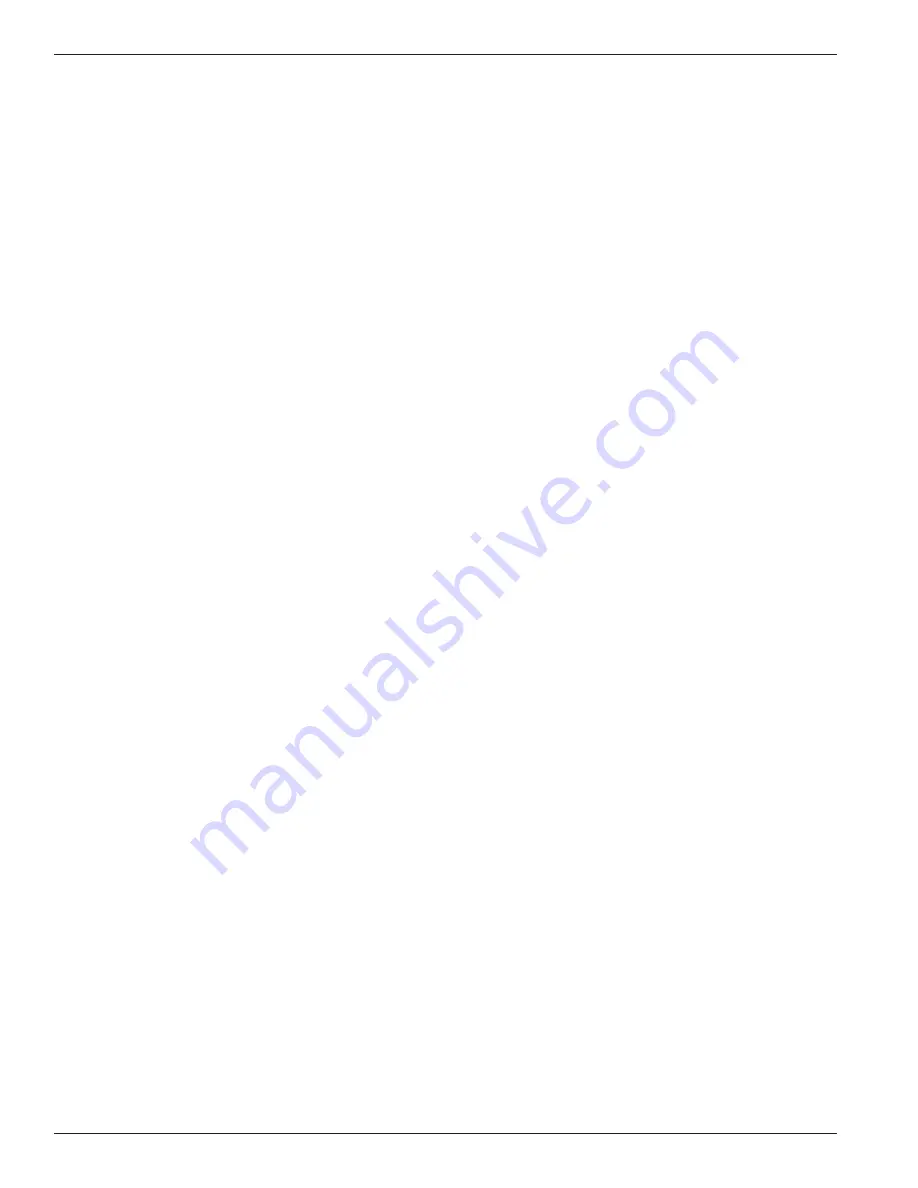
gas. These oils typically also have properties that prevent
corrosion and carbon buildup in the cylinders and valves.
Contact Corken is assistance is needed in selecting a
suitable cylinder lubricating oil. Oil manufacturers are
often a good source for this information as well.
Engine oils (motor oils) should never be used as a cylinder
lubricant. The additives in engine oil are poorly suited for
that purpose.
Engine Oils (Motor Oils)
At noted above, engine oils (or motor oils) are
not recommended for use in Corken compressor
crankcases or cylinders. Engine oils are formulated
for use in internal combustion engines and contain
additives that specifically counter the contaminants
created by the combustion of fuel (soot, CO
2
, water,
etc.). As such, they are not necessarily the best oils to
use in a gas compressor.
Detergents and dispersants in engine oils can react
with the compressor’s process gas, or form emulsions
inside the compressor’s crankcase that are detrimental
to lubrication. Ultimately, this negatively effects the
oil’s properties and damages the compressor’s critical
internal components.
If a suitable industrial oil is not readily available, engine oils
can
temporarily
be used in Corken compressors in normal
service, but only until a suitable industrial oil can be sourced
(see above for definition of “normal service”). Engine oils
should not be used for compressors in “heavy service”.
Engine oil is labeled with an API “donut” indicating the
API Service Grade. It is
critical
that the engine oil have
an API Service Grade of
SJ or better
. Engine oils with
an API Service Grade of SA and SB are obsolete, but still
readily available. These very low quality oils should
never
be used in Corken compressors. Industrial oils do not
receive an API Service Grade like engine oil does.
2 .7 Relief Valves
A relief valve should be fitted in the piping between
the compressor discharge any device that blocks or
restricts the gas flow. Relief valves should be properly
sized and made of a material compatible with the gas
being compressed and temperatures generated by the
compressor. Local codes and regulations should be
checked for specific relief valve requirements. Also, relief
valves may be required at other points in the compressor’s
system piping like to protect ASME code vessels.
A rule of thumb to select the set pressure on a relief valve
located on compressor piping discharge is for it to be
between 10–20% above the highest discharge pressure
the compressor can produce, but less than the maximum
compressor working pressure. This can vary with relief
valve manufacturer so consult the valve supplier.
2 .8 Shutdown/Alarm Devices
For all applications, shutdown/alarm sensors (switches
or transmitters) provide worthwhile protection that may
prevent serious damage to the compressor system. All
electronic devices should be selected to meet local code
requirements. Shutdown/alarm devices typically used on
Corken compressors are as follows:
1.
Low Oil Pressure Sensor:
Shuts down the unit if
crankcase oil pressure falls below 15 psig (1.03 bar g)
due to oil pump failure or low oil level in crankcase.
The switch or the compressor controller must have
a 30 second delay on startup which allows the
compressor to build oil pressure in the crankcase.
2.
High Discharge Temperature Sensor:
This sensor is
strongly recommended for all applications. Both sensor
and the compressor have an operating range. It is
preferable that the sensor set point be 30°F (17°C) above
the normal compressor discharge temperature, but below
the maximum design temperature for O-ring material
used on the compressor (see note below). The O-ring
code can be found on the compressor model number.
Note: Maximum temperature for these material are:
• Buna-N and Neoprene
®1
250°F (121°C)
• Viton
®1
and PTFE 350°F (177°C)
1
Registered trademark of the DuPont Company.
3.
Low Suction Pressure Sensor:
Shuts down the unit
if inlet pressure is below a preset limit (set point). The
set point should follow these guidelines:
• For safety shut off it must be greater than
the compressor minimum suction pressure
(atmospheric) to prevent pulling oil from the
crankcase into the gas stream.
• For process shut off a good rule of thumb set point
is 25% of product vapor pressure. It can be lower
or higher based on economic decision on how
much product can be recovered. This decision
must be made by the customer.
4.
High Discharge Pressure Sensor:
Shuts down
the unit if outlet pressure is above a preset limit (set
point). The set point should follow these guidelines:
• Less than the compressor’s maximum working
pressure.
• Less than 80–90% of the relief valve pressure set
point (consult relief valve manufacturer)
• Greater than the compressor’s discharge pressure
based on normal operating conditions.
5.
Vibration Switch:
Shuts down the unit if vibration
becomes excessive.
12