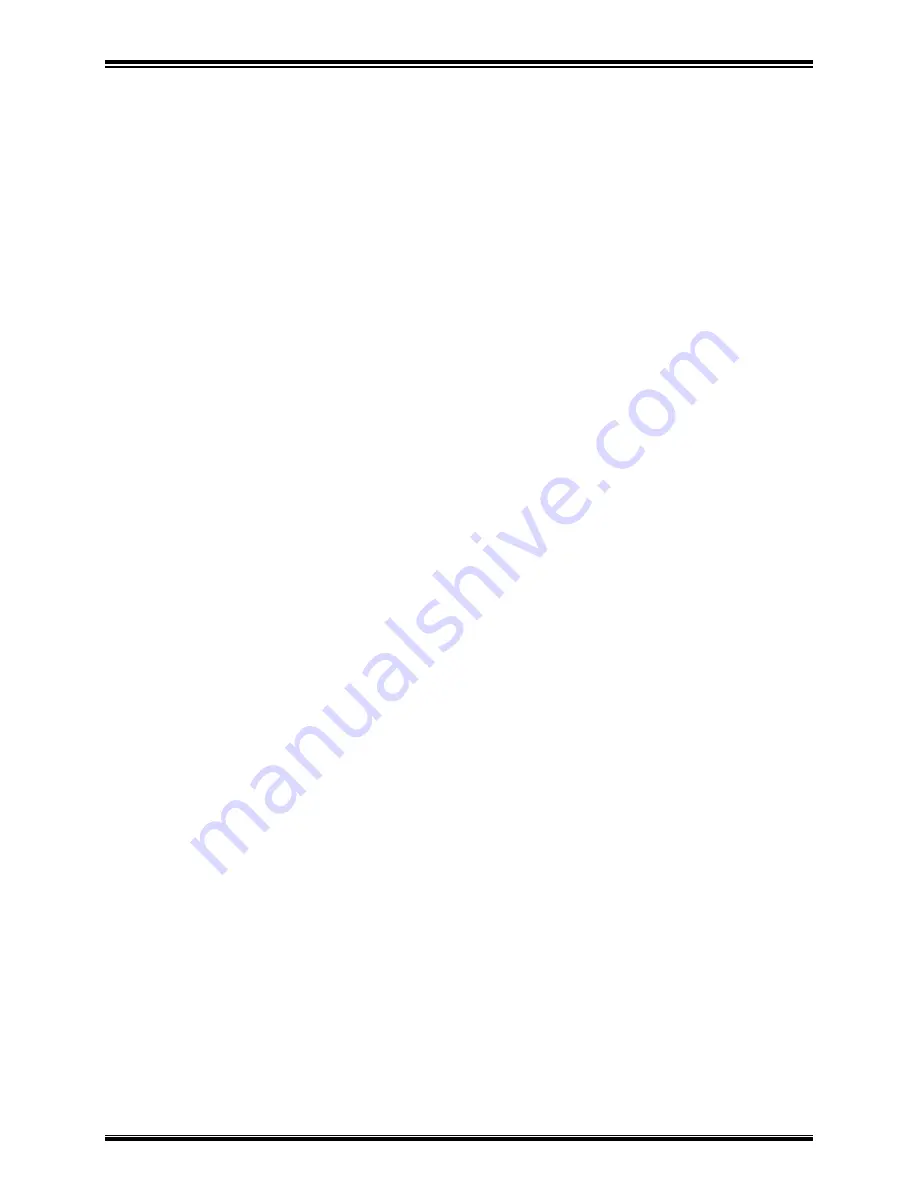
Comco Inc.
ii
Issue Date: January 2009
Table of Contents
The Comco Warranty ............................................................................................ iv
Safety Precautions ................................................................................................ v
Chapter 1: The DirectFlo DF1400
.............................................................1-1
This chapter introduces you to the basic unit, including its
description, principles of operation, and detail specifications.
Overview .................................................................................................... 1-2
Figure 1-1, DirectFlo DF1400 ......................................................... 1-2
How The DirectFlo Works .......................................................................... 1-3
Figure 1-2, DirectFlo Pressurized ................................................... 1-3
Figure 1-3, Modulator Open............................................................ 1-4
Figure 1-4, Modulator Closed ......................................................... 1-5
Detail Specifications ................................................................................... 1-6
Chapter 2: Getting Started
........................................................................2-1
This chapter tells you what you need to have and what you
need to do to set up the DirectFlo.
The Proper Work Area ............................................................................... 2-2
Figure 2-1, Micro-abrasive Blasting System Requirements ............ 2-3
Figure 2-2, DirectFlo Reference Sheet ........................................... 2-4
What You Received with the DirectFlo ....................................................... 2-5
Basic Components of the DirectFlo ............................................................ 2-6
Figure 2-3, External Component Locations ..................................... 2-7
Setup and Test .......................................................................................... 2-8
Figure 2-4, Tank Inspection ............................................................ 2-9
Chapter 3: Using the DirectFlo
.................................................................3-1
This chapter discusses the selection of key operating
parameters such as abrasives and nozzles; and tells you
how to operate the DirectFlo for maximum efficiency.
Essence of Micro-Abrasive Blasting ........................................................... 3-2
Table 3-1, Factors Affecting Abrasive Blasting ............................... 3-3
Abrasive Selection ..................................................................................... 3-4
Table 3-2, Abrasives and Their Applications ................................... 3-5
Tank Orifice and Nozzle Selection ............................................................. 3-6
Table 3-3, Orifice Selection Chart ................................................... 3-7
Figure 3-1, Changing the Tank Orifice ............................................ 3-7
Figure 3-2, Changing the Nozzle .................................................... 3-8
Table 3-4, Nozzle Chart .................................................................. 3-9
General Operation of the DirectFlo ............................................................ 3-12
Figure 3-3, Filling the Abrasive Tank .............................................. 3-13
Figure 3-4, Controls and Indicators ................................................. 3-14