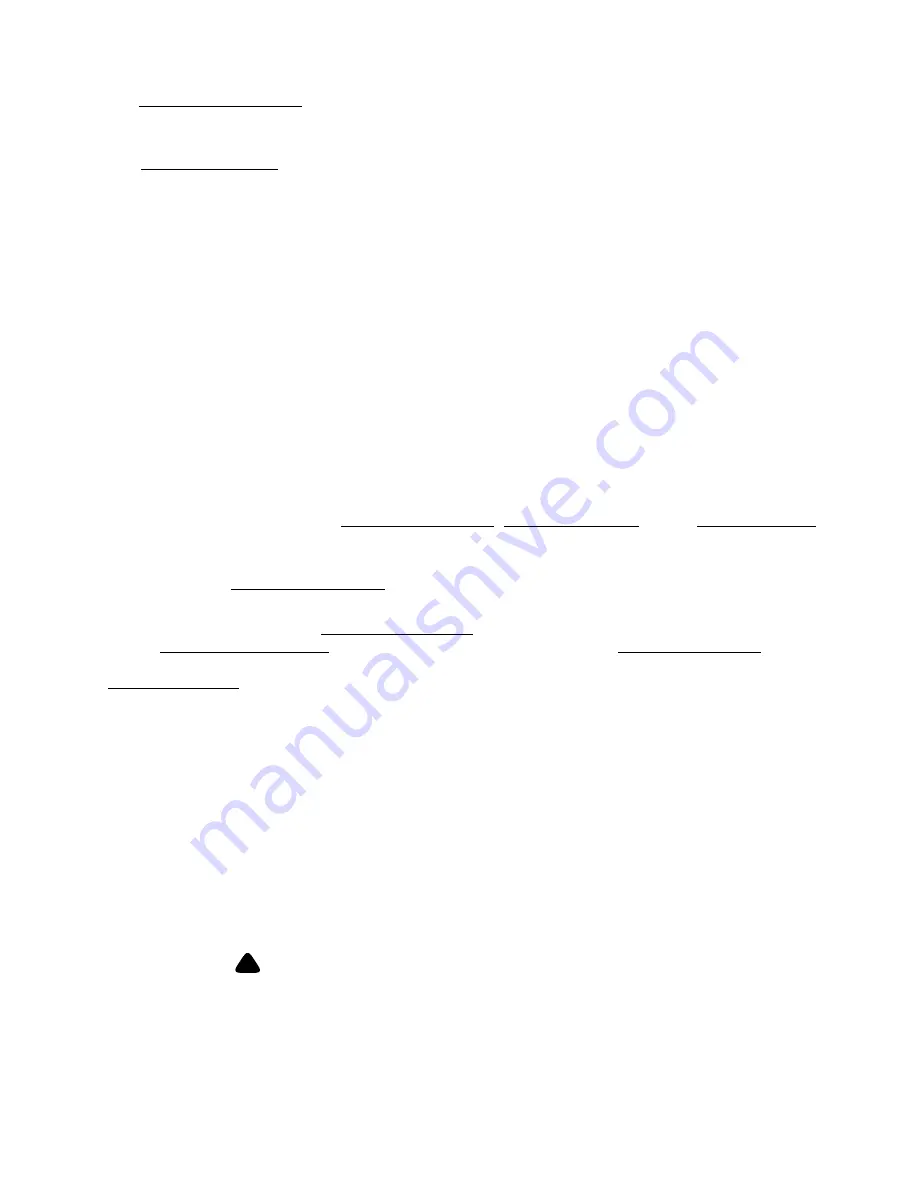
Adjustment Procedures
Chapter 5
750-177
5-3
The Operating Limit Control senses temperature or pressure and automatically turns the burner on to initiate
the start-up sequence when required and turns the burner off to initiate the shutdown sequence when the
demand is satisfied. The control must be set to initiate startup only at the low fire position.
The Modulating Control senses changes in the hot water temperature or steam pressure and signals the
modulating motor to control the flow of fuel and air to the burner. With either steam or hot water boilers, the
modulating control must be set to ensure the burner is at its minimum low fire position before the operating
limit control either starts or stops the burner.
When adjusting or setting controls, first be sure all control devices are securely mounted and level. With the
temperature sensing control, make sure the sensing bulb is properly bottomed in its well and is secured against
movement. Be sure the connecting tubing is not kinked.
The dial settings are generally accurate; although it is not unusual to have a slight variation between a scale
setting and an actual pressure gauge or thermometer reading. Always adjust control setting to agree with
pressure gauge or thermometer readings. Accurate instrument readings are required. When necessary use
auxiliary test equipment to set controls.
Burner controls correctly set to match load demands will provide operational advantages and achieve the
following desirable objectives:
• The burner will be operating in low fire position prior to shut down.
• The burner will operate at low fire for a brief period on each start during normal operation.
• Eliminates frequent burner on-off cycling.
Separate and independent controls affect modulated firing and burner on-off cycling. Figure 5-3 depicts a
typical setting relationship of the operating limit control, modulating control and the high limit control.
The burner will be “on” whenever the pressure or temperature is less than point
B
and “off” whenever
pressure or temperature is greater than point
A
. The distance between points
A
and
B
represents the “on-off”
differential of the operating limit control.
In normal operation, the burner will shut down whenever the pressure or temperature rises above setting
A
.
At that point the switch in the operating limit control will open. As the pressure or temperature drops back to
B
, the operating limit control closes and the burner will restart. The modulating control will signal the
modulating motor to be in a low fire position. If the load demands exceed the low fire input potential, the
modulating control will increase the firing rate proportionately as pressure or temperature falls toward point
D
. The modulating motor will stop at any intermediate point between
C
and
D
whenever the fuel input
balances the load requirement.
As the load requirement changes, the firing rate will change accordingly. Thus it is referred to as
modulated
firing.
Point
D
represents the maximum firing rate of the burner, or highfire. In the event pressure or temperature
drops while the burner is firing at highfire, it indicates that the load exceeds the capacity of the boiler.
The firing graph (Figure 5-1) shows that point
B
and point
C
do not coincide. Extreme load conditions could
require the points be closely matched.
When set as shown, with a time lag between
B
and
C
, the burner will be in a low fire position upon a restart
and will fire at that rate for a short period of time before falling pressure or temperature requires an increase
in the firing rate.
!
DANGER
CAUTION
Excessive cycling increases the potential and severity of internal condensation. On-Off cycling
should be limited to eight (8) cycles or less per hour to keep the blower motor from overheating and
excessive wear on the switch gear and pilot. Failure to follow these instructions could result in dam-
age and premature failure of the equipment.
A
B
Содержание FLX 1000
Страница 12: ...Chapter 1 General Description 1 6 750 177...
Страница 68: ...Chapter 2 Profire V Burner 2 56 750 177...
Страница 90: ...Chapter 4 Sequence of Operation 4 10 750 177...
Страница 104: ...Chapter 5 Adjustment Procedures 5 14 750 177...
Страница 110: ...Chapter 6 Troubleshooting 6 6 750 177...
Страница 122: ...8 2 750 177 Figure 8 1 Typical Hot Water Flextube Casing...
Страница 124: ...8 4 750 177 Figure 8 2 Typical Low Pressure Steam Flextube Casing...
Страница 126: ...8 6 750 177 Figure 8 3 Typical High Pressure Steam Flextube Casing...
Страница 128: ...Parts Chapter 8 8 8 750 177 Steam Pressure Controls...
Страница 129: ...Chapter 8 Parts 750 177 8 9 Water Level Controls...
Страница 130: ...Parts Chapter 8 8 10 750 177 Water Level Controls continued...
Страница 131: ...Chapter 8 Parts 750 177 8 11 Water Column Main and Aux 15 Steam...
Страница 132: ...Parts Chapter 8 8 12 750 177 Water Column Main and Aux 150 Steam...
Страница 133: ...Chapter 8 Parts 750 177 8 13 Safety Valves...
Страница 134: ...Parts Chapter 8 8 14 750 177...
Страница 135: ......
Страница 136: ...e mail info cleaverbrooks com Web Address http www cleaverbrooks com...