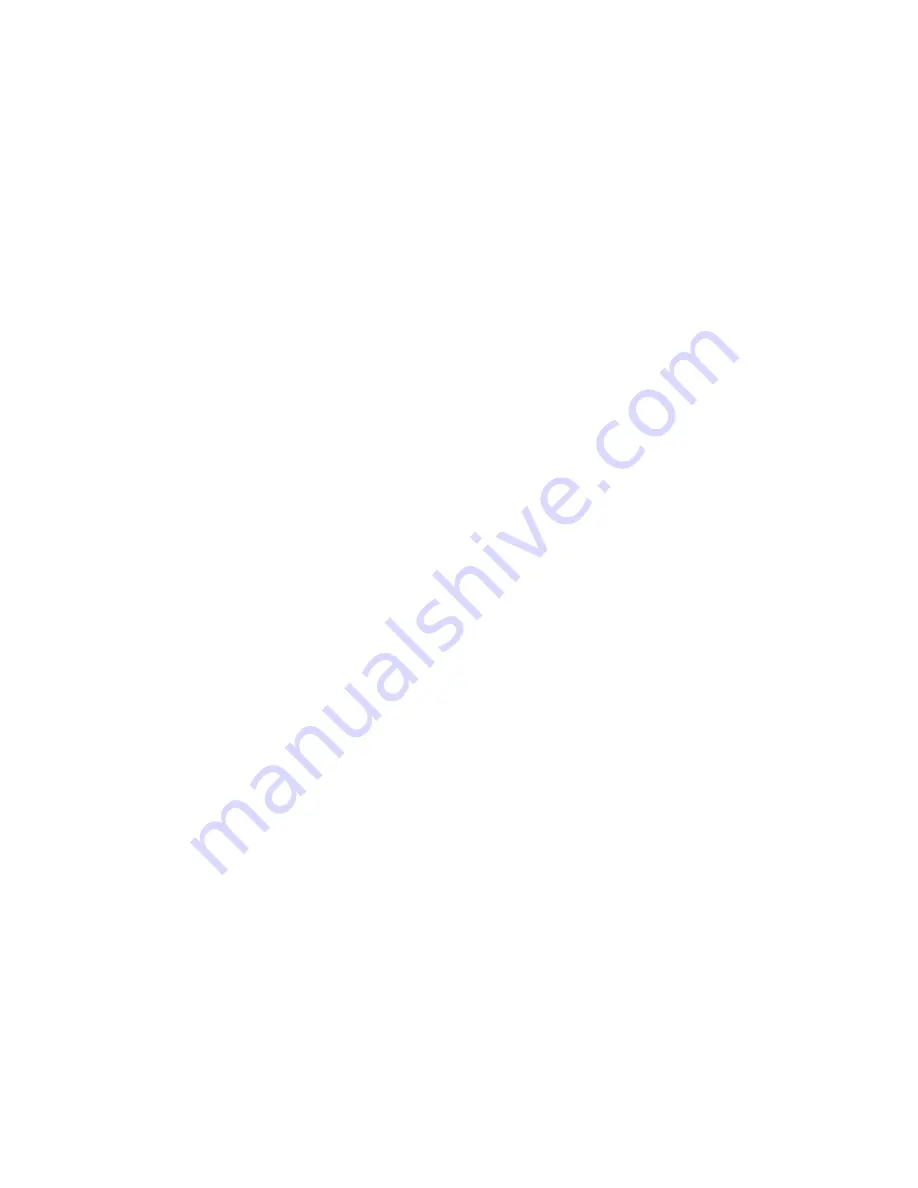
Chapter 2
Profire V Burner
2-38
750-177
for a smooth ignition of the main flame. Disconnect the wiring to the solenoid on the Suntec B2TC-8931 oil pump.
Loosen and remove the knurled nut on the solenoid. Adjust the screw, clockwise to increase the low-fire oil pres-
sure, and counterclockwise to decrease the low-fire oil pressure, until a smooth ignition of the oil flame is obtained
and a satisfactory low-fire oil flame is established. Turn the burner off and restart to ensure smooth ignition is
obtained at the set low-fire pressure. Replace knurled nut and tighten finger tight.
4. Adjust the high-fire oil input to match the maximum rating. Turn the burner off and reconnect the wiring to the sole-
noid valve. Restart the burner and allow the burner to go through ignition and low-fire. When the solenoid ener-
gizes, the oil pump discharge pressure is at high-fire pressure. The high-fire pressure adjustment screw is located
on the oil pump body. Adjust the screw, clockwise to increase the pressure and counterclockwise to decrease the
pressure, until the correct amount of oil pressure is obtained. The high-fire oil pressure should be 300 psi. High-fire
is typically 3.5% to 4.5% O2, with less than No.1 smoke (Bacharach). The burner should be adjusted to provide
the correct amount of fuel flow at a constant rate at high-fire position as indicated on the burner data plate located
inside the control panel.
5. Tighten all linkages and marked settings. Complete the Startup Report.
LOW-HIGH-OFF/LOW OIL BURNER ADJUSTMENT
The Suntec B2TD-8842 oil pump is typically incorporated and is a two-stage, two-step oil pump. The lowfire
pressure adjustment is 100 - 200 psi (solenoid de-energized). High-fire pressure adjustment is 200 - 300 psi
(solenoid energized).
1. Turn the burner switch to the “ON” position.
2. Adjust low-fire with the oil pressure regulating valve to have approximately 100 to 200 psi, and adjust the
air shutter for a clean fire. Record the combustion reading from the flue gas analyzer, normally 3.5% to 4.5%
O2 and less than No. 1 smoke (Bacharach). To adjust the oil pressure regulating valve, remove the lockscrew
and adjust the pressure by turning the allen screw clockwise to increase pressure, and counterclockwise to
decrease pressure.
3. Operate the boiler at low-fire until it is up to operating pressure (steam) or temperature (hot water).
4. Adjust high-fire fuel input to match maximum oil pressure. At high-fire, the pressure should be 300 psi.
Verify and record the readings and pressures. High-fire is typically 3.5% to 4.5% O2 with less than No. 1
smoke (Bacharach). The burner should be adjusted to provide correct fuel flow at a constant rate, at the low-
fire and high-fire position as indicated on the burner data plate.
5. Tighten all linkages and marked settings. Complete the Startup Report.
FULL MODULATION OIL BURNER ADJUSTMENT
The oil burner adjustments consist of the oil metering valve and air damper shutters. The oil metering valve
position (indicated by a scale on the valve) will vary the oil pressure to the nozzle. Models V13 to V34 use a
simplex oil nozzle, while models V35 to V168 use a return flow oil nozzle. An oil pressure gauge should be
installed in the return line to monitor the oil pressure. At low-fire, the pressure range in the return line should
be between 40 and 80 PSI with the oil metering valve position set between 6 and 8 on the scale. At highfire,
the return line pressure will vary from 135 to 200 PSI dependent upon the brand of the oil nozzle. At high-
fire, the oil metering valve position will be approximately 2 on the scale.
1. Set the “MANUAL-AUTO” switch on the “MANUAL” position.
2. Position the manual flame control potentiometer in the “CLOSED” (low-fire) position.
3. Turn the burner switch to the “ON” position. The burner will start and be in the low-fire position.
4. Adjust low-fire with the metering valve position to have approximately 80 to 90 psi, and adjust the lowfire air shut-
ter for a clean fire. Record the combustion reading from the flue gas analyzer, normally 4.5% to 6.5% O2 and less
Содержание FLX 1000
Страница 12: ...Chapter 1 General Description 1 6 750 177...
Страница 68: ...Chapter 2 Profire V Burner 2 56 750 177...
Страница 90: ...Chapter 4 Sequence of Operation 4 10 750 177...
Страница 104: ...Chapter 5 Adjustment Procedures 5 14 750 177...
Страница 110: ...Chapter 6 Troubleshooting 6 6 750 177...
Страница 122: ...8 2 750 177 Figure 8 1 Typical Hot Water Flextube Casing...
Страница 124: ...8 4 750 177 Figure 8 2 Typical Low Pressure Steam Flextube Casing...
Страница 126: ...8 6 750 177 Figure 8 3 Typical High Pressure Steam Flextube Casing...
Страница 128: ...Parts Chapter 8 8 8 750 177 Steam Pressure Controls...
Страница 129: ...Chapter 8 Parts 750 177 8 9 Water Level Controls...
Страница 130: ...Parts Chapter 8 8 10 750 177 Water Level Controls continued...
Страница 131: ...Chapter 8 Parts 750 177 8 11 Water Column Main and Aux 15 Steam...
Страница 132: ...Parts Chapter 8 8 12 750 177 Water Column Main and Aux 150 Steam...
Страница 133: ...Chapter 8 Parts 750 177 8 13 Safety Valves...
Страница 134: ...Parts Chapter 8 8 14 750 177...
Страница 135: ......
Страница 136: ...e mail info cleaverbrooks com Web Address http www cleaverbrooks com...