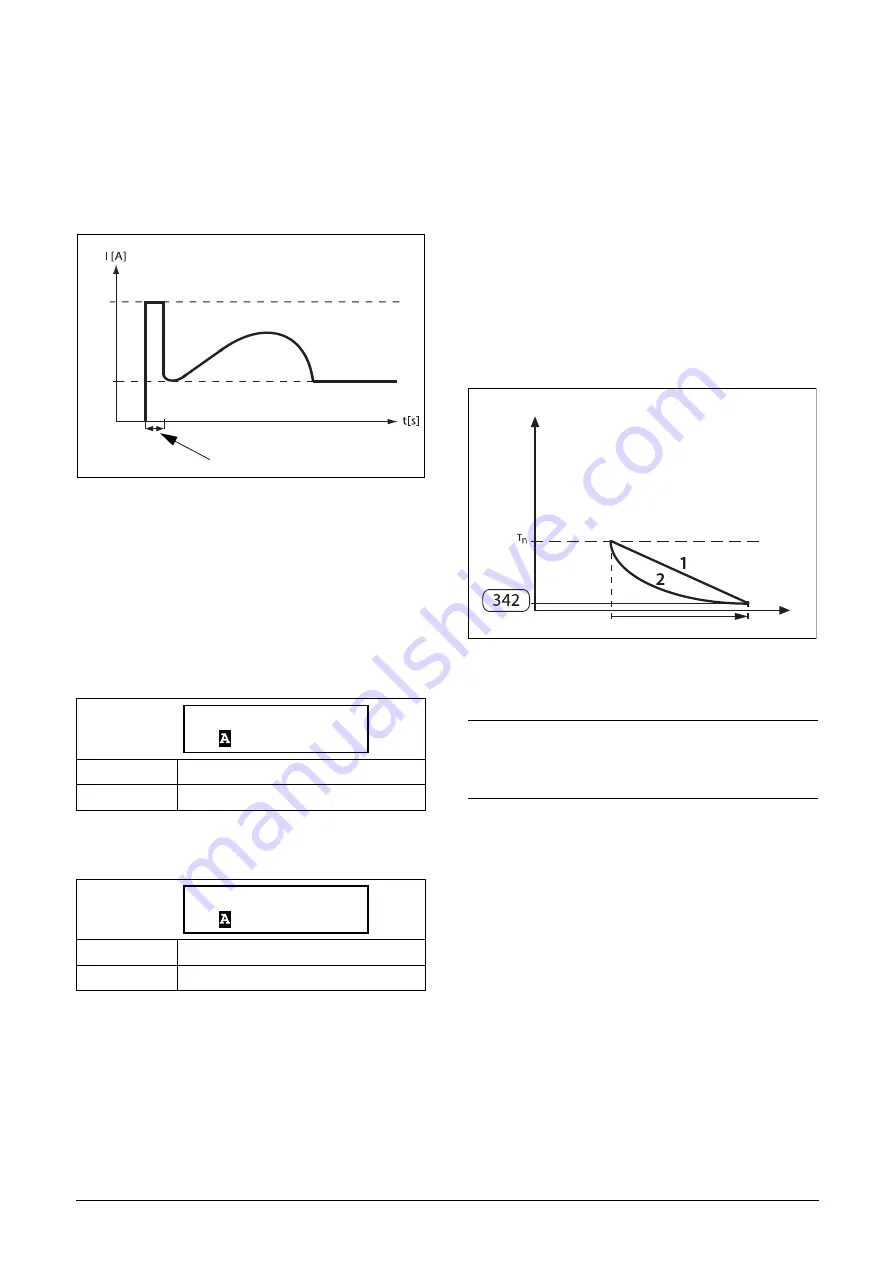
94
Functionality
CG Drives & Automation, 01-5980-01r2
Torque Boost [337]
In specific applications torque boost is required for the start.
The torque boost parameter enables a high torque to be
obtained by providing a high current for 0.1-2 seconds at
start. This enables a soft start of the motor even if the break
away torque is high at the start. An example is crushing mills
applications etc.
Fig. 56 Torque boost principle.
Torque boost may be activated before the start ramp. The
current regulator is activated immediately, and the current is
controlled to be at the set “Torque Boost Current Limit”
[3371] for the set “Torque Boost Time” [3372]. See Fig. 56.
If “torque boost” is used, the total start time is prolonged with
the “Torque Boost Time” [3372].
Torque Boost Current Limit [3371]
Torque Boost Time [3372]
8.3.4
Stop Setting [340]
Stopping is always initiated by triggering of the thyristors to
take over the current when the internal bypass contact is
opened. When the current is correctly flowing through the
thyristors, the selected stop method is executed.
Stop Method [341]
The available stop methods are:
Linear or Square Torque Control
A torque-controlled stop could be used when a sudden stop
of the motor could harm the application. The motor torque
is controlled according to either a linear or a square ramp,
from the actual torque value to the set “End Torque at Stop”
in menu [342]. See Fig. 57 below.
Fig. 57 Torque control at stop
Voltage Control
If a linear voltage-ramp is preferred for the stop, “Voltage
Ctr” is selected as stop method in menu [341]. First the
voltage is reduced to the set “Step Down Voltage at Stop”
[343]. Then a linear ramp will be followed until the
minimum allowed switch-on period is reached, the duration
decided by “Stop Time” [345]. See Fig. 58, page 95.
Coast
The voltage is switched off and the motor is allowed to coast
to a stop.
Brake
Braking may be used in applications where the motor needs
to be stopped quickly. When this selection is made, the
braking method (“Dynamic Vector Brake” or “Reverse
Current Brake”) can be activated in menu [344].
Default:
Off
Range:
Off, 300 - 700% of I
n_mot
[224]
Default:
1.0 s
Range:
0.1 - 2.0 s
Torque boost time
Torque boost current limit
FLC
3371 TB CurrLim
Stp
Off
3372 TB Time
Stp
1.0s
Note: Set the End Torque at Stop so the motor stops
according to the set ramp time.
When the ramp time has passed, the motor will coast if
still rotating.
Time
Torque
Stop time [345]
Nominal torque
End torque
1 Linear
2 Square
Содержание emotron TSA Series
Страница 1: ...Emotron TSA Softstarter Instruction manual English Valid from Software version 1 27...
Страница 2: ......
Страница 4: ......
Страница 6: ...2 CG Drives Automation 01 5980 01r2...
Страница 12: ...8 Introduction CG Drives Automation 01 5980 01r2...
Страница 18: ...14 Mounting CG Drives Automation 01 5980 01r2...
Страница 42: ...38 Application guidelines CG Drives Automation 01 5980 01r2...
Страница 46: ...42 Getting started CG Drives Automation 01 5980 01r2...
Страница 70: ...66 Main features CG Drives Automation 01 5980 01r2...
Страница 142: ...138 Functionality CG Drives Automation 01 5980 01r2...
Страница 158: ...154 Troubleshooting Diagnoses and Maintenance CG Drives Automation 01 5980 01r2...
Страница 160: ...156 Options CG Drives Automation 01 5980 01r2...
Страница 168: ...164 Technical data CG Drives Automation 01 5980 01r2...
Страница 202: ...CG Drives Automation 01 5980 01r2 198...
Страница 203: ......