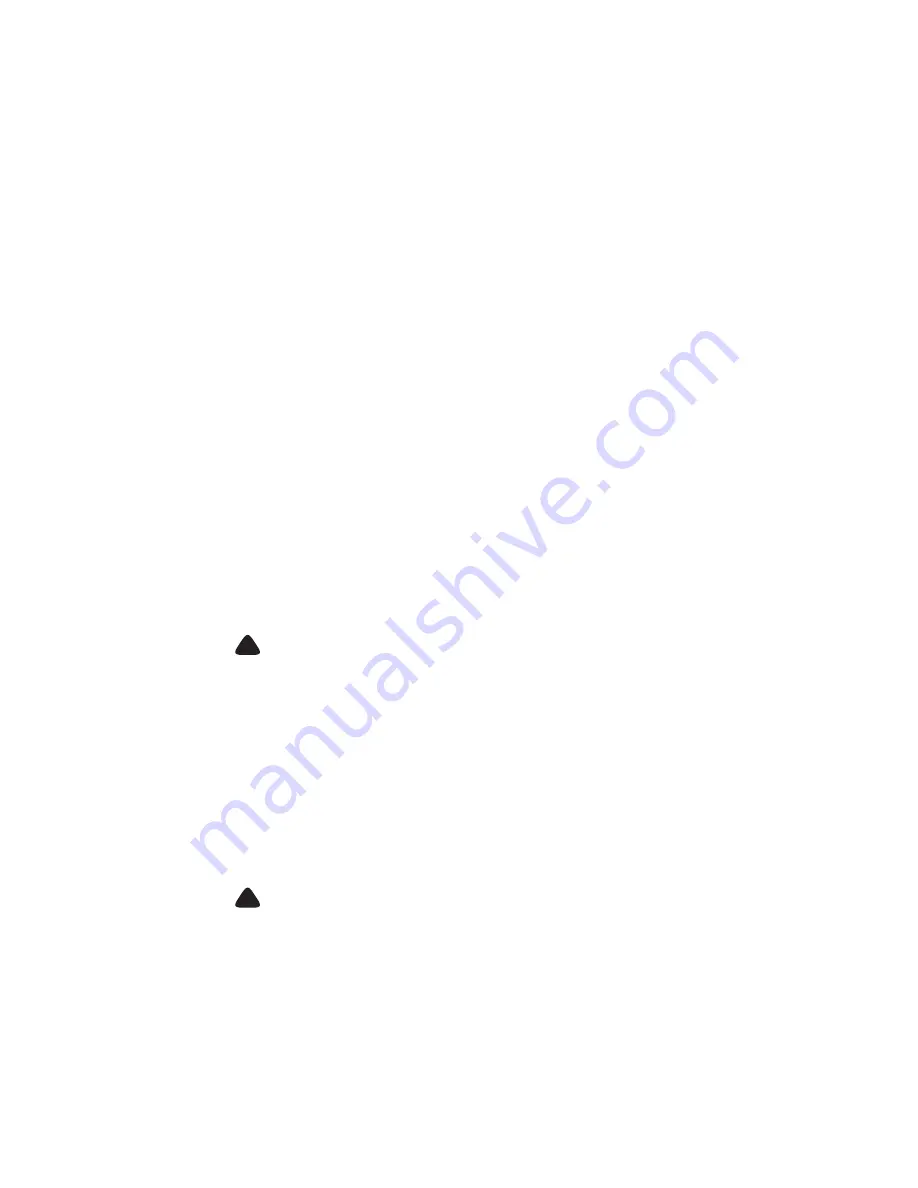
General Description
Chapter 3
750-177
3-11
J. Preparation for Extended Layup
Many boilers used for heating or seasonal loads or for standby service may have extended periods of non-use.
The procedures outlined in this section are designed to allow a boiler to be kept off line for any period of time
without damage to the unit. Special care must be taken so that neither waterside nor fireside surfaces are
allowed to deteriorate from corrosion. Operating boilers can be protected from corrosion and scale by applying
various chemical treatments and monitoring the system on a regular basis. However, boilers that are taken off
line, even for short intervals, are susceptible to oxygen attack. Boiler drums and/or tubes may sustain pitting
type damage during either wet or dry layup if proper precautions are not taken.
Oxygen solubility at ambient (off-line) temperatures can be many times that of normal boiler operating
temperatures. The higher the oxygen concentration, the greater the oxygen corrosion potential. Problems also
can occur as a result of improper shutdown procedures, where settled solids can dry in a hard, adherent
deposit.
Care must be take to prevent fireside corrosion, especially when firing oil that contains sulfur. Dormant periods,
and even frequent shutdowns, expose the fireside surfaces to condensation during cooling. Moisture and any
sulfur residue can form an acid solution. Under certain conditions, and especially in areas with high humidity,
the corrosive effect of the acid can be serious. An acid solution could eat through or severely damage boiler
tubes or other metal heating surfaces during the time that a boiler is out of service.
Too many conditions exist to lay down definite rules for individual installations. In general, there are two
methods of storage: wet or dry. Your local Cleaver-Brooks authorized representative can recommend the better
method based on the circumstances of your particular installation. Regardless of the method employed, the
boiler should be thoroughly cleaned and inspected prior to storage. With either method, common sense
dictates a periodic recheck of fireside and waterside conditions during layup to meet the requirements of
special or job site conditions.
Preparing The Boiler For Layup
To prepare a boiler for layup, thoroughly clean the fireside by removing any soot or other products of
combustion from the tubes, exposed drum surfaces, and refractory.
!
DANGER
CAUTION
The insulating refractory covering the top of the bottom drum must be protected from damage when
work is being done in the boiler furnace area. Damage to the insulation may eventually cause dam-
age to the boiler itself.
Generally, a good brushing will clean fireside surfaces. Use a wire brush for metal surfaces and a soft bristle
brush for the refractory. Sweep away or vacuum any accumulation.
To prevent condensation from forming in the control cabinet, keep the control circuit energized. For extended
layup periods, especially where high humidity or large swings in ambient temperature occur, the flame
safeguard control should be removed and stored in a dry atmosphere.
It is recommended that the burner air inlet be blocked to prevent the flow of warm, moist air through the boiler.
!
DANGER
CAUTION
A label should be affixed to the burner advising that the air inlet has been blocked. Failure to remove
the air inlet block when attempting to operate the burner may result in damage to the equipment.
Dry Storage
Dry storage generally is used for boilers that are to be out of service for some time or for boilers that might be
subjected to freezing conditions. With the dry storage method, the boiler must be thoroughly dried because
any moisture would cause corrosion. Drying can be accomplished by the use of a small stove or heater.
Содержание FLX 1000
Страница 12: ...Chapter 1 General Description 1 6 750 177...
Страница 68: ...Chapter 2 Profire V Burner 2 56 750 177...
Страница 90: ...Chapter 4 Sequence of Operation 4 10 750 177...
Страница 104: ...Chapter 5 Adjustment Procedures 5 14 750 177...
Страница 110: ...Chapter 6 Troubleshooting 6 6 750 177...
Страница 122: ...8 2 750 177 Figure 8 1 Typical Hot Water Flextube Casing...
Страница 124: ...8 4 750 177 Figure 8 2 Typical Low Pressure Steam Flextube Casing...
Страница 126: ...8 6 750 177 Figure 8 3 Typical High Pressure Steam Flextube Casing...
Страница 128: ...Parts Chapter 8 8 8 750 177 Steam Pressure Controls...
Страница 129: ...Chapter 8 Parts 750 177 8 9 Water Level Controls...
Страница 130: ...Parts Chapter 8 8 10 750 177 Water Level Controls continued...
Страница 131: ...Chapter 8 Parts 750 177 8 11 Water Column Main and Aux 15 Steam...
Страница 132: ...Parts Chapter 8 8 12 750 177 Water Column Main and Aux 150 Steam...
Страница 133: ...Chapter 8 Parts 750 177 8 13 Safety Valves...
Страница 134: ...Parts Chapter 8 8 14 750 177...
Страница 135: ......
Страница 136: ...e mail info cleaverbrooks com Web Address http www cleaverbrooks com...