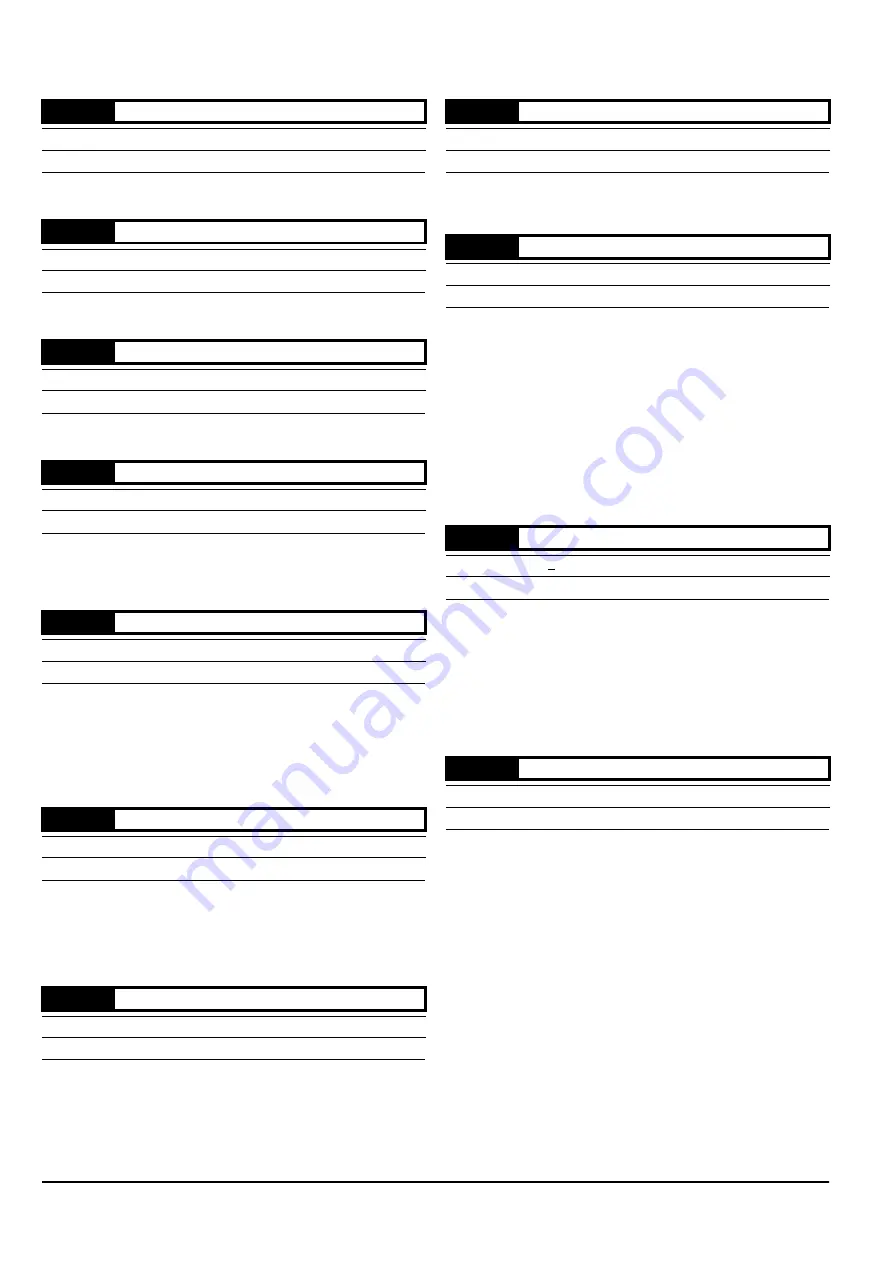
*
46
M’Ax User Guide
Issue Number: 4
See Appendix D Optimising the Dynamic Performance.
See Appendix D Optimising the Dynamic Performance.
See Appendix D Optimising the Dynamic Performance.
0.16
is used for adjusting the cut-off frequency of a first-order filter in the
current demand to the speed loop. See Appendix D Optimising the
Dynamic Performance.
Set
0.17
at
1
to copy to the related PID buffer in the SLM new values
entered in the following parameters:
0.13
,
0.14
,
0.15
Speed-loop PID gains
0.16
Current-demand filter 1 cut-off frequency
Return
0.17
to
0
immediately afterwards. Do not leave
0.17
at
1
since
this will prevent the Drive from operating correctly.
I
M
Rated continuous motor-current (defined by the motor via the
SLM
)
Use
0.18
for changing the level of overload current from the Drive. The
default overload is 200% rated continuous motor-current for up to 2
seconds.
For basic applications, do not set
0.18
at values greater than 200%.
0.19
indicates the value of the continuous-current rating of the motor.
The value is automatically defined by the motor via the
SLM
.
0.20
indicates the maximum continuous output current of the Drive. This
is also referred to as the FLC (full-load current).
Set
0.22
as follows:
0.22 set at 0 (default)
The motor speed is controlled by the speed reference selected by
0.30
Reference selector, or by jog (see
0.31
Jog selected indicator and
0.32
Jog reference).
0.22 set at 1
The motor torque is controlled by
0.23
Torque reference. The speed may
vary in order to maintain the motor torque at the level of the torque
demand.
No speed limit is applied; if the motor speed exceeds [0.08] Maximum
reference clamp, the Drive will trip, allowing the motor to coast. (See trip
OU.SPd
in Appendix B Diagnostics.)
I
LIM
Value of the current limit that is obtained from the setting of
0.18
Symmetrical current limit
Set at the required percentage of maximum continuous motor current.
The value can be entered in the following ways:
•
Use of the display and keypad
•
Via serial communications
If the torque is to be controlled by an external torque reference, see the
M’Ax Advanced User Guide.
Set
0.24
as follows for speed control (ramps are not used with torque
control):
0.24 set at 0 (default)
The motor speed responds directly to changes in the speed reference.
Excessive acceleration demand will cause current-limiting, resulting in
the motor acceleration not meeting the demand. Excessive deceleration
demand will cause excessive DC-bus voltage, resulting in the Drive
tripping (trip
OU
).
0.24 set at 1
Maximum acceleration and deceleration due to the following...
•
Starting the motor when a speed reference is already applied to the
Drive
•
Rapid changes in the speed reference
•
Stopping the motor by opening the
RUN
contact.
...are limited to the values of the following parameters:
0.25
Acceleration rate
0.26
Deceleration rate
0.13
Speed-loop proportional gain Kp1
{3.10}
ô
0.000 ~ 0.3000
ð
[
SLM
]
RW
Uni
0.14
Speed-loop integral gain Ki1
{3.11}
ô
0.000 ~ 20.000
ð
[
SLM
]
RW
Uni
0.15
Speed-loop derivative gain Kd1
{3.12}
ô
0.0000 ~ 0.1000
ð
[
SLM
]
RW
Uni
0.16
Current-demand filter 1 cut-off frequency
{4.12}
ô
0 ~ 1200
ð
500
RW
Uni
Hz
0.17
SLM online enable
{11.64}
ô
0 ~ 1
ð
0
RW
Bit
0.18
Symmetrical current limit
{4.07}
ô
0 ~ 300
ð
200
RW
Uni
%I
M
0.19
Motor - rated current
{5.07}
ô
0 ~ FLC
RO
Uni
A
0.20
Drive rated current (FLC)
{11.32}
ô
00.00 ~ 99.99
RO
Uni
P
A
0.22
Torque mode selector
{4.11}
ô
0 ~ 1
RW
Bit
P
0.23
Torque reference
{4.08}
ô
+200.00
ð
0.00
RW
Bi
%I
LIM
0.24
Ramp enable
{2.02}
ô
0 ~ 1
ð
0
RW
Bit
Содержание M'Ax 403
Страница 6: ......
Страница 61: ...M Ax User Guide 55 Issue Number 4 Use this page for notes...
Страница 73: ...M Ax User Guide 67 Issue Number 4 Use this page for notes...
Страница 75: ...M Ax User Guide 69 Issue Number 4...