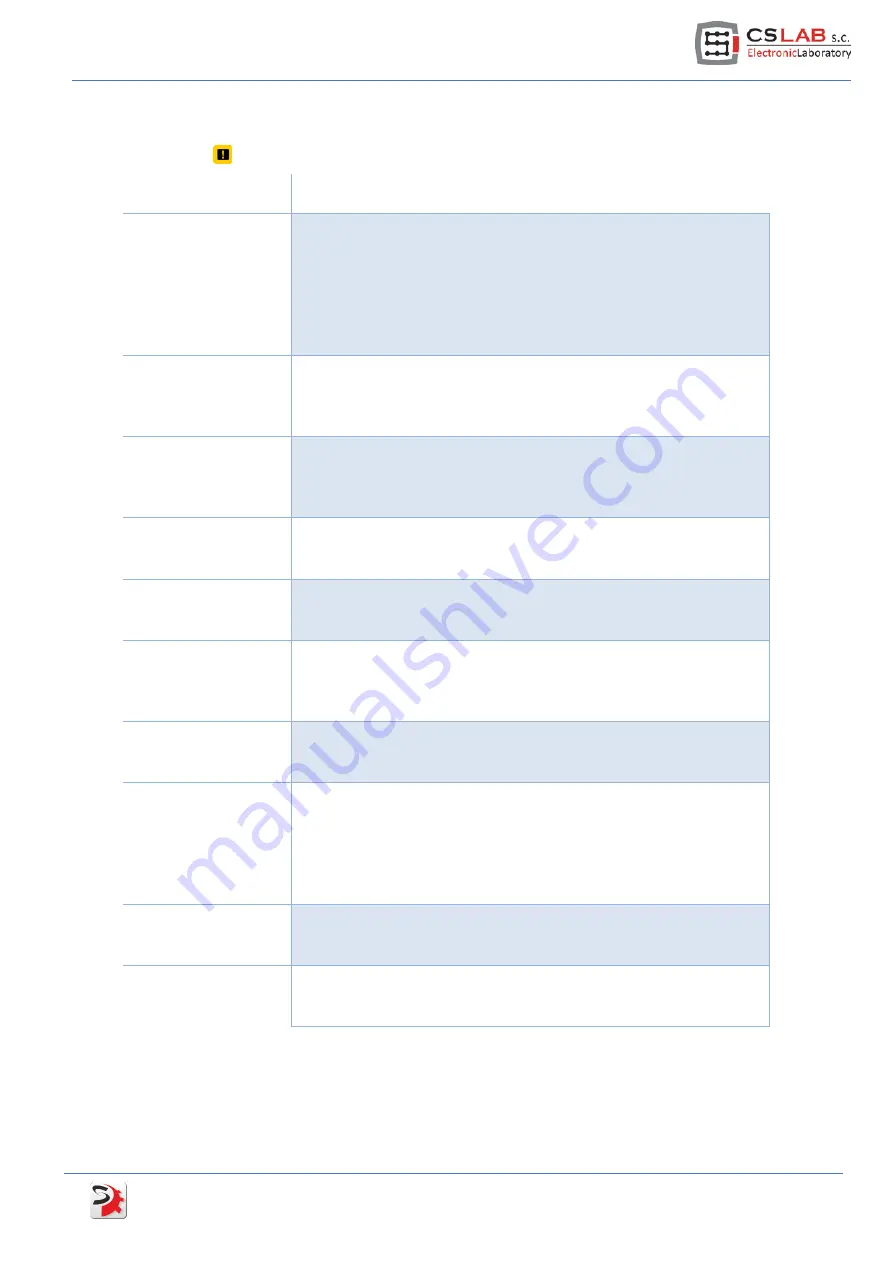
6.
Drive alarm flags description
You can open current alarms and warnings information window from the menu “Tools
→
show
alarms” or click icon from the toolbar.
Alarm name
Description
To high voltage on a
DC bus
Overvoltage on a power output stage DC circuit. The alarm shows
up when we power the power output stage with too high voltage
or if energy received from a motor during braking raises power
supply voltage up. In the second situation we should decrease
acceleration in a CNC controller, increase capacitors capacitance in
a power supply or to use a special power module by CS-Lab
company that allows for braking resistor connection.
Motor overload
Overload. Motor input current was exceeded for too long
(chapter 7 - „Drive overload characteristic”. This may mean to
large mechanical overload, motor breakdown or parameters of a
motor are set incorrectly.
(!) Over current
protection
Short circuit alarm. Means: power supply wires short circuit,
motor malfunction, power output stage malfunction.
It may also appear at incorrectly set current PID regulator or very
rapid acceleration/deceleration.
Power output stage
overheat
It means driver overheat. You should wait till the driver cools
down and if the problem persists then you assure better cooling
for the driver and a control cabinet.
Following error
(velocity controller)
Rotational speed of a motor differs too much from the set speed It
means to high revs or incorrectly set motor parameters or PID
regulators.
To low voltage on a
DC bus
Power supply voltage of a power output stage is too low. This
alarm also occurs if HV voltage wasn’t entered, also at too weak
power supply or if power supply of a power outputs stage is
broken.
Following error
(position controller)
A driver wasn’t able to keep set positioning tolerance. You should
check settings of a max. following error in a PID tuning settings or
correct acceleration/braking ramps in a CNC controller.
Error state of HALL
sensors
Incorrect HALL sensors read-outs. Some sensor can be broken or
(more often) connection faults, a bad quality wire or a shield
incorrect connection. The error appears also when we have
connected DC motor and we still do not have a drive reconfigured.
In this case you should set a motor type and save the settings and
next turn the drive 24V power supply off and on.
Rotor positioning
error
A rotor positioning terror. Unsuccessful procedure of a rotor
position definition after power is turned on. Verify motor settings
and connection.
Unsuccessful
calibration of LEM
sensors!
LEM current sensors unsuccessful calibration. Contact with service.
simDrive™ AC Servo Drive -
U
SER
G
UIDE
43
Содержание SimDrive M4-H040K
Страница 1: ...Applies to hardware version v1 Applies to firmware version v2 00 Rev 1 0 copyright 2014 CS Lab s c...
Страница 9: ...2 1 Brushless motors AC BLDC simDrive AC Servo Drive USER GUIDE 9...
Страница 10: ...2 2 Brushed motors DC 10 simDrive AC Servo Drive User Guide...
Страница 17: ...4 1 4 Digital inputs IN0 IN5 4 1 5 Digital outputs OUT0 OUT2 simDrive AC Servo Drive USER GUIDE 17...