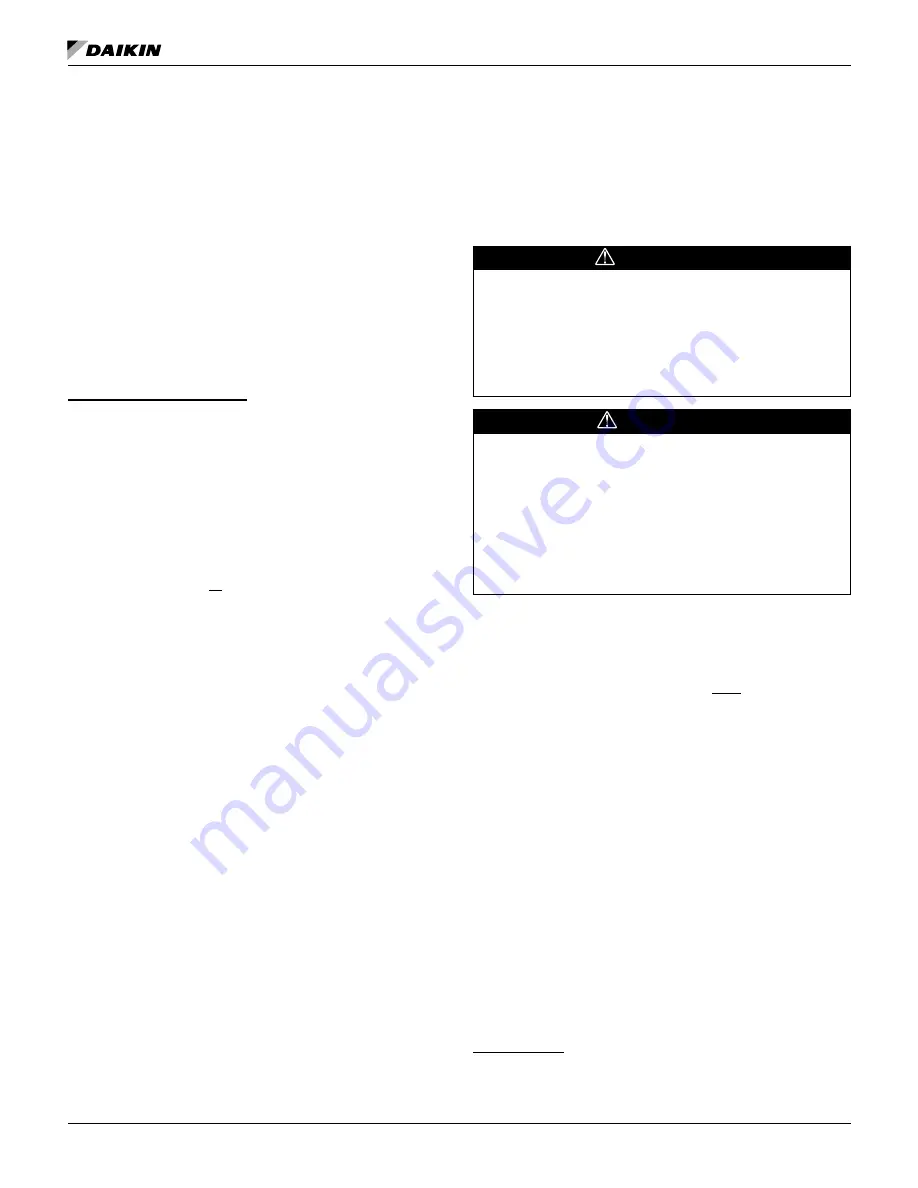
I
nsTallaTIon
www.DaikinApplied.com 17
IOM 1266-2 • MAGNITUDE
®
MODEL WME CHILLERS
5. Remove the following wires coming from the VFD:
• 350V DC power supply (gray cable)
• power leads on the top of the motor housing
6. Remove the Ethernet cable coming from unit control box.
7. Remove the wireway box assembly from the compressor
to the back of the starter.
8. Loosen the (4) bolts from the compressor’s bottom
, flag #8).
NOTE:
Do not loosen or remove bolts securing the
compressor brackets as height is pre-set from
the factory.
9. Use front tapped lifting hole on the compressor motor
housing (see
flag #9)
to
rig compressor for
and unit rigging instructions in
.
Compressor Re-Attachment
1. Set the suction elbow back on top of the evaporator and
install the bolts/screws loosely at the evaporator flange.
Use new O-rings provided.
2. Set the discharge piping back on top of the condenser
and install the bolts loosely at the condenser flange. Use
the new gasket supplied with the unit.
3. Set compressor on mounting brackets and install the (4)
mounting bolts loosely. Reconnect the discharge nozzle
with new O-rings provided and also at the suction elbow.
NOTE:
For steps 4-6, all bolts need to be installed loosely
first before final torque is applied.
4. Install (12) bolts/screws at suction elbow to compressor
and torque to 25 ft-lbs max; do not over-tighten.
5.
Install (18) bolts at evaporator flange to the suction line
and torque to 62 ft-lbs max; do not over-tighten.
6. Install and torque the (8) bolts at the discharge nozzle
to 205 ft-lbs, then torque the (8) bolts at the condenser
flange to the same.
7. Torque the (4) compressor mounting bolts to 25 ft-lbs
max; do not over-tighten.
8.
Re-install the (4) flange bolts at the hot gas bypass line.
9. Re-install the wireway between compressor and VFD.
10. Re-attach all associated power wiring & Ethernet cable.
11. Re-attach rotor cooling return line on the underside of
the compressor motor housing along with both liquid
injection lines.
12. Pull vacuum at evaporator and compressor to 300
microns and perform a standing hold to verify no
moisture or leaks - do not allow rise of 300 microns
within 1 hour.
13.
After verifying that pumps are running and water flow
has been established on both evaporator and condenser,
add vapor refrigerant to bring the saturated temperature
above freezing. Open all valves.
14. Perform refrigerant leak check to ensure all connections
and fittings are securely fastened.
Water Piping
All evaporators and condensers have OGS-type grooved water
connections (adhering to Standard AWWA C606) or optional
flange connections. The installing contractor must provide
matching mechanical connections. Be sure that water inlet
and outlet connections match certified drawings and nozzle
markings. PVC/CPVC piping should not be used.
WARNING
Polyolester Oil, commonly known as POE oil is a synthetic
oil used in many refrigeration systems, and may be present
in this Daikin product. POE oil, if ever in contact with PVC/
CPVC, will coat the inside wall of PVC/CPVC pipe causing
environmental stress fractures. Although there is no PVC/
CPVC piping in this product, please keep this in mind when
selecting piping materials for your application, as system
failure and property damage could result.
CAUTION
If welding is to be performed on the mechanical or flange
connections:
1. Remove the solid-state temperature sensor, thermostat
bulbs, and nozzle mounted flow switches from the wells
to prevent damage to those components.
2. Properly ground the unit or severe damage to the
MicroTech
®
unit controller can occur.
NOTE:
ASME certification will be revoked if welding is
performed on a vessel shell or tube sheet.
The water heads can be interchanged (end for end) so that
the water connections can be made at either end of the unit.
If this is done, use new head gaskets and relocate the control
sensors.
Field installed water piping to the chiller must include:
• air vents at the high points.
• a cleanable water strainer upstream of the evaporator
and condenser inlet connections.
•
a flow proving device for both the evaporator and
condenser to prevent freeze up. Flow switches, thermal
dispersion switches, or Delta P switches can be used.
Note that flow switches are factory installed. Additional
flow switches can be used only if they are connected in
series with the ones already provided. Connect additional
flow switches in series between original flow switch
inputs. Calibration of thermal dispersion flow switches is
•
sufficient shutoff valves to allow vessel isolation. The
chiller must be capable of draining the water from the
evaporator or condenser without draining the complete
system.
• Piping must be supported to eliminate weight and strain
on the fittings and connections.
• Chilled water piping must be adequately insulated.
Recommended
field installed chiller water piping includes:
• thermometers at the inlet and outlet connections of both
vessels.
Содержание Magnitude WME Series
Страница 4: ...Intentionally Left Blank...