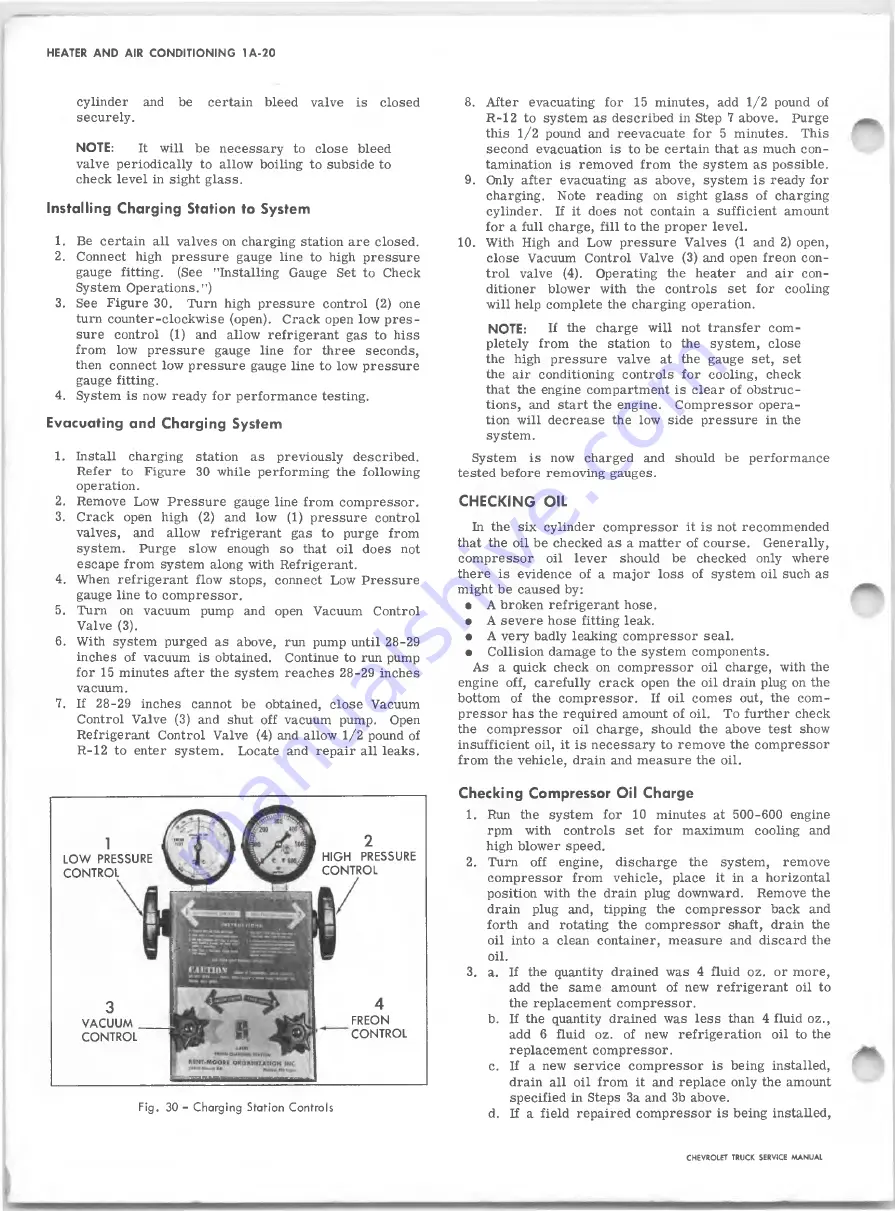
HEATER AND AIR CONDITIONING 1A-20
cylinder and be certain bleed valve is closed
securely.
NOTE:
It will be necessary to close bleed
valve periodically to allow boiling to subside to
check level in sight glass.
Installing Charging Station to System
1. Be certain all valves on charging station are closed.
2. Connect high pressure gauge line to high pressure
gauge fitting. (See "Installing Gauge Set to Check
System Operations.")
3. See Figure 30. Turn high pressure control (2) one
turn counter-clockwise (open). Crack open low pres
sure control (
1
) and allow refrigerant gas to hiss
from low pressure gauge line for three seconds,
then connect low pressure gauge line to low pressure
gauge fitting.
4. System is now ready for performance testing.
Evacuating and Charging System
1. Install charging station as previously described.
Refer to Figure 30 while performing the following
operation.
2. Remove Low Pressure gauge line from compressor.
3. Crack open high (2) and low (1) pressure control
valves, and allow refrigerant gas to purge from
system. Purge slow enough so that oil does not
escape from system along with Refrigerant.
4. When refrigerant flow stops, connect Low Pressure
gauge line to compressor.
5. Turn on vacuum pump and open Vacuum Control
Valve (3).
6
. With system purged as above, run pump until 28-29
inches of vacuum is obtained. Continue to run pump
for 15 minutes after the system reaches 28-29 inches
vacuum.
7. If 28-29 inches cannot be obtained, close Vacuum
Control Valve (3) and shut off vacuum pump. Open
Refrigerant Control Valve (4) and allow 1/2 pound of
R-12 to enter system. Locate and repair all leaks.
F ig . 30 - Charging Station Controls
8
. After evacuating for 15 minutes, add 1/2 pound of
R-12 to system as described in Step 7 above. Purge
this 1/2 pound and reevacuate for 5 minutes. This
second evacuation is to be certain that as much con
tamination is removed from the system as possible.
9. Only after evacuating as above, system is ready for
charging. Note reading on sight glass of charging
cylinder. If it does not contain a sufficient amount
for a full charge, fill to the proper level.
10. With High and Low pressure Valves (1 and 2) open,
close Vacuum Control Valve (3) and open freon con
trol valve
(4 ).
Operating the heater and air con
ditioner blower with the controls set for cooling
will help complete the charging operation.
NOTE:
If the charge will not transfer com
pletely from the station to the system, close
the high pressure valve at the gauge set, set
the air conditioning controls for cooling, check
that the engine compartment is clear of obstruc
tions, and start the engine. Compressor opera
tion will decrease the low side pressure in the
system.
System is now charged and should be performance
tested before removing gauges.
CHECKING OIL
In the six cylinder compressor it is not recommended
that the oil be checked as a matter of course. Generally,
compressor oil lever should be checked only where
there is evidence of a major loss of system oil such as
might be caused by:
• A broken refrigerant hose.
• A severe hose fitting leak.
• A very badly leaking compressor seal.
• Collision damage to the system components.
As a quick check on compressor oil charge, with the
engine off, carefully crack open the oil drain plug on the
bottom of the compressor. If oil comes out, the com
pressor has the required amount of oil. To further check
the compressor oil charge, should the above test show
insufficient oil, it is necessary to remove the compressor
from the vehicle, drain and measure the oil.
Checking Compressor Oil Charge
1. Run the system for 10 minutes at 500-600 engine
rpm with controls set for maximum cooling and
high blower speed.
2. Turn off engine, discharge the system, remove
compressor from vehicle, place it in a horizontal
position with the drain plug downward. Remove the
drain plug and, tipping the compressor back and
forth and rotating the compressor shaft, drain the
oil into a clean container, measure and discard the
oil.
3. a. If the quantity drained was
4
fluid oz. or more,
add the same amount of new refrigerant oil to
the replacement compressor.
b. If the quantity drained was less than
4
fluid oz.,
add
6
fluid oz. of new refrigeration oil to the
replacement compressor.
c. If a new service compressor is being installed,
drain all oil from it and replace only the amount
specified in Steps 3a and 3b above.
d. If a field repaired compressor is being installed,
1
L O W P R E S S U R E
C O N T R O L
2
H IG H P R E S S U R E
C O N T R O L
3
V A C U U M
C O N T R O L
4
FR EO N
C O N T R O L
CHEVROLET TRUCK SERVICE MANUAL
Содержание 10 Series 1967
Страница 1: ...CHASSIS V3 a n s W U gw...
Страница 2: ......
Страница 28: ......
Страница 39: ...HEATER AND AIR CONDITIONING 1A 11 EVAPORATOR OUTLET Fig 20 Airflow Schematic CHEVROLET TRUCK SERVICE MANUAL...
Страница 80: ...BODY IB 18 Fig 41 Exploded View of Level Ride Seat CHEVROLET TRUCK SERVICE MANUAL...
Страница 89: ...BODY IB 27 CHEVROLET TRUCK SERVICE MANUAL...
Страница 105: ...BODY IB 43 Fig 94 Check Link Assembly Typical CHEVROLET TRUCK SERVICE MANUAL...
Страница 117: ...BODY IB 55 Fig 116 A uxiliary Seat CHEVROLET TRUCK SERVICE MANUAL...
Страница 121: ...Fig 4 1 0 3 0 Series Truck Frame...
Страница 122: ...Fig 5 4 0 6 0 Single A xle Truck Frames Exc T ilt Cab FRAME 2 4...
Страница 124: ...CHEVROLET TRUCK SERVICE MANUAL 1 Ficu 7 4 0 6 0 Series T ilt Cab Truck Frames FRAME 2 6...
Страница 128: ...CHEVROLET TRUCK SERVICE MANUAL Fig 8 Underbody Reference Points and Dimensions Chevy Van G10 and 20 FRAME 2 10...
Страница 207: ...REAR SUSPENSION AND DRIVE LINE 4 49 Fig 91 Tandem Rear Axles and Power Divider CHEVROLET TRUCK SERVICE MANUAL...
Страница 228: ...BRAKES 5 12 TD 50 60 Fig 23 Parking Brake Cables T Models CHEVROLET TRUCK SERVICE MANUAL...
Страница 280: ......
Страница 324: ...I I...
Страница 336: ...ENGINE FUEL 6M 12 CHEVROLET TRUCK SERVICE MANUAL...
Страница 342: ......
Страница 348: ......
Страница 386: ......
Страница 393: ...CHEVROLET TRUCK SERVICE MANUAL CLUTCHES AND TRANSMISSIONS 7 7...
Страница 452: ...FUEL TANK AND EXHAUST SYSTEMS 8 6 Fig 7 Fuel Lines and Filter CD50 60 CHEVROLET TRUCK SERVICE MANUAL...
Страница 472: ...STEERING 9 18 Fig 31 Typical Power Steering Hose Routing CHEVROLET TRUCK SERVICE MANUAL...
Страница 474: ...w j...
Страница 486: ......
Страница 500: ...1...
Страница 502: ...l c t r iC al 12 2...
Страница 506: ...ELECTRICAL BODY AND CHASSIS 12 6 VIEW C Fig 9 Front Lighting Assemblies CHEVROLET TRUCK SERVICE MANUAL...
Страница 532: ...ELECTRICAL BODY AND CHASSIS 12 32 Fig 42 Engine Compartment PT 20 30 CHEVROLET TRUCK SERVICE MANUAL...
Страница 535: ...ELECTRICAL BODY AND CHASSIS 12 35 Fig 45 Engine Compartment CS40 50 60 MS60 CHEVROLET TRUCK SERVICE MANUAL...
Страница 561: ...ELECTRICAL BODY AND CHASSIS 12 61 18 DG 18 DG Fig 71 Instrument Panel G A 10 20 CHEVROLET TRUCK SERVICE MANUAL...
Страница 562: ...ELECTRICAL BODY AND CHASSIS 12 62 Fig 72 Engine and Tail Lamps G A 10 20 CHEVROLET TRUCK SERVICE MANUAL...
Страница 566: ...ELECTRICAL BODY AND CHASSIS 12 66 Fig 76 Engine Compartment SE50 60 CHEVROLET TRUCK SERVICE MANUAL...
Страница 568: ......
Страница 576: ......
Страница 580: ...1...
Страница 587: ...SPECIFICATIONS 7 ENGINE SECTION 6 8 25 1 on CE TE400 Series CHEVROLET TRUCK SERVICE MANUAL...
Страница 590: ...SPECIFICATIONS 10 ENGINE TORQUES CHEVROLET TRUCK SERVICE MANUAL...