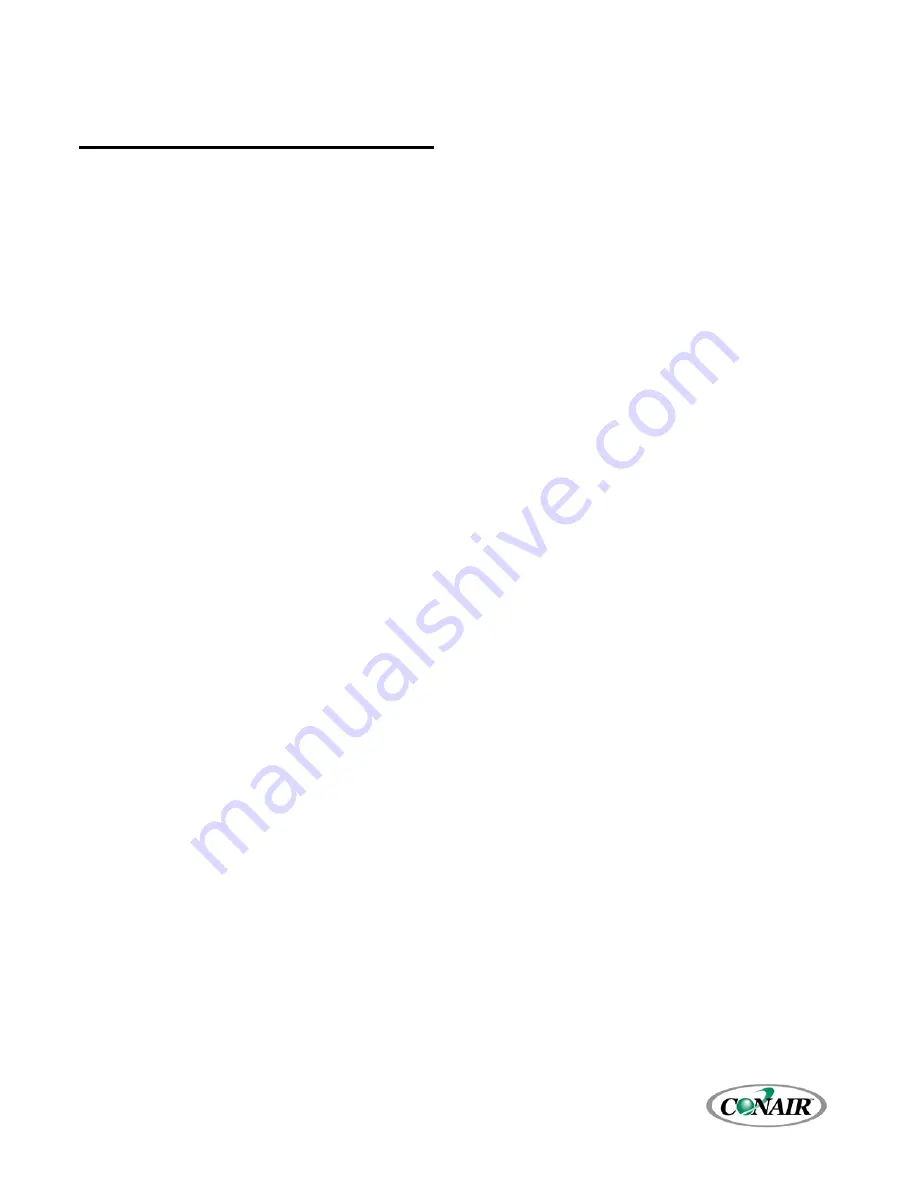
Corporate Office: 724.584.5500
Instant Access 24/7 (Parts and Service): 800.458.1960
Parts and Service
:
814.437.6861
9
Installation - Chiller
Mechanical
Unit Location
The chiller is available in many different
configurations to meet various environments. Please
refer to the proposal and order acknowledgement
for this equipment to verify the specific
environmental design conditions for your chiller.
Allow a minimum of 48 inches (1219mm) of
clearance between the remote condenser and any
walls or obstructions. For installations with multiple
condensers, allow a minimum of 96 inches (2438mm)
between condensers placed side-by-side or 48
inches (1219mm) for condensers placed end-to-end.
In all cases, install the equipment on a rigid surface
suitable to support the full operating weight of the
unit. Level all equipment to ensure proper operation.
When installed the equipment must be level within
¼ inch over its length and width.
Serviceability is an important factor to consider when
deciding on the location of the chiller. Do not
compromise this feature by locating it in an
inaccessible area. When locating the chiller it is
important to consider accessibility to the
components to allow for proper maintenance and
servicing of the unit. In general, allow a minimum of
36 inches (914mm) of clearance around all sides and
above the unit. There should be no piping or conduit
located over the unit. This will ensure easy access
with an overhead crane or lift for heavier
components should they need to be replaced or
serviced.
Proper ventilation is another important
consideration when locating the unit. Locate the unit
is an area that will not rise above 110°F (43.3°C).
In addition, ensure the condenser and evaporator
refrigerant pressure relief valves can vent in
accordance with all local and national codes.
Rigging
The chiller has a structural steel frame with forklift
slots to facilitate easy movement and positioning.
Follow proper rigging methods to prevent damage
to components. Avoid impact loading caused by
sudden jerking when lifting or lowering the chiller.
Use pads where abrasive surface contact may occur.
Use the frame supporting the unit for positioning it
with a crane or a forklift.
Chilled Water Piping
Proper insulation of chilled water piping is crucial to
prevent condensation. The formation of
condensation on chiller water piping, the state
change of the water from gas to liquid, adds a
substantial heat load to the system and becomes an
additional burden for the chiller.
The importance of properly sized piping between
the chiller and process cannot be overemphasized.
Reference the current edition of the ASHRAE
Fundamentals Handbook or other suitable design
guide for proper pipe sizing. In general, run full size
piping out to the process and then reduce the pipe
size to match the connections on the process
equipment. One of the most common causes of
unsatisfactory chiller performance is poor piping
system design. Avoid long lengths of hoses, quick
disconnect fittings, and manifolds wherever possible
as they offer high resistance to water flow. When
manifolds are required, install them as close to the
use point as possible. Provide flow-balancing valves
at each machine to assure adequate water
distribution in the entire system.
Condenser Water Piping
(Water-Cooled Condenser Chillers Only)
The performance of a condenser is dependent on
maintaining the proper flow and temperature of
water through the heat exchanger. Insufficient water
flow or high condenser water supply temperature
will result in the reduction of cooling capacity of the
chiller. Extreme conditions will eventually result in
the chiller shutting down due to high refrigerant
pressure. Allowing the condenser to plug up from
contaminants in the condenser water stream
adversely affects performance. In order to reduce
maintenance costs and chiller downtime, a water
treatment program is highly recommended for the
condenser cooling water. Contact our Customer
Service Department for assistance in the proper
procedure for cleaning out any plugged condenser.