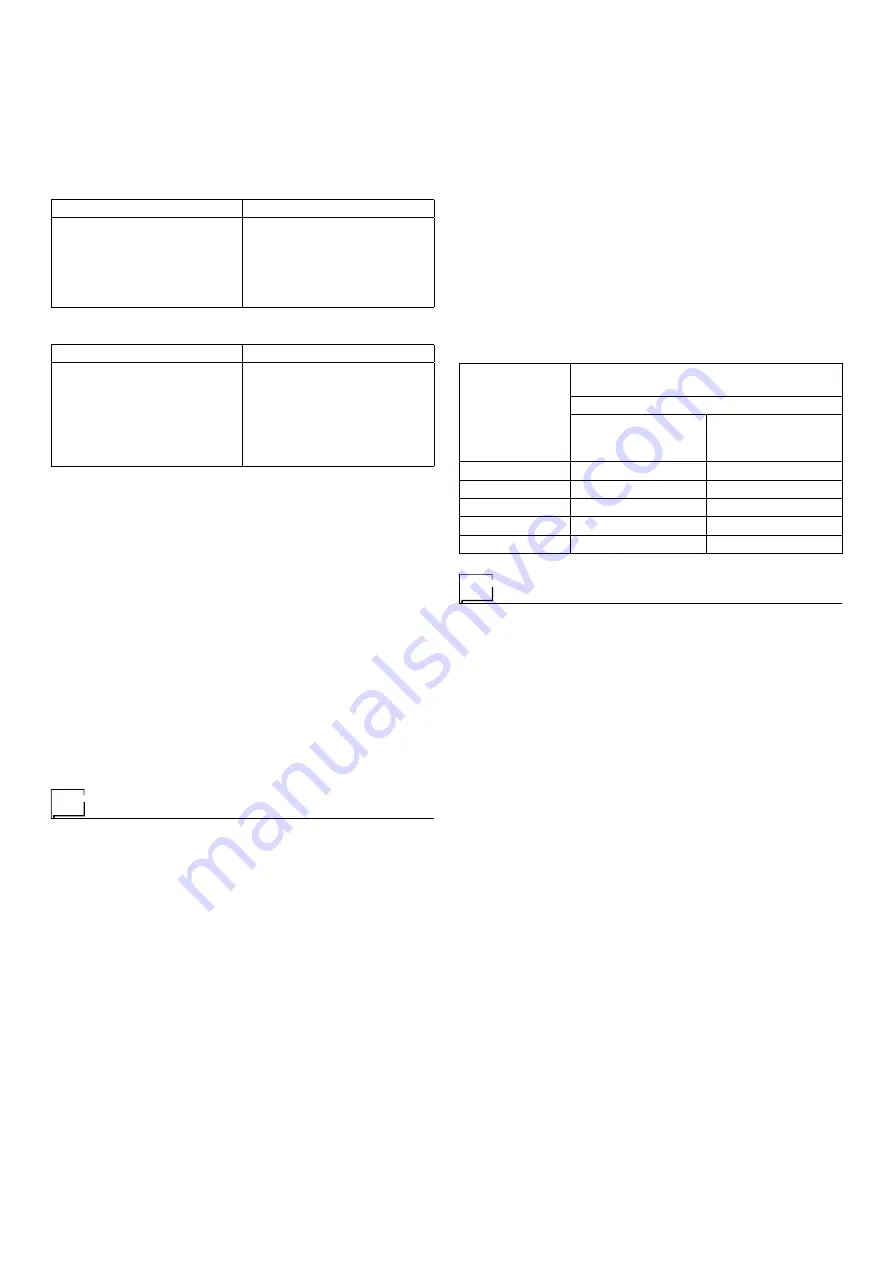
8
WELDING PARAMETERS
Table 3 shows some general indications for the choice of elec-
trode, based on the thickness of the parts to be welded. The
values of current to use are shown in the table 5 with the re-
spective electrodes for the welding of common steels and
low-grade alloys. These data have no absolute value and are
indicative data only. For a precise choice follow the instructions
provided by the electrode manufacturer.
Table 3
Welding thickness (mm)
Ø electrode (mm)
1,2 ÷ 2
1,5 ÷ 3
3 ÷ 5
5 ÷ 12
≥
12
≥
20
1,6
2
2,5
3,25
4
≥
5
Table 4
Ø electrode (mm)
Current (A)
1,6
2
2,5
3,25
4
5
6
30 ÷ 60
40 ÷ 75
60 ÷ 110
95 ÷ 140
140 ÷ 190
190 ÷ 240
220 ÷ 330
The current to be used depends on the welding positions and
the type of joint, and it increases according to the thickness and
dimensions of the part.
The current intensity to be used for the different types of weld-
ing, within the field of regulation shown in table 4 is:
• High for plane, frontal plane and vertical upwards welding.
• Medium for overhead welding.
• Low for vertical downwards welding and for joining small pre-
heated pieces.
A fairly approximate indication of the average current to use in
the welding of electrodes for ordinary steel is given by the fol-
lowing formula:
I = 50 × (Øe - 1)
Where:
I = intensity of the welding current
Øe = electrode diameter
Example:
For electrode diameter 4 mm
I = 50 × (4 - 1) = 50 × 3 = 150A
TIG welding with “Lift”
In the TIG process welding is achieved by melting the two metal
pieces to be joined, with the possible addition of material from
the outside, using an arc ignited by a tungsten electrode. The
“Lift” type ignition used in
DIGITECH vision PULSE
equip-
ments makes it possible to reduce tungsten inclusions on ig-
nition to a minimum. The molten bath and the electrode are
protected by and inert gas (for example, Argon). This type of
welding is used to weld thin sheet metal or when elevated qual-
ity is required.
1) Connecting the welding cables (Fig. E):
• Connect one end of the gas hose to the gas connecter on
the TIG torch and the other end to the pressure reducer
on the inert gas cylinder (Argon or similar).
• With the machine switched off:
- Connect the ground cable to the snap-on connector
(positive).
- Connect the relative ground clamp to the workpiece or
to the workpiece support in an area free of rust, paint,
grease, etc..
- Connect the TIG torch power cable to the snap-on con-
nector marked - (negative).
2) Switch the welding machine on by moving the power sup-
ply switch to
I
(Pos. 3, Fig. A).
3) Make the adjustments and do the parameter settings on
the control panel (for further information see the DH con-
trol panel manual).
4) Open the gas cylinder and regulate the flow by adjusting
the valve on the TIG torch by hand.
5) Ignite the electric arc by contact, using a decisive, quick
movement without dragging the tungsten electrode on the
piece to be welded (“Lift” type ignition).
6) The welder has a SWS “Smart Welding Stop” system for
the end of TIG welding. Lifting up the torch without switch-
ing off the arc will introduce a slope down and it will switch
off automatically.
7) When you have finished welding remember to shut the
valve on the gas cylinder.
Table 5 shows the currents to use with the respective elec-
trodes for TIG DC welding. This input is not absolute but is for
your guidance only; read the electrode manufacturers’ instruc-
tions for a specific choice. The diameter of the electrode to use
is directly proportional to the current being used for welding.
Table 5
Ø ELECTRODE
(mm)
ELECTRODE TYPE
Current adjustment field (A)
TIG DC
Tungsten
Ce 1%
Grey
Tungsten
Rare ground 2%
Turchoise
1
10-50
10-50
1,6
50-80
50-80
2,4
80-150
80-150
3,2
150-250
150-250
4
200-400
200-400
Maintenance
ATTENTION:
Cut off the power supply to the equipment be-
fore effecting any internal inspection.
DIGITECH vision PULSE 3300-4000-5000
IMPORTANT:
For fully electronic welding machines, remov-
ing the dust by sucking it into the machine by the fans, is of ut-
most importance.
In order to achieve correct functioning of the machine, pro-
ceed as described:
• Periodic removal of accumulations of dirt and dust inside the
equipment using compressed air. Do not point the jet of air
directly at the electrical parts as this could damage them.
• Periodical inspection for worn cables or loose connections
that could cause overheating.
TORCH
The torch is subjected to high temperatures and is also stressed
by traction and torsion. We recommend not to twist the wire and
not to use the torch to pull the welder. As a result of the above
the torch will require frequent maintenance such as:
• Cleaning welding splashes from the gas diffuser so that the
gas flows freely.
• Substitution of the contact point when the hole is deformed.
• Cleaning of the wire guide liner using trichloroethylene or
specific solvents.
• Check of the insulation and connections of the power cable;
the connections must be in good electrical and mechanical
condition.
SPARE PARTS
Original spares have been specifically designed for our equip-
ment. The use of spares that are not original may cause vari-
Содержание DIGITECH vision PULSE 3000
Страница 10: ...10 2101EA86 Wiring diagram ...
Страница 12: ......
Страница 19: ...7 21 22 23 24 26 25 27 28 30 41 40 29 30 31 32 33 34 35 36 37 38 39 40 ...
Страница 21: ...9 ...
Страница 22: ...10 ...
Страница 23: ...11 ...
Страница 24: ......
Страница 97: ...73 ...
Страница 98: ...74 ...
Страница 99: ...75 ...
Страница 100: ......