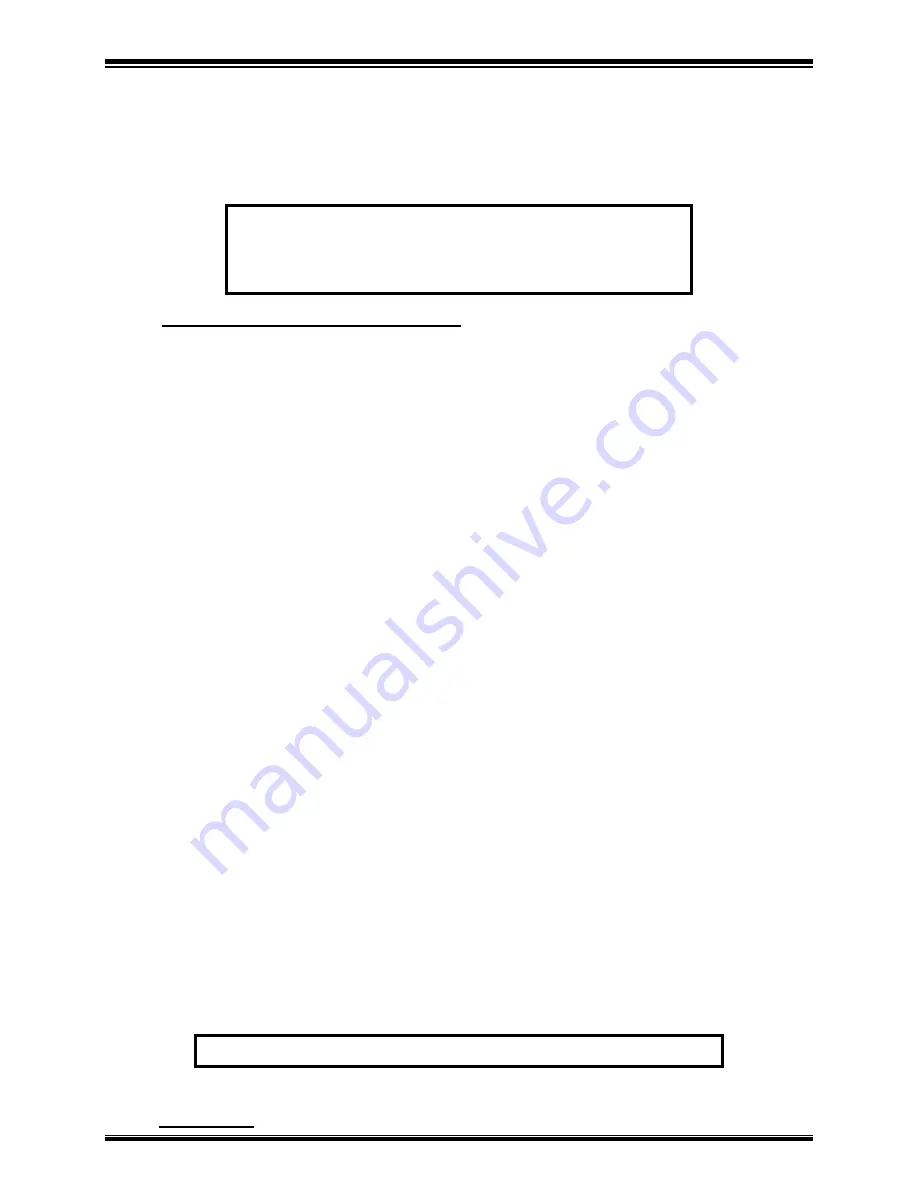
DirectFlo DF1400
Chapter 5: Trouble-Shooting and Repair
Comco Inc.
5-10
Issue Date: January 2009
The Vent Hose (1/4” Diameter)
Moving the hose through the pinch on a regular basis will greatly extend the life of the
hose. However, the vent hose will eventually wear out and need to be replaced. This
procedure explains how to replace the vent hose.
Vent Hose Replacement Procedure
1.
Turn the power off, depressurize the unit, and unplug the power cord.
2.
At the rear panel of the DirectFlo, loosen the hose connector nut from the
connector using a 7/16" open-end wrench and remove the hose.
3.
Remove and save the rubber grommet from the old hose.
4.
Pull the hose through the pinch tube and inspect the pinch tube and
plunger as described 5.13.3.
5.
Inspect the hose connector for wear, replace if necessary.
6.
Feed a 6 ft. length of new hose MB1233 (or the old cut back hose)
through the pinch tube. Slip the rubber grommet (ST5010) and the
connector nut onto the hose.
7.
Work the end of the hose onto the hose connector fitting and tighten the
nut onto the connector using a 7/16" open-end wrench. It is only
necessary to tighten the nut enough to clamp the hose to the fitting’s
tube.
Leaks
Small leaks can increase air usage considerably and reduce the efficiency of the
DirectFlo. A large drop in pressure while the machine is operating can be an indication
of an air leak. Check the supply air inlet hose and the supply regulator for leaks. This is
a high-pressure line so small leaks can cause the loss of large volumes of air.
If a leak is suspected within the DirectFlo, switch off the power and remove the cabinet
cover according to the directions in the following section. Are there any noticeable
powder clouds or unusual powder buildup inside the machine? This is an indication or a
leak in the abrasive or vent lines. Check for loose hose connections.
If necessary, switch the power on to re-pressurize the unit. Are there any noticeable or
audible leaks? Listen near the tank top, PowderGate, tank vent hose and pressure
regulator; or apply a soap solution to these locations and watch for bubbles.
It is very hard to detect a slight leak in the tank cover. If you cannot locate a leak
anywhere else, it is probably the tank cover O-rings. See the previous discussion,
“
Tank Cover
”.
CAUTION
:
Always use the proper hose when replacing a worn or
damaged abrasive hose. The use of a different hose or a
hose with a different pressure rating may present a hazard.
CAUTION
: T
here is High Voltage at the Terminal Block!!