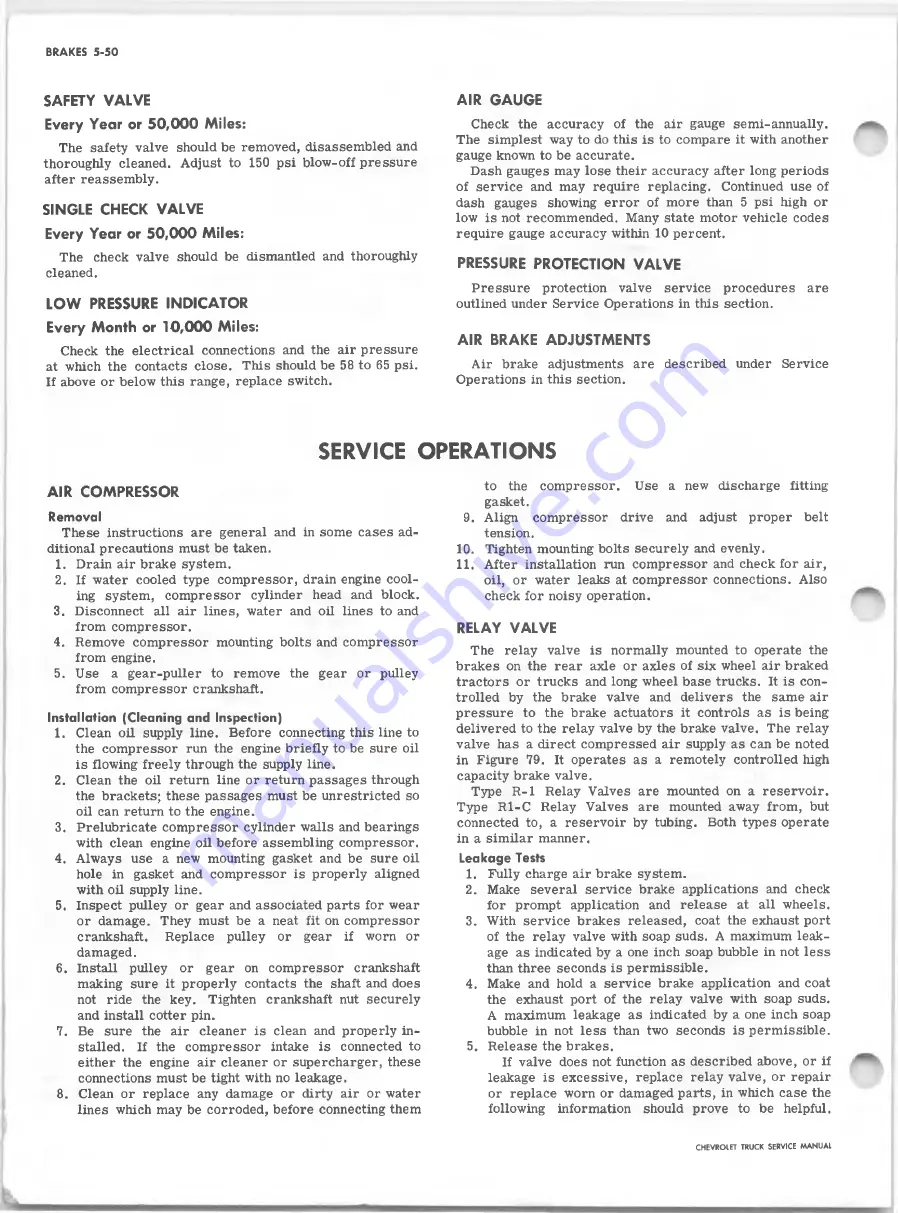
BRAKES 5-50
SAFETY VALVE
Every Year or 50,000 Miles:
The safety valve should be removed, disassembled and
thoroughly cleaned. Adjust to 150 psi blow-off pressure
after reassembly.
SINGLE CHECK VALVE
Every Year or 50,000 Miles:
The check valve should be dismantled and thoroughly
cleaned.
LOW PRESSURE INDICATOR
Every Month or 10,000 Miles:
Check the electrical connections and the air pressure
at which the contacts close. This should be 58 to 65 psi.
If above or below this range, replace switch.
AIR GAUGE
Check the accuracy of the air gauge semi-annually.
The simplest way to do this is to compare it with another
gauge known to be accurate.
Dash gauges may lose their accuracy after long periods
of service and may require replacing. Continued use of
dash gauges showing error of more than 5 psi high or
low is not recommended. Many state motor vehicle codes
require gauge accuracy within
1 0
percent.
PRESSURE PROTECTION VALVE
Pressure protection valve service procedures are
outlined under Service Operations in this section.
AIR BRAKE ADJUSTMENTS
Air brake adjustments are described under Service
Operations in this section.
SERVICE OPERATIONS
AIR COMPRESSOR
Removal
These instructions are general and in some cases ad
ditional precautions must be taken.
1. Drain air brake system.
2. If water cooled type compressor, drain engine cool
ing system, compressor cylinder head and block.
3. Disconnect all air lines, water and oil lines to and
from compressor.
4. Remove compressor mounting bolts and compressor
from engine.
5. Use a gear-puller to remove the gear or pulley
from compressor crankshaft.
Installation (Cleaning and Inspection)
1. Clean oil supply line. Before connecting this line to
the compressor run the engine briefly to be sure oil
is flowing freely through the supply line.
2. Clean the oil return line or return passages through
the brackets; these passages must be unrestricted so
oil can return to the engine.
3. Prelubricate compressor cylinder walls and bearings
with clean engine oil before assembling compressor.
4. Always use a new mounting gasket and be sure oil
hole in gasket and compressor is properly aligned
with oil supply line.
5. Inspect pulley or gear and associated parts for wear
or damage. They must be a neat fit on compressor
crankshaft.
Replace pulley or gear if worn or
damaged.
6
. Install pulley or gear on compressor crankshaft
making sure it properly contacts the shaft and does
not ride the key. Tighten crankshaft nut securely
and install cotter pin.
7. Be sure the air cleaner is clean and properly in
stalled. If the compressor intake is connected to
either the engine air cleaner or supercharger, these
connections must be tight with no leakage.
8
. Clean or replace any damage or dirty air or water
lines which may be corroded, before connecting them
to the compressor. Use a new discharge fitting
gasket.
9. Align compressor drive and adjust proper belt
tension.
10. Tighten mounting bolts securely and evenly.
11. After installation run compressor and check for air,
oil, or water leaks at compressor connections. Also
check for noisy operation.
RELAY VALVE
The relay valve is normally mounted to operate the
brakes on the rear axle or axles of six wheel air braked
tractors or trucks and long wheel base trucks. It is con
trolled by the brake valve and delivers the same air
pressure to the brake actuators it controls as is being
delivered to the relay valve by the brake valve. The relay
valve has a direct compressed air supply as can be noted
in Figure 79. It operates as a remotely controlled high
capacity brake valve.
Type R -l Relay Valves are mounted on a reservoir.
Type R l-C Relay Valves are mounted away from, but
connected to, a reservoir by tubing. Both types operate
in a sim ilar manner.
Leakage Tests
1. Fully charge air brake system.
2. Make several service brake applications and check
for prompt application and release at all wheels.
3. With service brakes released, coat the exhaust port
of the relay valve with soap suds. A maximum leak
age as indicated by a one inch soap bubble in not less
than three seconds is permissible.
4. Make and hold a service brake application and coat
the exhaust port of the relay valve with soap suds.
A maximum leakage as indicated by a one inch soap
bubble in not less than two seconds is permissible.
5. Release the brakes.
If valve does not function as described above, or if
leakage is excessive, replace relay valve, or repair
or replace worn or damaged parts, in which case the
following information should prove to be helpful.
CHEVROLET TRUCK SERVICE M ANUAL
Содержание 10 Series 1967
Страница 1: ...CHASSIS V3 a n s W U gw...
Страница 2: ......
Страница 28: ......
Страница 39: ...HEATER AND AIR CONDITIONING 1A 11 EVAPORATOR OUTLET Fig 20 Airflow Schematic CHEVROLET TRUCK SERVICE MANUAL...
Страница 80: ...BODY IB 18 Fig 41 Exploded View of Level Ride Seat CHEVROLET TRUCK SERVICE MANUAL...
Страница 89: ...BODY IB 27 CHEVROLET TRUCK SERVICE MANUAL...
Страница 105: ...BODY IB 43 Fig 94 Check Link Assembly Typical CHEVROLET TRUCK SERVICE MANUAL...
Страница 117: ...BODY IB 55 Fig 116 A uxiliary Seat CHEVROLET TRUCK SERVICE MANUAL...
Страница 121: ...Fig 4 1 0 3 0 Series Truck Frame...
Страница 122: ...Fig 5 4 0 6 0 Single A xle Truck Frames Exc T ilt Cab FRAME 2 4...
Страница 124: ...CHEVROLET TRUCK SERVICE MANUAL 1 Ficu 7 4 0 6 0 Series T ilt Cab Truck Frames FRAME 2 6...
Страница 128: ...CHEVROLET TRUCK SERVICE MANUAL Fig 8 Underbody Reference Points and Dimensions Chevy Van G10 and 20 FRAME 2 10...
Страница 207: ...REAR SUSPENSION AND DRIVE LINE 4 49 Fig 91 Tandem Rear Axles and Power Divider CHEVROLET TRUCK SERVICE MANUAL...
Страница 228: ...BRAKES 5 12 TD 50 60 Fig 23 Parking Brake Cables T Models CHEVROLET TRUCK SERVICE MANUAL...
Страница 280: ......
Страница 324: ...I I...
Страница 336: ...ENGINE FUEL 6M 12 CHEVROLET TRUCK SERVICE MANUAL...
Страница 342: ......
Страница 348: ......
Страница 386: ......
Страница 393: ...CHEVROLET TRUCK SERVICE MANUAL CLUTCHES AND TRANSMISSIONS 7 7...
Страница 452: ...FUEL TANK AND EXHAUST SYSTEMS 8 6 Fig 7 Fuel Lines and Filter CD50 60 CHEVROLET TRUCK SERVICE MANUAL...
Страница 472: ...STEERING 9 18 Fig 31 Typical Power Steering Hose Routing CHEVROLET TRUCK SERVICE MANUAL...
Страница 474: ...w j...
Страница 486: ......
Страница 500: ...1...
Страница 502: ...l c t r iC al 12 2...
Страница 506: ...ELECTRICAL BODY AND CHASSIS 12 6 VIEW C Fig 9 Front Lighting Assemblies CHEVROLET TRUCK SERVICE MANUAL...
Страница 532: ...ELECTRICAL BODY AND CHASSIS 12 32 Fig 42 Engine Compartment PT 20 30 CHEVROLET TRUCK SERVICE MANUAL...
Страница 535: ...ELECTRICAL BODY AND CHASSIS 12 35 Fig 45 Engine Compartment CS40 50 60 MS60 CHEVROLET TRUCK SERVICE MANUAL...
Страница 561: ...ELECTRICAL BODY AND CHASSIS 12 61 18 DG 18 DG Fig 71 Instrument Panel G A 10 20 CHEVROLET TRUCK SERVICE MANUAL...
Страница 562: ...ELECTRICAL BODY AND CHASSIS 12 62 Fig 72 Engine and Tail Lamps G A 10 20 CHEVROLET TRUCK SERVICE MANUAL...
Страница 566: ...ELECTRICAL BODY AND CHASSIS 12 66 Fig 76 Engine Compartment SE50 60 CHEVROLET TRUCK SERVICE MANUAL...
Страница 568: ......
Страница 576: ......
Страница 580: ...1...
Страница 587: ...SPECIFICATIONS 7 ENGINE SECTION 6 8 25 1 on CE TE400 Series CHEVROLET TRUCK SERVICE MANUAL...
Страница 590: ...SPECIFICATIONS 10 ENGINE TORQUES CHEVROLET TRUCK SERVICE MANUAL...