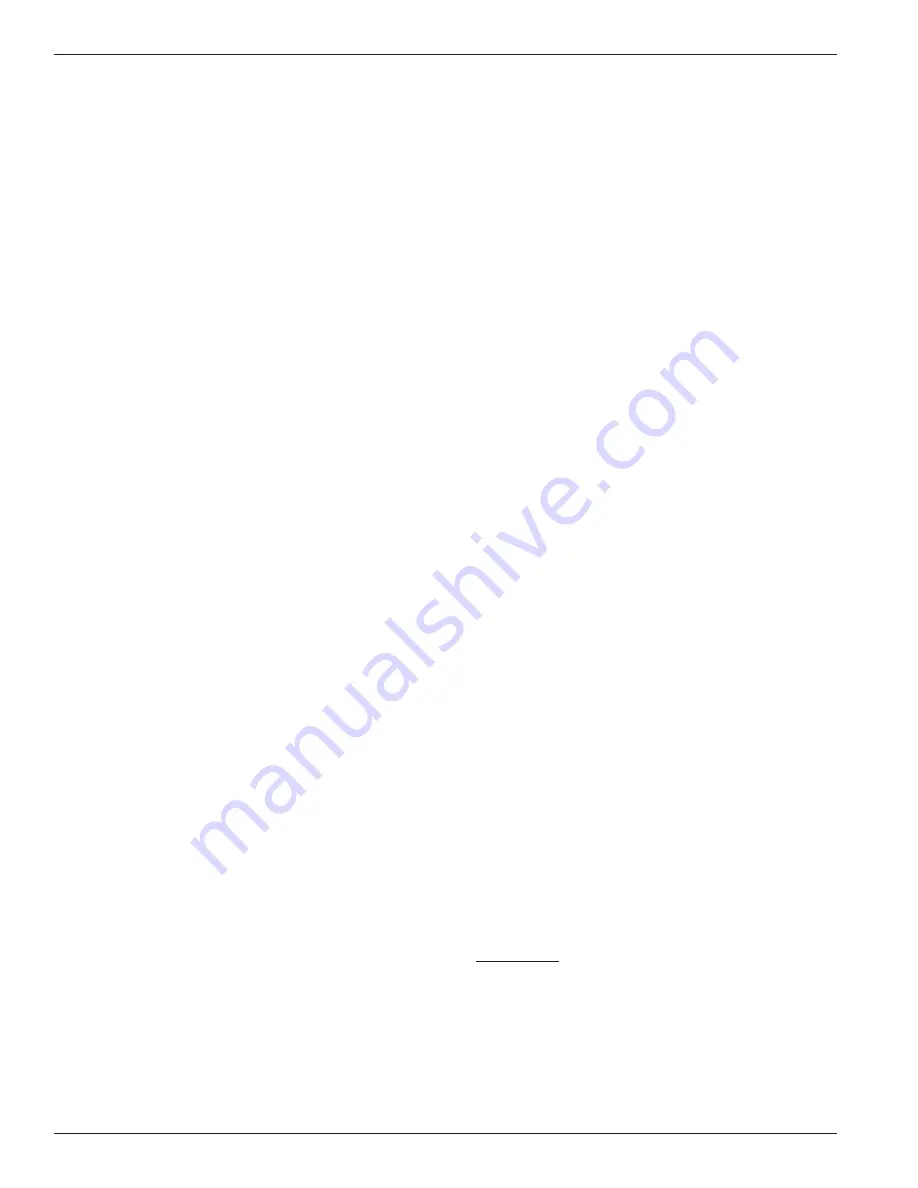
3 .7 Variable Clearance Heads (VCH)
Variable clearance head (VCH) assemblies (outboard)
allow adjustment of the compressor when operating
conditions change. Turning the clearance volume adjusting
cup changes the capacity and bhp requirements of the
cylinder. Normally, the packager has already provided
at least a preliminary adjustment of the VCH. If not, it
may be necessary to adjust the heads for maximum
clearance before startup. After startup, adjust the heads
inward to increase the capacity and bhp of the cylinder
to the desired levels.
To adjust the variable clearance heads, follow the steps
below.
1) Remove the VCH adjusting screw nut. Adjustment can
be made while the unit running.
2) Turn the end of the adjusting cup to adjust the cylinder
head end clearance.
3) Turning the end of the adjusting cup inward (clockwise)
reduces cylinder head end clearance.
4) Turning the end of the adjusting cup outward
(counterclockwise) increases cylinder head end
clearance.
5) Replace the VCH adjustable screw nut and O-ring.
The approximate clearance volume change per turn of
the adjusting bolt is 3%.
3 .8 Startup Check List
Please verify all of the items on this list before
starting the compressor! Failure to do so may result
in a costly (or dangerous) mistake .
Before Starting the Compressor
1. Become familiar with the function of all piping
associated with the compressor. Know each line’s use!
2. Verify that actual operating conditions will match the
anticipated conditions.
3. Ensure that line pressures are within cylinder
pressure ratings.
4. Clean out all piping.
5. Check all mounting shims, cylinder and piping
supports to ensure that no undue twisting forces exist
on the compressor.
6. Verify that strainer elements are in place and clean.
7. Verify that cylinder bore and valve areas are clean.
8. Check V-belt tension and alignment. Check drive
alignment on direct drive units.
9. Rotate unit by hand. Check flywheel for wobble or play.
10. Check crankcase oil level.
11. Drain all liquid traps, separators, etc.
12. Verify proper electrical supply to motor and panel.
13. Check that all gauges are at zero level reading.
14. Test piping system for leaks.
15. Purge unit of air before pressurizing with gas.
16. Carefully check for any loose connections or bolts.
17. Remove all stray objects (rags, tools, etc.) from
vicinity of unit.
18. Verify that all valves are open or closed as required.
19. Double-check all of the above.
After Starting Compressor
1. Verify and note proper oil pressure. Shut down and
correct any problem immediately.
2. Observe noise and vibration levels. Correct
immediately if excessive.
3. Verify proper compressor speed.
4. Examine entire system for gas, oil or water levels.
5. Note rotation direction.
6. Check startup voltage drop, running amperage and
voltage at motor junction box (not at the starter).
7. Test each shutdown device and record set points.
8. Test all relief valves.
9. Check and record all temperatures, pressures and
volumes after 30 minutes and one hour.
10. After one hour running time, tighten all head bolts,
valve holddown bolts, and baseplate bolts. See
Appendix B for torque values.
16