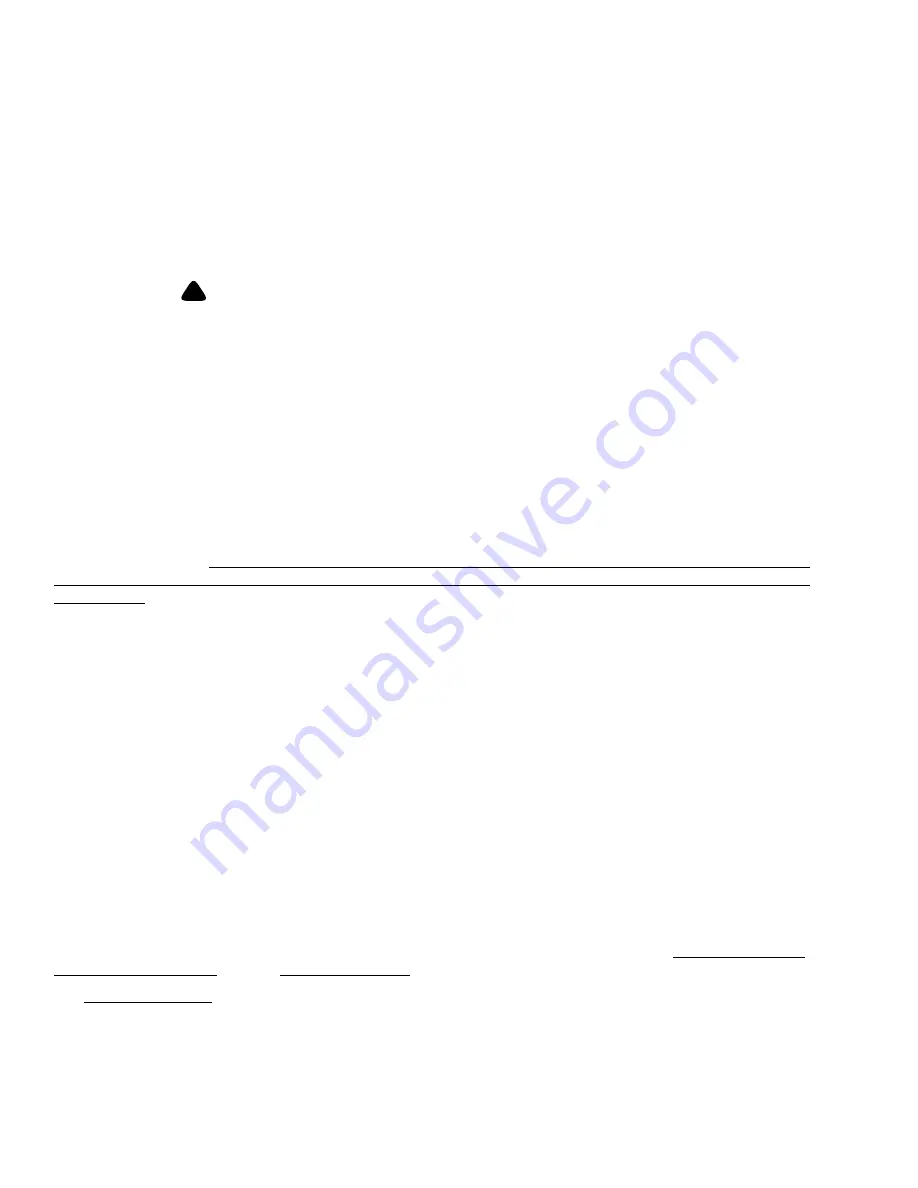
Chapter 5
Adjustment Procedures
5-2
750-177
B. LINKAGE - MODULATING MOTOR AND AIR DAMPER
The linkage consists of various arms, connecting rods, and swivel ball joints that transmit motion from the
modulating motor to the metering valve, to the air damper, and to the gas butterfly valve, if used.
When properly adjusted, a coordinated movement of the damper and metering valves within the limits of the
modulating motor travel is attained to provide proper fuel-air ratios through the firing range.
In linkage adjustments there are several important factors that must serve as guides.
1. The modulating motor must be able to complete its full travel range.
!
DANGER
CAUTION
Do not restrict the full travel of the modulating motor. Failure to follow these instructions could re-
sult in equipment damage.
2. Initial adjustment should be made with the motor in full closed position, that is with the shaft on the power end of
the motor in its most counterclockwise position.
3. The closer the linkage rod connector is to the drive shaft, the less the arm will travel; the closer the connector is to
the driven shaft, the farther that arm will travel.
Prior to initially firing a boiler it is advisable to check for free movement of the linkage. The damper motor
must be allowed to complete its full stroke and the damper must move freely from low to high fire position.
C. MODULATING MOTOR
The modulating motor has a 90
shaft rotation. The motor manufacturer also provides a 160
stroke model
for other applications. If a replacement is obtained from someone other than a Cleaver-Brooks Service or Parts
representative, it may have an incorrect stroke. To prevent damage, verify the 90
stroke prior to installing a
replacement.
The stroke may be determined by powering the motor and connecting terminals R-B to actually determine the
stroke as motor drives to an open position.
D. MODULATING MOTOR SWITCHES - LOW FIRE AND HIGH FIRE
The modulating motor contains either one or two internal switches depending upon application. The
microswitches are actuated by adjustable cams attached to the motor shaft.
Factory replacement motors have the cams preset. The low fire start switch is set to make the red and yellow
leads at approximately 8
on motor closing. The high fire purge air proving switch (located in the modulating
motor) is set to make red and blue tracer leads at approximately 60
the on motor opening. Normally the
settings are left as is, but job conditions may require readjustment. If the cams require adjustment or resetting,
follow the instructions in the manufacturer’s technical manual.
E. BURNER OPERATING CONTROLS - GENERAL
Note: Adjustments to the boiler operating controls should be made by an authorized Cleaver-Brooks
Service Technician. Refer to the appropriate boiler Operation and Maintenance manual for specific
information on boiler startup and operation.
The standard boiler operating control package consists of three separate controls, the High Limit Control,
Operating Limit Control and the Modulating control.
The High Limit Control senses the hot water temperature or steam pressure. It is used as a safety limit to turn
the burner off in the event the operating limit control fails. The high limit control should be set sufficiently
above the operating limit control to avoid nuisance shutdowns.
A
B
C
D
E
F
G
8
Содержание FLX 1000
Страница 12: ...Chapter 1 General Description 1 6 750 177...
Страница 68: ...Chapter 2 Profire V Burner 2 56 750 177...
Страница 90: ...Chapter 4 Sequence of Operation 4 10 750 177...
Страница 104: ...Chapter 5 Adjustment Procedures 5 14 750 177...
Страница 110: ...Chapter 6 Troubleshooting 6 6 750 177...
Страница 122: ...8 2 750 177 Figure 8 1 Typical Hot Water Flextube Casing...
Страница 124: ...8 4 750 177 Figure 8 2 Typical Low Pressure Steam Flextube Casing...
Страница 126: ...8 6 750 177 Figure 8 3 Typical High Pressure Steam Flextube Casing...
Страница 128: ...Parts Chapter 8 8 8 750 177 Steam Pressure Controls...
Страница 129: ...Chapter 8 Parts 750 177 8 9 Water Level Controls...
Страница 130: ...Parts Chapter 8 8 10 750 177 Water Level Controls continued...
Страница 131: ...Chapter 8 Parts 750 177 8 11 Water Column Main and Aux 15 Steam...
Страница 132: ...Parts Chapter 8 8 12 750 177 Water Column Main and Aux 150 Steam...
Страница 133: ...Chapter 8 Parts 750 177 8 13 Safety Valves...
Страница 134: ...Parts Chapter 8 8 14 750 177...
Страница 135: ......
Страница 136: ...e mail info cleaverbrooks com Web Address http www cleaverbrooks com...