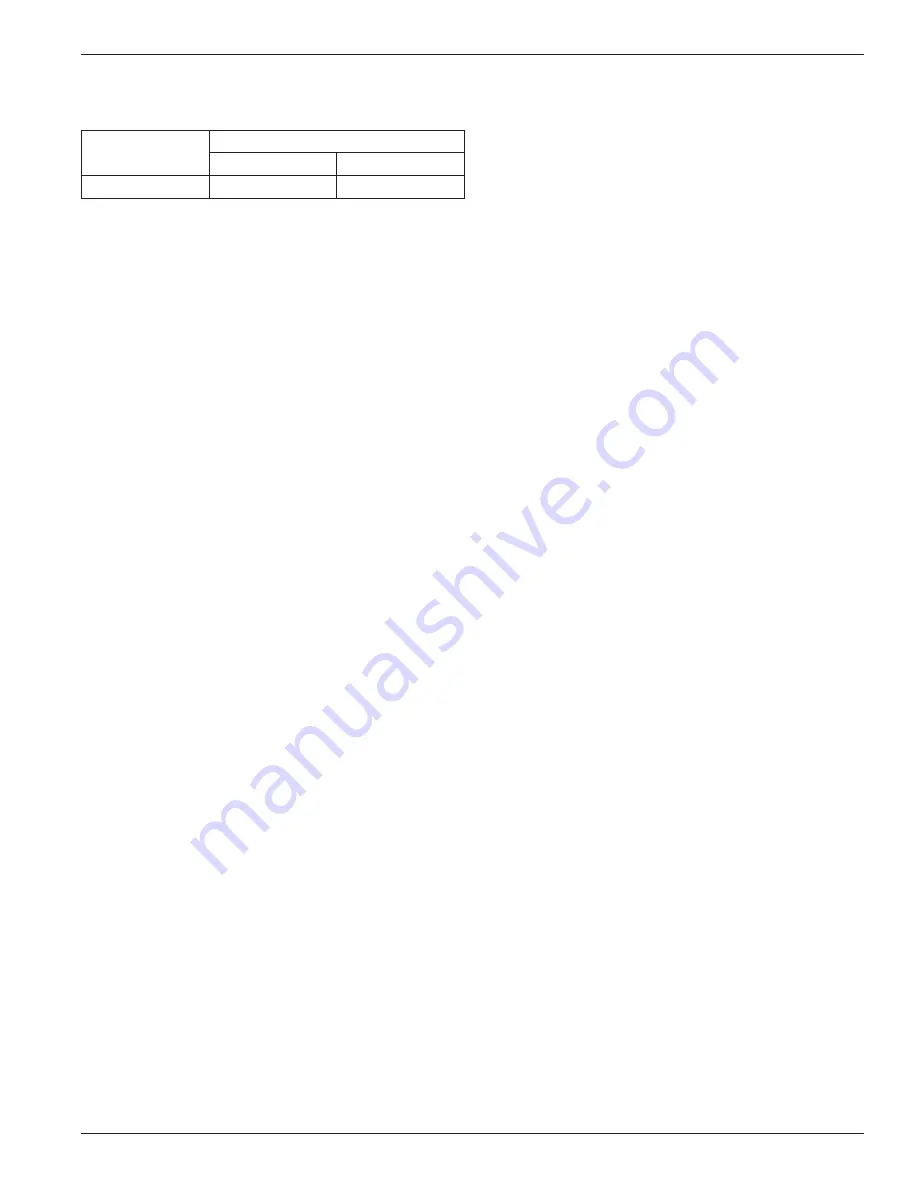
challenging for a Corken compressor user to select a
suitable crankcase oil. This guide is intended to aid in
that regard.
Compressor
Model
Approximate Capacity
Quarts
Liters
HG/THG600
7
6.6
Figure 2.6B
It is safe to say that purchasing a quality crankcase oil,
and changing it regularly, is significantly less costly than
the repair bill and downtime associated with a lubrication
failure in any gas compressor. Considering the relatively
small volume of oil used in Corken compressors, and the
critical nature of the services where these compressors
are used, selecting the appropriate high quality oil is
the most economical choice. It will help ensure the
dependability and longevity of the compressor.
Corken recommends using industrial oils (rather than
engine oil or “motor oil”). Industrial oils have additives
selected and blended for specific purposes. Many are
designed specifically for the challenges inherent in
compressor crankcases. Industrial oils are available as
a conventional (mineral based) oil, a synthetic oil, or a
blend of the two.
All new Corken compressors are tested at the factory
using a conventional mineral oil. This oil is drained
prior to shipment. An oil suitable for the anticipated
environmental and operating conditions must be
selected and added to the compressor prior to the
initial startup.
Oils to Avoid
Selecting a crankcase oil based on low price or easy
availability is seldom the best decision. Following are oils
to avoid:
•
Do not use
any oil with a viscosity index below 95.
•
Do not use
any oil with a pour point less than 20°F
(11°C) lower than the anticipated minimum ambient
temperature (unless a crankcase oil heater is used).
•
Do not use
engine/motor oil.
See below for additional detail on each of these parameters.
Critical Oil Characteristics
Viscosity
Viscosity is the most important physical property of
lubricating oil. Simply put, the viscosity of an oil is a
measure of its resistance to flow. In gas compressors,
oils with higher viscosity (like ISO 100) are thicker and
are used for higher ambient temperatures. Oils with lower
viscosity (like ISO 68) are thinner and are used at lower
ambient temperatures. If the oil’s viscosity is too high, the
oil may not circulate through the compressor adequately.
If the viscosity is too low, the lubricating film will be
unable to protect the components from wear.
Viscosity Index
Viscosity Index (VI) is a measure of how much the
oil’s viscosity changes as its temperature changes. A
low viscosity index is an indication that the viscosity
changes more as the temperature changes. Oils with low
viscosity index tend to become thin as the oil temperature
increases. This can cause lubrication failure as well as
unstable oil pressure. A high viscosity index reflects
a more stable viscosity, and is generally preferred for
Corken compressors.
The minimum Viscosity Index for
oils used in Corken compressors is 95
(VI is a unit-less
number). This is particularly important when operating
at high or low temperature extremes, or at a variety of
ambient temperatures (seasonal changes). Oils with a high
viscosity index can be used at wider ambient temperature
range compared to oils with a lower viscosity index.
It should be noted that a conventional oil (not synthetic)
with a high viscosity index may not necessarily be
suitable for continuous service at high temperature.
Such an oil will oxidize faster than a synthetic oil.
Synthetics have naturally high viscosity index, and are
therefore recommended for “heavy service” as described
below—including high temperature and continuous duty
applications. It many climates, the use of the correct
synthetic oil will eliminate the need to change oil viscosity
grades as the seasons change.
Pour Point
The pour point of an oil is the lowest temperature at
which the oil flows. At temperatures below the pour
point, the oil is essentially solid and can’t freely flow to
the compressor’s bearings and other wear surfaces, or
even to the compressor’s oil pump.
The oil’s pour point is particularly critical when starting
a compressor at low temperature conditions. An oil
should have a pour point at least 20°F (11°C) below the
lowest expected ambient temperature. For example,
if the minimum ambient temperature is expected to
be 0°F (-18°C), the pour point must be no higher than
-20°F (-29°C).
Do not assume the pour point of an oil is low enough.
Consult the oil’s technical data sheet – generally available
on the oil manufacturer’s website. Many conventional oils
have a pour point around 0 to 15°F (-18 to -9°C) which is
too high to use at low ambient temperatures. Synthetic oils
generally have a lower pour point than conventional oils.
Crankcase Oil Recommendations
The primary factors for selecting a suitable crankcase oil
from the chart below are ambient temperature range and the
9