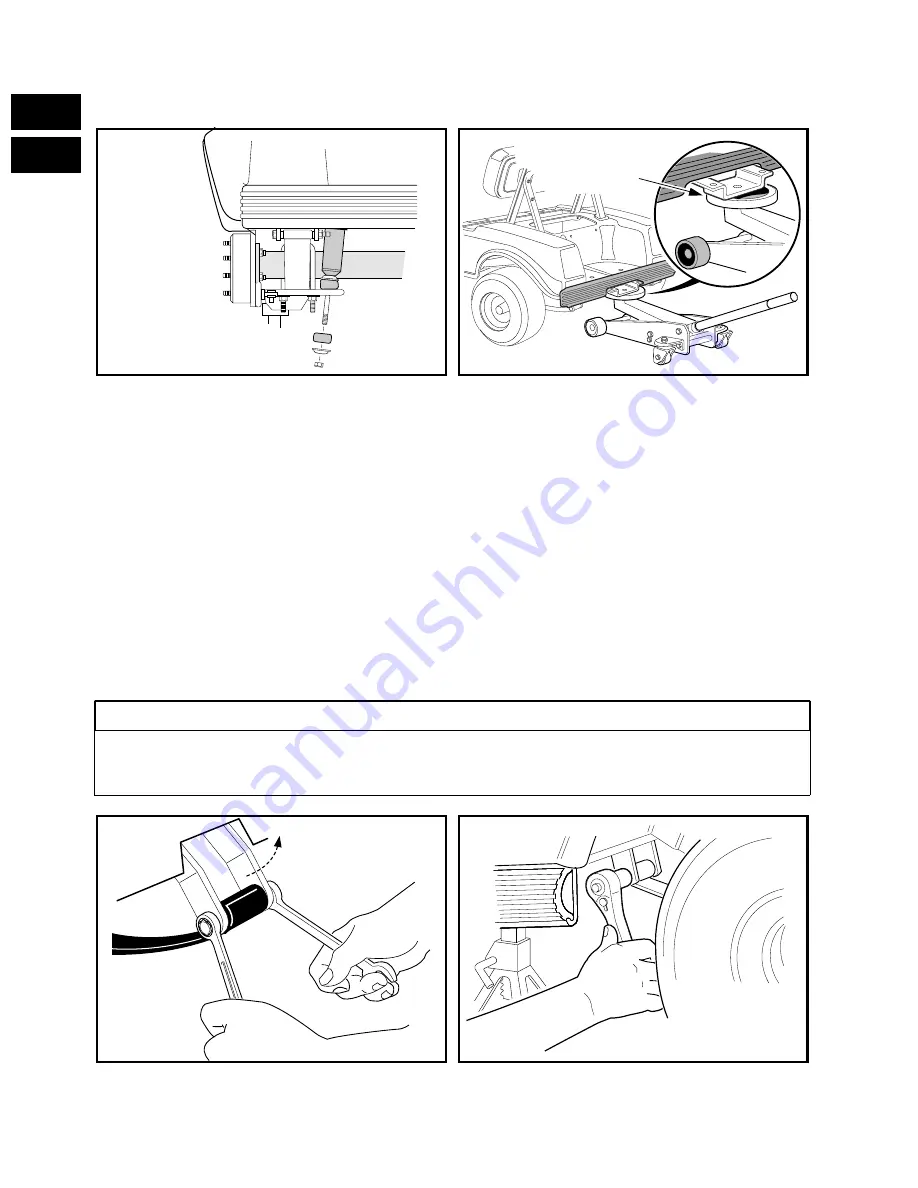
Page 44
10
G
Removing the Transaxle, Continued:
8. Continue raising the vehicle until the rear bumper is higher than the top of the unitized transmission
(high enough to allow the transaxle and engine to be rolled under it and out of the vehicle) (Figure 10-
25).
9. Position jackstands, adjusted to support the vehicle at this height, under the frame cross-member
between the leaf-spring mounts and side stringers, just forward of each rear wheel. Lower the floorjack
to allow the jackstands to support the vehicle (Figure 10-26).
10. Pull the floorjack from beneath the vehicle and move it away.
11. Lift the snubber out of the snubber bracket in the vehicle frame and lower it to the floor (Figure 10-27).
Now the powertrain should be completely disconnected from the vehicle and resting on the floor.
12. Grasp the ends of the leaf-springs at the rear of the vehicle and roll the powertrain out from under the
vehicle (Figure 10-28).
13. Place blocks under the engine mounting plate so that they will completely support the engine and keep
it level to the floor (Figure 10-29, Page 46). See NOTE below.
FIGURE 10-21
FIGURE 10-22
• PLACE THE BLOCKS SO THAT THEY WILL SUPPORT THE ENGINE WHEN THE UNITIZED
TRANSAXLE IS DETACHED AND MOVED AWAY FROM IT IN THE FOLLOWING STEPS.
FIGURE 10-23
FIGURE 10-24
DISCONNECT SHOCK
ABSORBERS FROM
LOWER MOUNTS
POSITION FLOORJACK
UNDER BUMPER
SUPPORT
NOTE
REMOVE BOLTS, THEN
ROTATE SHACKLES
UP AND AWAY
FROM SPRING
USE A 9/16" SOCKET
TO REMOVE SPRING
RETAINER BOLTS
Содержание 1997 DS
Страница 2: ......
Страница 82: ...Page 74 10 G ...
Страница 88: ...Page 80 G 11 ...
Страница 151: ...Page 143 G 13 18 DRIVE CLUTCH DISASSEMBLY FIGURE 16 5 20 21 17 19 2 1 3 10 13 4 5 6 7 11 12 12 16 15 14 9 8 18 ...
Страница 160: ...Page 152 13 18 G ...
Страница 163: ......
Страница 164: ...Golf Cars Club Car Inc P O Box 204658 Augusta GA 30917 4658 ...