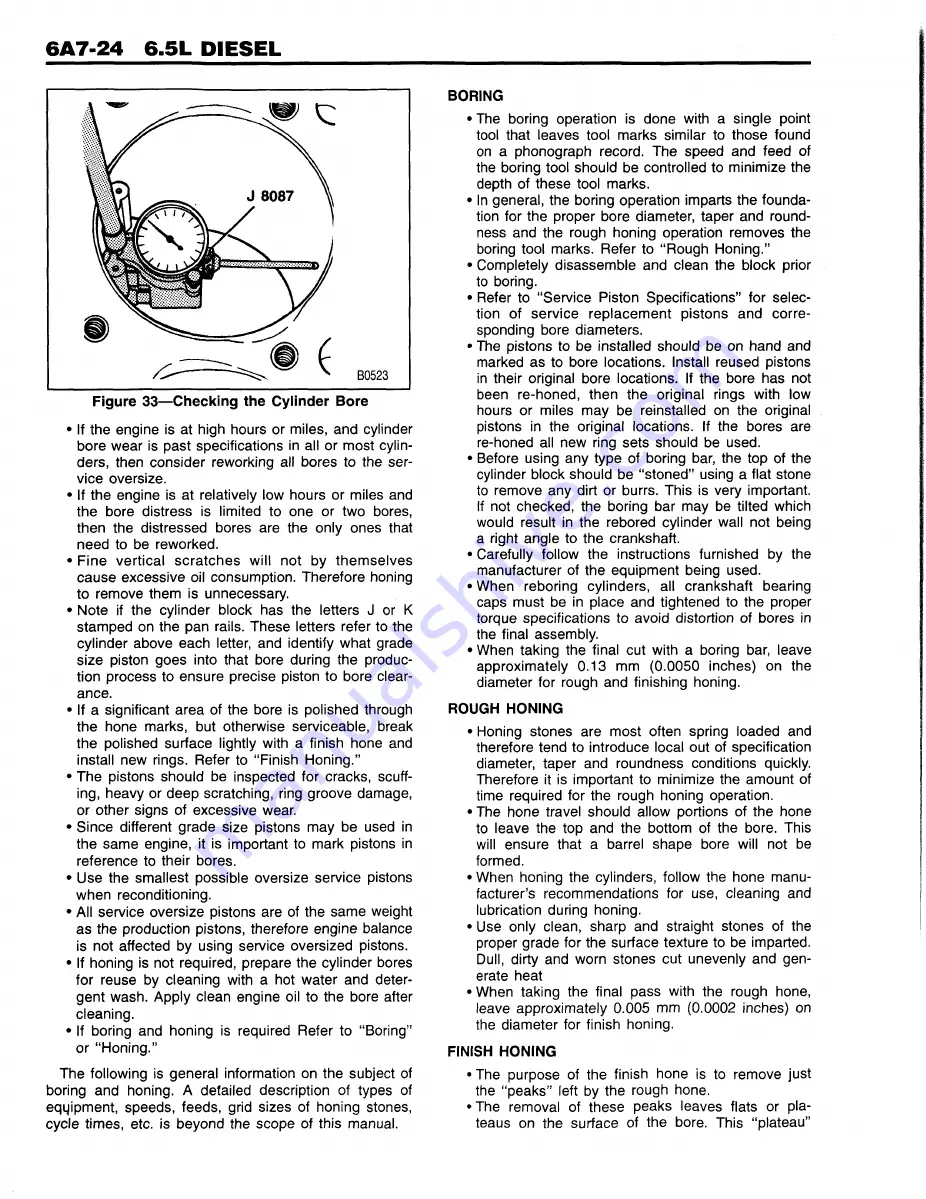
Figure 33— Checking the Cylinder Bore
• If the engine is at high hours or miles, and cylinder
bore wear is past specifications in all or most cylin
ders, then consider reworking all bores to the ser
vice oversize.
• If the engine is at relatively low hours or miles and
the bore distress is limited to one or two bores,
then the distressed bores are the only ones that
need to be reworked.
• Fine vertical scratches will not by them selves
cause excessive oil consumption. Therefore honing
to remove them is unnecessary.
• Note if the cylinder block has the letters J or K
stamped on the pan rails. These letters refer to the
cylinder above each letter, and identify what grade
size piston goes into that bore during the produc
tion process to ensure precise piston to bore clear
ance.
• If a significant area of the bore is polished through
the hone marks, but otherwise serviceable, break
the polished surface lightly with a finish hone and
install new rings. Refer to “ Finish Honing.”
• The pistons should be inspected for cracks, scuff
ing, heavy or deep scratching, ring groove damage,
or other signs of excessive wear.
• Since different grade size pistons may be used in
the same engine, it is important to mark pistons in
reference to their bores.
• Use the smallest possible oversize service pistons
when reconditioning.
• All service oversize pistons are of the same weight
as the production pistons, therefore engine balance
is not affected by using service oversized pistons.
• If honing is not required, prepare the cylinder bores
for reuse by cleaning with a hot water and deter
gent wash. Apply clean engine oil to the bore after
cleaning.
• If boring and honing is required Refer to “ Boring”
or “ Honing.”
The following is general information on the subject of
boring and honing. A detailed description of types of
equipment, speeds, feeds, grid sizes of honing stones,
cycle times, etc. is beyond the scope of this manual.
BORING
• The boring operation is done with a single point
tool that leaves tool marks similar to those found
on a phonograph record. The speed and feed of
the boring tool should be controlled to minimize the
depth of these tool marks.
• In general, the boring operation imparts the founda
tion for the proper bore diameter, taper and round
ness and the rough honing operation removes the
boring tool marks. Refer to “ Rough Honing.”
• Completely disassemble and clean the block prior
to boring.
• Refer to “ Service Piston Specifications” for selec
tion of service replacement pistons and corre
sponding bore diameters.
• The pistons to be installed should be on hand and
marked as to bore locations. Install reused pistons
in their original bore locations. If the bore has not
been re-honed, then the original rings with low
hours or miles may be reinstalled on the original
pistons in the original locations. If the bores are
re-honed all new ring sets should be used.
• Before using any type of boring bar, the top of the
cylinder block should be “ stoned” using a flat stone
to remove any dirt or burrs. This is very important.
If not checked, the boring bar may be tilted which
would result in the rebored cylinder wall not being
a right angle to the crankshaft.
• Carefully follow the instructions furnished by the
manufacturer of the equipment being used.
• When reboring cylinders, all crankshaft bearing
caps must be in place and tightened to the proper
torque specifications to avoid distortion of bores in
the final assembly.
• When taking the final cut with a boring bar, leave
approximately 0.13 mm (0.0050 inches) on the
diameter for rough and finishing honing.
ROUGH HONING
• Honing stones are most often spring loaded and
therefore tend to introduce local out of specification
diameter, taper and roundness conditions quickly.
Therefore it is important to minimize the amount of
time required for the rough honing operation.
•T h e hone travel should allow portions of the hone
to leave the top and the bottom of the bore. This
will ensure that a barrel shape bore will not be
formed.
• When honing the cylinders, follow the hone manu
facturer’s recommendations for use, cleaning and
lubrication during honing.
• Use only clean, sharp and straight stones of the
proper grade for the surface texture to be imparted.
Dull, dirty and worn stones cut unevenly and gen
erate heat
• When taking the final pass with the rough hone,
leave approximately 0.005 mm (0.0002 inches) on
the diameter for finish honing.
FINISH HONING
• The purpose of the finish hone is to remove just
the “ peaks” left by the rough hone.
• The removal of these peaks leaves flats or pla
teaus on the surface of the bore. This “ plateau”
Содержание Light Duty Truck 1994 Series
Страница 1: ......
Страница 11: ...VIEW A p n n n j VIEW C F7554 Figure 10 Hydra Matic 4L60 E Transmission I D Location ...
Страница 15: ...G VAN MODELS Rally Sportvan Cutaway Van Extended Van Vandura Chevy Van Magnavan Hi Cube Van F7569 ...
Страница 17: ...S T PICKUP REGULAR CAB 2 DOOR S T UTILITY VEHICLE S T PICKUP EXTENDED CAB 4 DOOR S T UTILITY VEHICLE 2900r4506 ...
Страница 24: ...NOTES ...
Страница 26: ... ...
Страница 69: ...NOTES ...
Страница 71: ...3 2 STEERING ...
Страница 73: ......
Страница 84: ......
Страница 102: ...40 ...
Страница 130: ...NOTES ...
Страница 146: ...NOTES ...
Страница 162: ...NOTES ...
Страница 166: ...Figure 5 Removing the Pinion Flange Figure 6 Pressing the Drive Pinion from the Cage ...
Страница 178: ...Figure 3 Spreading the Differential Case Figure 4 Removing the Differential ...
Страница 190: ...NOTES ...
Страница 202: ...NOTES ...
Страница 206: ...F5785 ...
Страница 209: ...Figure 11 Remove the Pinion Flange F4696 F4759 Figure 14 Removing the Differential Side Bearing ...
Страница 212: ...B Button Moved Out of Bearing Bore F5791 ...
Страница 228: ...NOTES ...
Страница 232: ......
Страница 234: ......
Страница 236: ...Adjuster 63 Bolt 64 Lock Figure 10 Turning the Adjuster Plug K3 Models ...
Страница 237: ...Figure 13 Removing the Pinion Seal 39 Bearing Cup Figure 16 Removing the Inner Bearing Cap ...
Страница 247: ...C Measure with Axle Shaft Forced Outboard 1 Shaft 5 Tube 9 Carrier Connector 23 Output Shaft 29 Carrier Case F5877 ...
Страница 261: ...F7475 ...
Страница 267: ...B Button Moved Out of Bearing Bore F5791 ...
Страница 294: ...NOTES ...
Страница 300: ...NOTES ...
Страница 318: ...NOTES ...
Страница 322: ...SR207LN2 EDS ...
Страница 324: ......
Страница 326: ...OVERHEAD OILING AND RETURN MAIN OIL GALLERY N30005 6A2 J EDS ...
Страница 368: ...103 153 127 V1200 ...
Страница 370: ......
Страница 372: ......
Страница 374: ...F9375 Figure 7 Engine Lubrication Diagram Engines Without Balance Shaft ...
Страница 375: ...Front View Rear View Showing Path Of Oil To Timing Chain Showing Main Gallery Oil Filter And Crankshaft Oil Feed V0575 ...
Страница 376: ...Figure 9 Engine Lubrication Diagram Engines With Balance Shaft ...
Страница 399: ...V2974 ...
Страница 410: ......
Страница 412: ...195 196 201 174 252 163 165 164 244 3706r3924 ...
Страница 452: ......
Страница 454: ...163 164 V1202 ...
Страница 456: ...20 21x 302 210 4 0 41 2 5 2 5 1 2 51 4 2 e3 54 3 9 252 252 S 255 255 25 6 256 209 V1196 ...
Страница 458: ...100 1 8 4 185 183 177 v 75 201 3706r1204 ...
Страница 460: ......
Страница 510: ......
Страница 512: ...V2131 ...
Страница 514: ...110 106 106 103 90 93 89 88 87 86 v 7 7 7 7 j A _ 111 f t 2 a a s 53 49 L 47 46 3706r4751 ...
Страница 516: ...259 260 150 237 S lM 180 167180 J 1 82 183 170 169 1 1 78 1 7 9 213212 2 0 7 205 r i 3706r4752 ...
Страница 566: ...NOTES ...
Страница 574: ...NOTES ...
Страница 618: ...SPECIAL TOOLS ...
Страница 620: ...NOTES ...
Страница 672: ......
Страница 682: ......
Страница 686: ......
Страница 689: ...SPRINGS LOCATED IN THE PUMP PRESSURE CONV CL REGULATOR VALVE SPRINGS LOCATED IN THE VALVE BODY 3 4 SHIFT ...
Страница 694: ...RH0213 4L60 E ...
Страница 695: ...657 659 m i J 8092 H J 34196 4 3 34196 5 657 658 665 J 23907 J 7004 1 J 8092 RH0214 4L60 E ...
Страница 696: ...J 8092 J 34196 4 33 31 J 8092 RH0215 4L60 E ...
Страница 697: ...SPECIAL TOOLS ...
Страница 698: ...SPECIAL TOOLS ...
Страница 758: ...RH0194 4L80 E ...
Страница 764: ......
Страница 770: ...SPECIAL TOOLS ...
Страница 771: ...SPECIAL TOOLS CONT ...
Страница 772: ......
Страница 775: ......
Страница 776: ......
Страница 785: ......
Страница 804: ...NOTES ...
Страница 806: ......
Страница 808: ......
Страница 822: ...3707r5079 ...
Страница 840: ......
Страница 848: ...NOTES ...
Страница 852: ......
Страница 859: ...17 Rear Case Half 18 Oil Pump Pick Up Tube 26 Connector Dowel Pin Location Pump Pick Up Screen F5434 ...
Страница 860: ...F5435 ...
Страница 866: ......
Страница 878: ...F9167 ...
Страница 882: ...16 FrontOutputShaft 18 DrivtQNr 19 DrivenGm t 20 DriveChain 22 FrontOutputBearing V2836 ...
Страница 890: ...F9168 ...
Страница 908: ......
Страница 914: ...J 2619 01 46 Rear Case 85 Front Output Shaft Rear Bearing F7659 Figure 21 Removing the Front Output Shaft Rear Bearing ...
Страница 919: ......