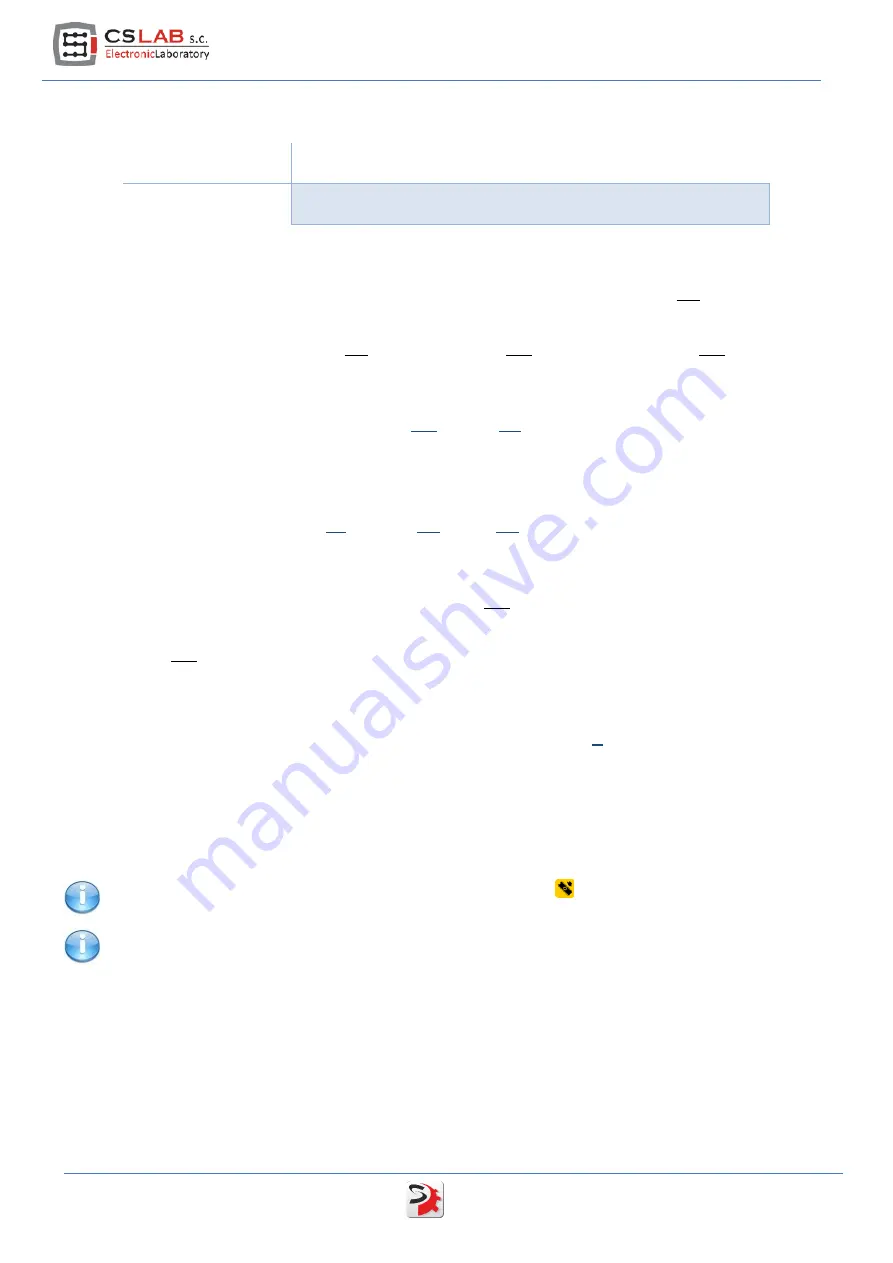
5.4.7
Reference signal (STEP/DIR)
5.4.8
Electronic gearing
Sometimes the connected motor have a high resolution encoder - e.g.
40000
𝑖𝑚𝑝
𝑟𝑒𝑣
and a CNC
controller is not able to provide STEP signal with enough frequency to fully exploit motor revs range.
As an example: motor with 4
0000
𝑖𝑚𝑝
𝑟𝑒𝑣
encoder has
3000
𝑟𝑒𝑣
𝑚𝑖𝑛
.
nominal revs and
5000
𝑟𝑒𝑣
.
𝑚𝑖𝑛
.
maximal
revs.
5000
𝑟𝑒𝑣
.
𝑚𝑖𝑛
.
=
83,33
𝑟𝑒𝑣
.
𝑠𝑒𝑐
.
Now we can easily calculate max. frequency of STEP signal:
83,33
𝑟𝑒𝑣
𝑠𝑒𝑐
× 40000
𝑖𝑚𝑝
𝑟𝑒𝑣
= 3,33
𝑖𝑚𝑝
𝑠𝑒𝑐
= 3,33
𝑀𝐻𝑧
.
Let's assume that we connect the drive to CSMIO/IP-M motion controller which provides 125kHz
max. frequency STEP signal. We would just only get
187
𝑟𝑒𝑣
𝑚𝑖𝑛
.
!
Here now the electronic gear comes to the rescue. Thanks to it we can set a multiplier x20 and we
get
3750
𝑟𝑒𝑣
𝑚𝑖𝑛
.
. The electronic gear function is set by two parameters: X and Y.
Set motor's position is expressed by the formula:
𝑀𝑂𝑇𝑂𝑅
′
𝑆
𝑃𝑂𝑆𝐼𝑇𝐼𝑂𝑁
=
𝐼𝑁𝑃𝑈𝑇
𝑆𝐼𝐺𝑁𝐴𝐿
×
𝑋
𝑌
In our example we enter X=20, and Y=1. We are going to multiply the input signal by 20. Obviously
using this function we can divide the input signal if there is such a need. However it is usually used
for multiplying.
To keep the settings saved after power is off - on the toolbar press icon after settings change.
The input signal multiplying (as shown in the example above) has negative influence on motor's
culture of work and on positioning accuracy. According to this fact we do not recommend the
multiplying use in applications which require great motion smoothness and precision.
In such situations we need to use CNC controller that is able to provide STEP signal with enough
frequency – e.g. CSMIO/IP-S which generates 4MHz max frequency STEP signal.
Parameter name
Description
Invert dir
Change of motor revs direction. The parameter affects only
external STEP/DIR signal control.
32
simDrive™ - AC Servo Drive User Guide
Содержание SimDrive M4-H040K
Страница 1: ...Applies to hardware version v1 Applies to firmware version v2 00 Rev 1 0 copyright 2014 CS Lab s c...
Страница 9: ...2 1 Brushless motors AC BLDC simDrive AC Servo Drive USER GUIDE 9...
Страница 10: ...2 2 Brushed motors DC 10 simDrive AC Servo Drive User Guide...
Страница 17: ...4 1 4 Digital inputs IN0 IN5 4 1 5 Digital outputs OUT0 OUT2 simDrive AC Servo Drive USER GUIDE 17...