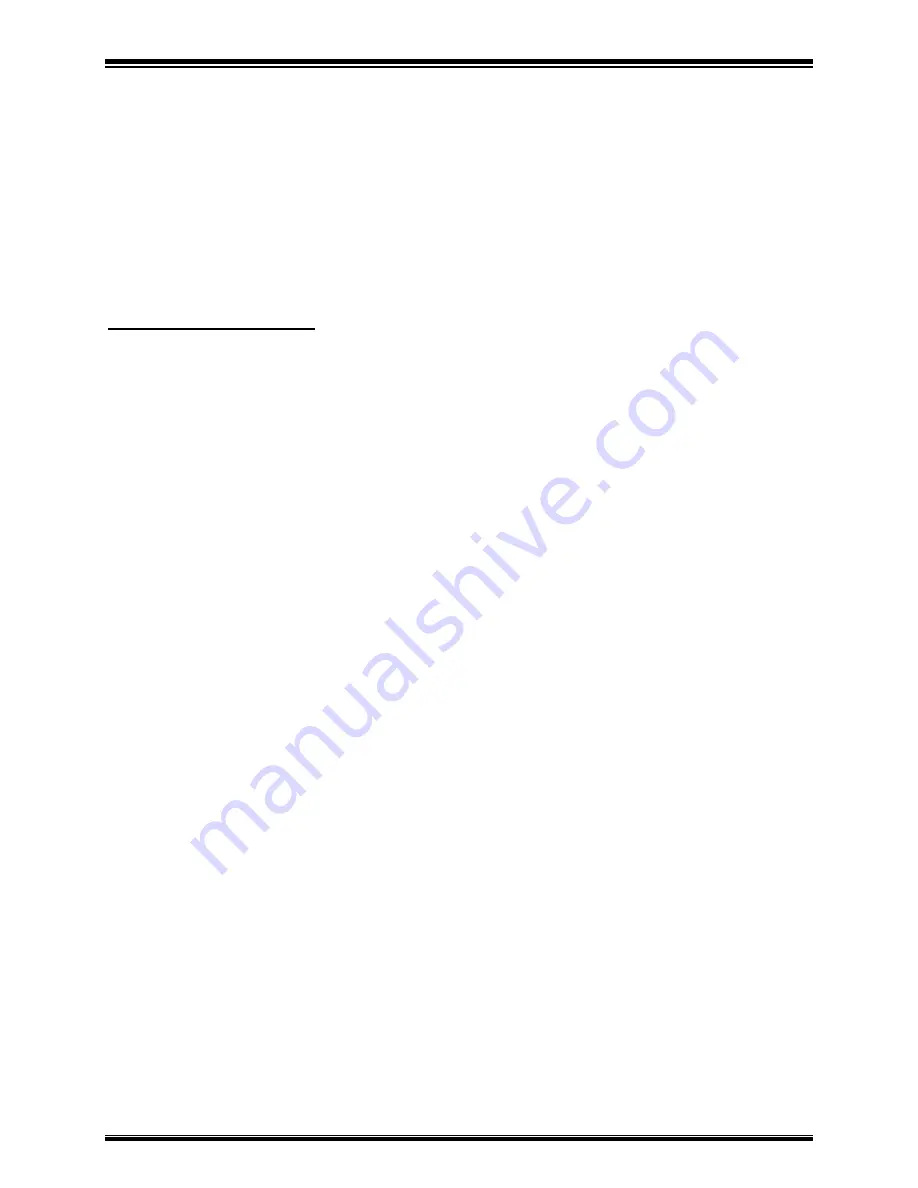
DirectFlo DF1400
Chapter 3: Using the DirectFlo
Comco Inc.
3-10
Issue Date: January 2009
Nozzle Distance
The velocity at which the abrasive particles are expelled from the nozzle produces a
well-defined stream that only flares about 7 - 10 degrees. Therefore, the distance the
nozzle is held from the work surface will determine the size of the blast pattern as well
as the material removal rate (or cutting action). Generally, as the nozzle is moved closer
to the work, the blast pattern decreases and the material removal rate increases. What
this means is, the distance the nozzle is held from the work surface will determine
whether you get a deep, narrow cut with well defined edges, or just a light abrasion over
a large area.
Abrading vs. Cutting
The width of the cut or hole produced by a round nozzle will be approximately the same
diameter as the nozzle, if the distance is less than 5 times the diameter of the nozzle
opening. Likewise, the cut width will increase to 3 times the nozzle diameter at a
distance of 25 times the opening and to 5 times at a distance of 40 times the opening.
Increasing the distance of the nozzle, the walls of a cut or hole will become increasingly
tapered and the top edge will be more rounded. At very long distances (over several
inches) there will be very little cut definition, but rather a general "blasting" of the
surface. Most cleaning and peening operations are done in this manner.
Although cutting action increases as the nozzle is moved closer to the work surface, it
should be noted that the material removal rate reaches a maximum when the spacing
between the nozzle tip and the work is about 5-8 times the nozzle opening diameter.
Moving the nozzle closer than this tends to start slowing the cutting rate as particles
bounce back and collide with each other. Also, as the hole becomes deeper, the
diameter will increase due to abrasive working on the sides of the cut. Deep holes or
cuts with relatively straight sides may be obtained if the cut is interrupted frequently and
excess abrasive removed.
These rules change somewhat for rectangular nozzles since the abrasive flow is more of
a fan and the cut character is more a function of the smaller dimension of the rectangle
than the greater width. Rectangular nozzles offer the advantage of a very narrow cut
without the disadvantage of very slow cutting.
Angle of Approach
Typically, a nozzle held perpendicular to the work surface is only done for precision
drilling applications. In most cases, it is far easier to obtain the desired results from
abrasive blasting with a nozzle held at an angle. The resulting blast pattern when the
nozzle is at an angle to the work surface does not tend to dig holes or produce sharp
edge cuts.
As the nozzle is tipped at an angle to a surface, the cutting of a groove will improve,
since the action is self-cleaning. In this manner, a saw cut may be made with relatively
straight sides through relatively thick materials. In any case, nozzle angle can be
adjusted in two planes to result in at least one side being cut perpendicular to the
surface.