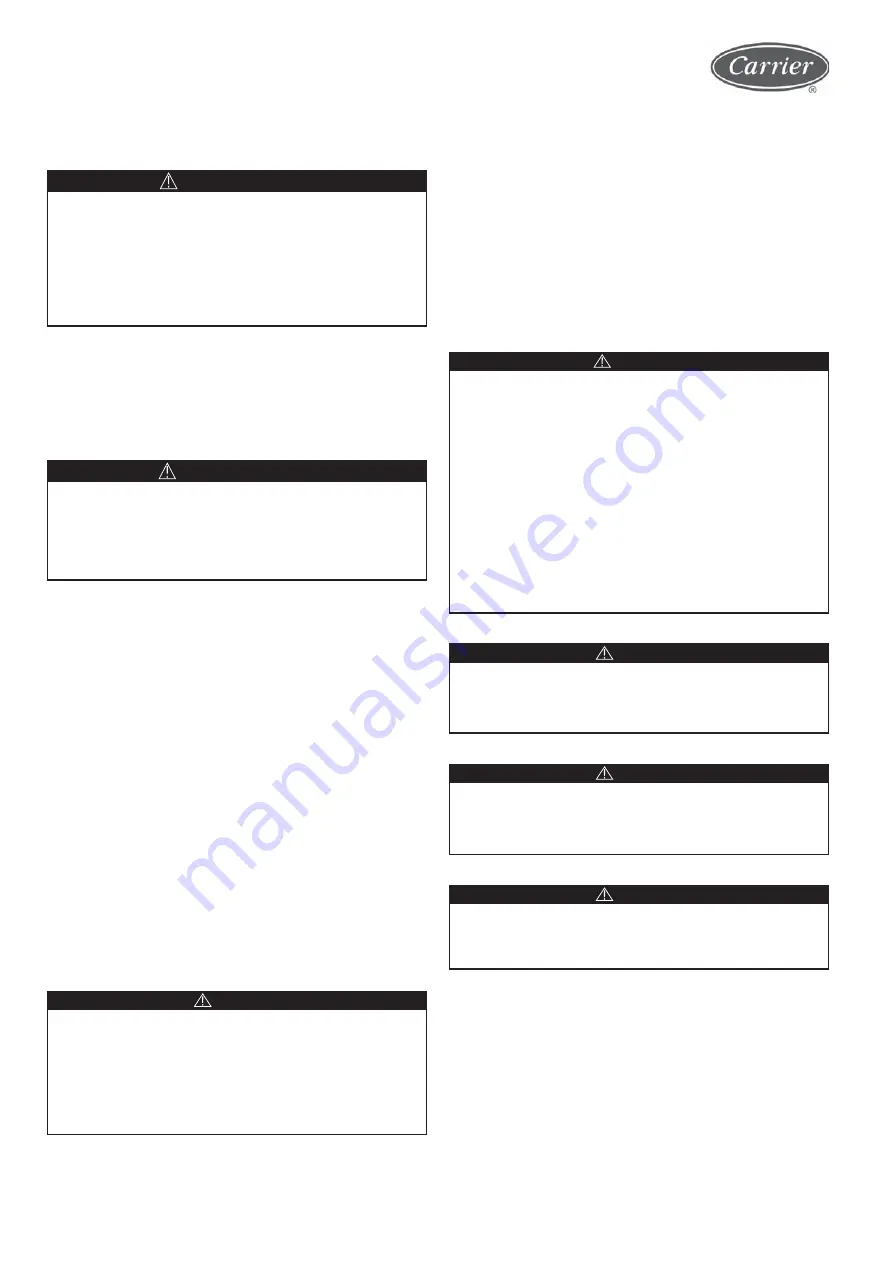
48
6. Maintenance & Repair
All technicians that need to handle the machine for any
purpose must be qualified to work with refrigerant and
electrical circuits.
Crankcase heater
They are supplied in all compressors of the unit to prevent
refrigerant build-up in the oil during equipment shutdowns.
Make sure that the heaters are fi rmly attached to prevent
them from moving.
6.1 - Refrigerant Circuit Maintenance
General maintenance
Keep the unit and the space around it clean and free from
obstructions. Once the installation is complete, remove any
waste, such as packaging materials.
•
Regularly clean the piping, removing all dust and dirt. This
makes it easier to fi nd water leaks, and they can be repaired
before more serious problems occur.
• Confi rm that all connections and gaskets are screwed are
secure. Secure connections prevent leakage and vibration.
•
Check that all insulation gaskets are closed tightly and that
all insulation is fi xed in place. Check all heat exchangers
and pipeline.
Refrigerant circuit
•
Leakage tests: The units are shipped with full R-410A
operating charge (see Attachment 2) and must be under
enough pressure to have a leak test performed.
Before performing any work on the machine, ensure that
the power supply is turned off . If a refrigerant circuit is
opened, it must be evacuated, refi lled and tested for leaks.
Before any operation on a refrigerant circuit, it is necessary
to completely remove the refrigerant charge with a group
of refrigerant charge recovery.
IMPORTANT
This system uses R-410A, which has higher pressures than
R-22 and other refrigerants. No other refrigerant can be
used in this system. The set of pressure gauges, hoses and
recovery systems should be designed for R-410A refrigerant.
If you have questions about the equipment, contact the
equipment manufacturer.
CAUTION
When charging, fl ush water through the cooler throughout
the process to avoid freezing. Damage caused by freezing
can void Carrier’s warranty.
CAUTION
DO NOT OVERLOAD the system. THE overload results in
damage to the compressor as a result of a higher discharge
pressure and higher power consumption.
CAUTION
The refrigerant charge should be removed slowly to
avoid oil losses from the compressor that can result
in a damaged compressor.
CAUTION
Tests for leaks to make sure there were no leaks during unit
transportation. System dehydration is not required, unless all
the refrigerant charge was lost. Do not reuse gaskets. Repair
any leaks found using good cooling practices.
•
Dehydration: Refer to the Carrier’s Standard Service
Techniques Manual, Chapter 1, Refrigerants, Sections 6
and 7 for more details. Do not reuse the compressor to
evacuate the system.
•
Refrigerant charge (See Table 1): Right in front of the drier
fi lter of each circuit there is a factory-installed liquid line
service valve. Each valve has a ¼-inch Schrader connection
to charge liquid refrigerant.
The units have crankcase resistors in the compressors.
The resistors are activated depending on the outside
temperature. If the outside temperature is below 16°C,
leave the units energized for 24 hours before turning
them on.
IMPORTANT
If it is necessary to perform the vacuum procedure in the
interconnection pipes, consider the following items:
•
NEVER use the compressor for the vacuum procedure.
•
For product safe and effi
cient operation it is
essential to ensure the vacuum process and prevent
air from entering during the refrigerant fl uid
charging procedure.
• Failure to follow the above recommendations
can cause potential damage to the product, the
installation and the physical integrity of persons who
are nearby during the procedure.
WARNING