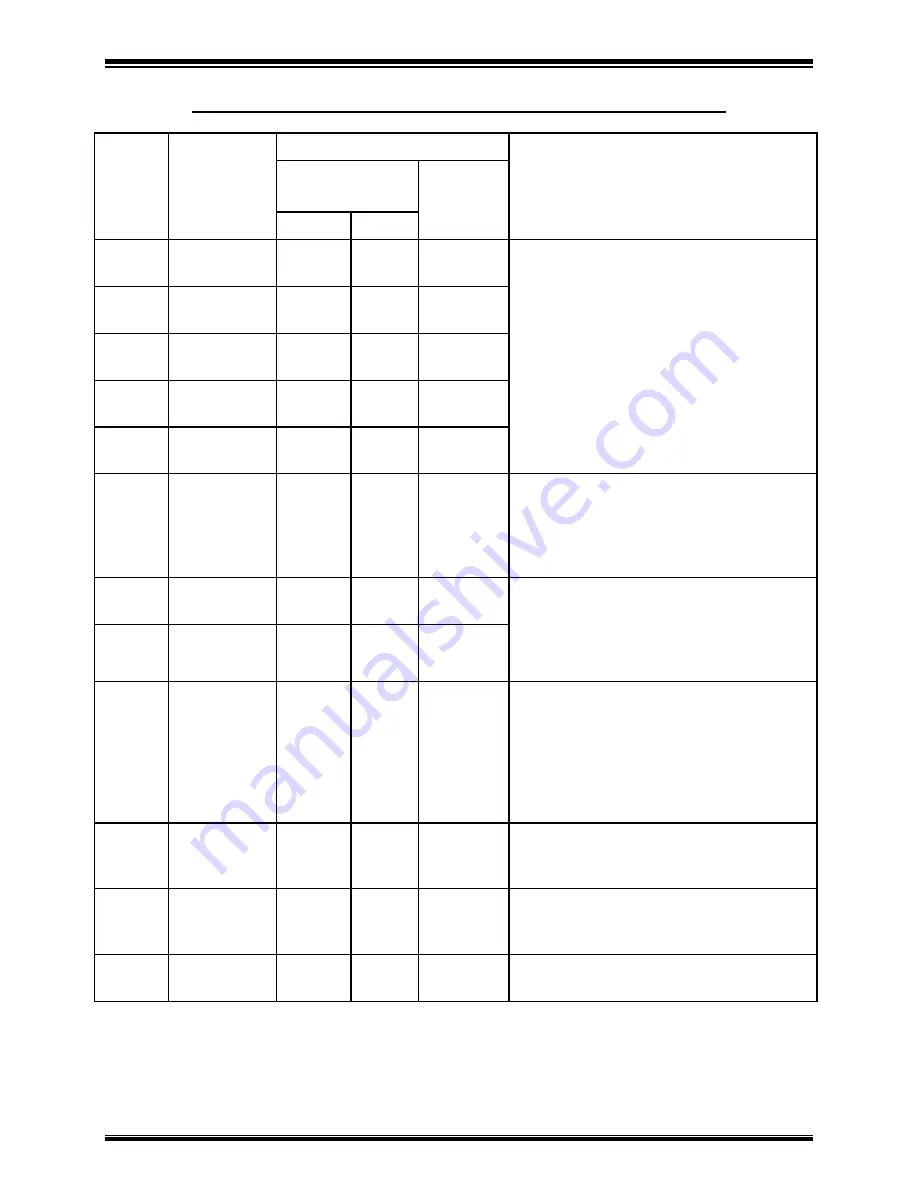
DirectFlo DF1400
Chapter 3: Using the DirectFlo
Comco Inc.
3-5
Issue Date: January 2009
Table 3-2: Common Abrasives and Their Applications
Comco
Type
Abrasive
Material
Particle Size
Description/Characteristics
Average
Particle Size
Range
(Microns)
Micron
Inch
A
Aluminum
Oxide
10
0.0004
5 - 25
The most common abrasive used. A
very hard abrasive that cuts well
through almost any material,
particularly brittle ones. Normally
leaves a matte finish, with the surface
roughness being dependent upon the
abrasive size and the blast pressure.
Somewhat sensitive to moisture.
J
Aluminum
Oxide
17.5
0.0007
10-25
B
Aluminum
Oxide
25
0.001
15 - 35
C
Aluminum
Oxide
50
0.002
30 - 80
N
Aluminum
Oxide
150
0.006
75 - 200
D
Glass
Beads
50
0.002
40 - 80
Good for light deburring and satin
finishing of some metals but not good
for cutting. Can be used to remove
loose surface particles such as oxides.
Sensitive to moisture.
E
Silicon
Carbide
20
0.0008
10 - 40
The fastest cutting of the standard
abrasives. The best abrasive to deburr
stainless steel and titanium parts. Does
not absorb moisture. Dark gray or
black in color.
F
Silicon
Carbide
50
0.002
30 - 80
G
Sodium
Bicarbonate
50
0.002
20 - 150
A very gentle abrasive, good for very
light cutting of soft materials. Can be
used to remove conformal coating from
PCBs. Water soluble and easily
removed from delicate parts.
Susceptible to moisture and cannot be
heated to above +150ºF.
H
Walnut
Shell
250
0.010
80 - 300
Gentle abrasive that can clean metal or
ceramic surfaces without changing the
surface finish. Absorbs moisture easily.
M
Plastic
200
0.008
150 - 300 Good for stripping soft materials, such
as paint or conformal coating, from
harder substrates.
K
Crushed
Glass
80
0.003
40 - 90
For light cutting of soft to medium
materials.
NOTE:
Always start the work shift with fresh abrasive powder. Powder left sitting in an
unpressurized machine overnight can absorb moisture. This contaminated
powder can cause flow problems. Keep powder containers sealed and stored
in a cool, dry place.