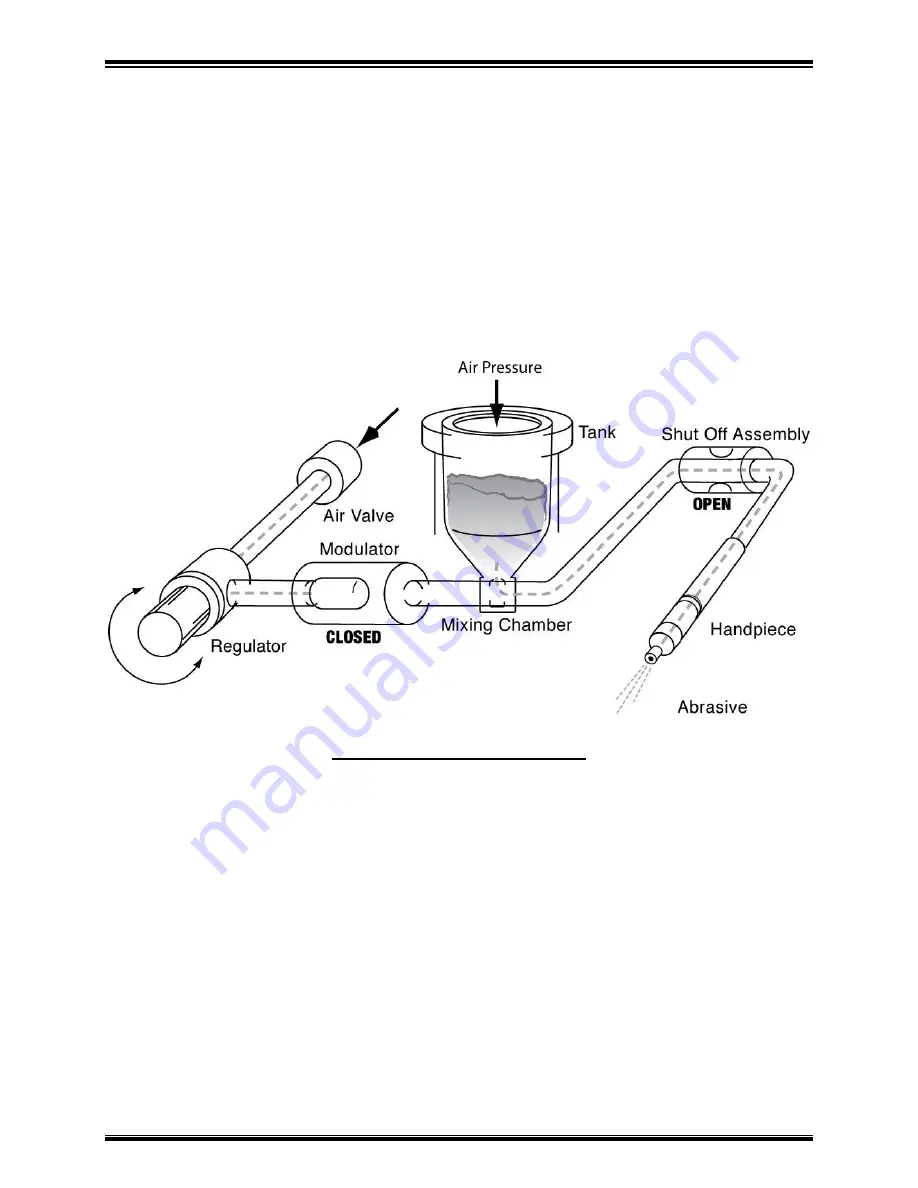
DirectFlo DF1400
Chapter 1: The DirectFlo 1400
Comco Inc.
1
-
5
Issue Date: January 2009
How the DirectFlo DF1400 Works
(cont’d)
In the second half of the operating cycle, the modulator coil becomes energized. This
pulls the modulator core against the seat (see Figure 1-4, below), shutting off the airflow
from the regulator. The pressure in the mixing chamber now decreases because the
downstream end of the system, at the nozzle, is open to the atmosphere.
Since the pressure in the mixing chamber is lower than the pressure in the abrasive
tank, the two pressures try to balance. Air pressure inside the abrasive tank pushes a
small amount of abrasive through a precision orifice at the bottom of the tank, into the
mixing chamber and out through the nozzle.
Figure 1-4: Modulator Closed
When the next cycle begins, the modulator is again de-energized, and opens to allow
pressurized air to freely flow into the mixing chamber and out the nozzle. This forces air
back into the abrasive tank, stabilizing the pressure between the tank and the mixing
chamber (refer back to Figure 1-3).
Each cycle happens very quickly; 50-60 times per second. The end result of this
“stop/start” action of the modulator is a consistent stream of abrasive out the nozzle, as
long as the footswitch is depressed. Releasing the footswitch stops the modulator from
cycling and causes the PowderGate to close the outlet air hose.
The only way for the abrasive powder in the tank to reach the mixing chamber is via the
orifice at the bottom of the tank. By changing the size of the tank orifice, you can
change the amount of abrasive that enters the mixing chamber, and thus change the
abrasion or cutting rate at the nozzle. Additional information regarding the tank orifice,
nozzle sizes, abrasives, and other variables in the abrasive blast process is presented in
Chapter 3 of this manual.