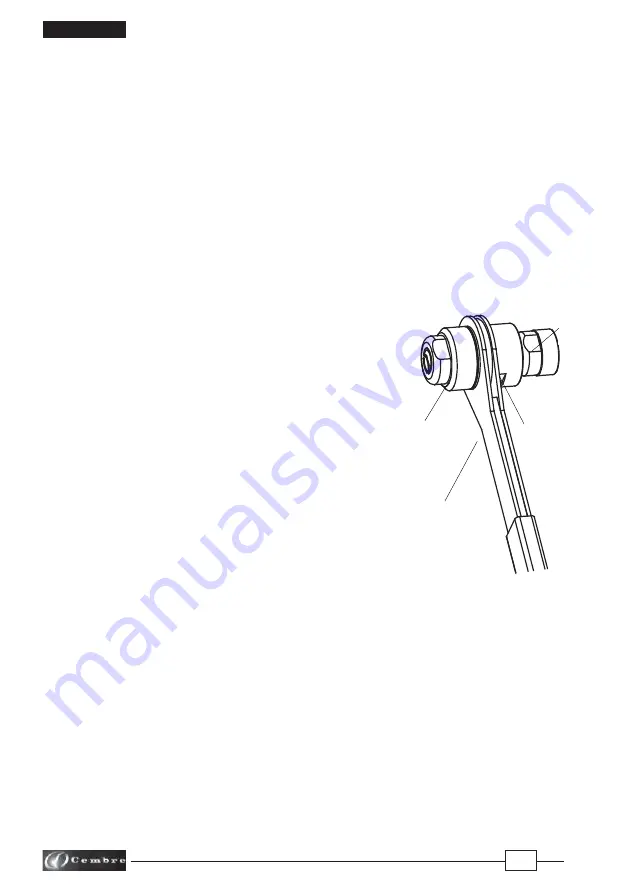
4
ENGLISH
01
06
03
02
FIG. 2
3. INSTRUCTIONS FOR USE
3.1) Setting
(Ref. to Figs. 2 - 7)
– Drill rail web or,
if already drilled, use a suitable tool to clean the hole
(Fig. 3).
– Check the size of the hole with the "GO/NO GO" gauge
CAL ....
;
the hole size is correct
only if the
green part enters the hole
. If the red part enters, the hole is too large (Fig. 4).
– Insert the
AR...-1
copper bush into the rail hole (Fig. 5).
– Turn, anti-clockwise, the support (06) up to the automatic stop (Fig. 2).
In order to achieve the maximum possible stroke length, the support (06) must be completely
turned (anti-clockwise) up to the mechanical stop.
– Insert the calibrated plunger
OG 6.5
into the bush, on the fl ange side ( Fig. 6).
– Using the recess in the gauge
CAL ....
screw and tighten the plunger
OG 6.5
into the tool (Fig. 7).
3.2) Extrusion
(Ref. to Figs. 2; 8; 9)
Before proceeding to the extrusion process, make sure
that the calibrated plunger is fully screwed in the tool
housing.
– Operate the tool, to pull the plunger
OG 6.5
through
the bush and extrude the bush onto the sides of the
hole (Fig. 8), the bush will also extrude itself around the
opposite side of the rail web (Fig. 9).
Should the calibrated plunger not fully exit from the
bush and the tool remain blocked, please proceed as
follows:
– Unscrew and remove the adjustment locking ring (02).
– Remove, reverse and refi t the ratchet handle (01).
– Manually grip the support (06) and rotate the ratchet
handle (01) anti-clockwise, up to the automatic stop.
– Turn the support (06) in a clockwise direction up to the automatic stop.
– Turn the nut (03) in a clockwise direction until the support (06) butts fi rmly against the rail web.
– Remove, reverse and refi t the ratchet handle (01) back to the original position.
– Refi t and tighten the adjustment locking ring (02).
Rotate the ratchet handle (01) in a clockwise direction to complete the installation of the contact
bush.