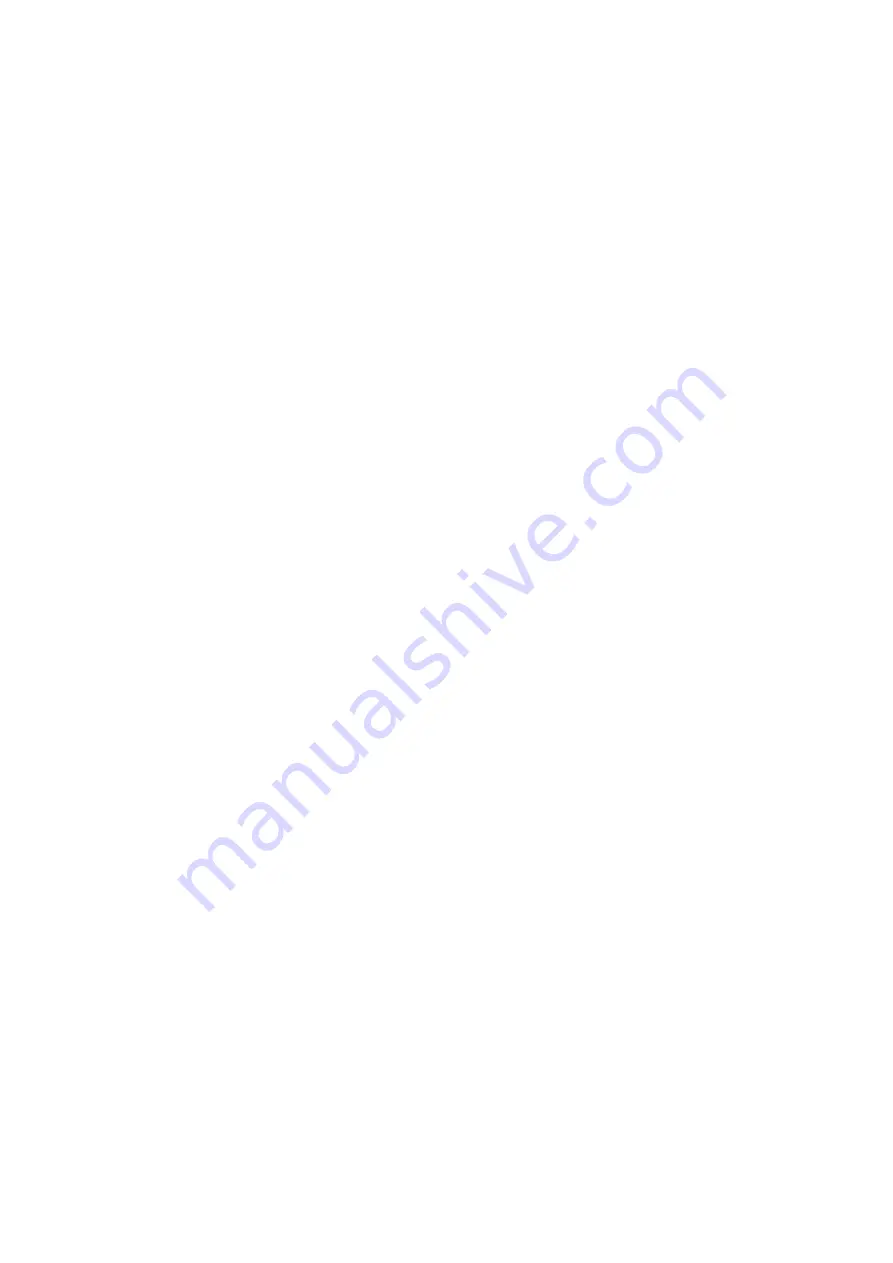
38
Recommendations for maintenance and cleaning of
mChe (microchannel) condenser coils
•
Regular cleaning of the coil surface is essential for
correct unit operation.
•
Eliminating contamination and removal of harmful residue
will increase the operating life of the coils and the unit.
•
The maintenance and cleaning procedures below are
part of the regular maintenance and will prolong the
life of the coils.
•
Specific recommendation in case of snow: For long
term storage, regularly check that no snow has
accumulated on the unit coils.
Products qualified as suitable for cleaning untreated
MCHE coils are available from the Carrier spare parts
network. After cleaning, rinsing of the coil is mandatory
(see Carrier standard RW01--25). The use of any other
cleaning product is strictly prohibited.
•
Remove all foreign objects or fragments/debris
attached to the coil surface or wedged between the
chassis and the supports.
•
Use a low-pressure dry air jet to remove all traces of
dust from the coil.
•
Wear the personal protection equipment, including
safety glasses and or mask, waterproof clothes and
safety gloves. It is recommended to wear clothing that
covers the whole body.
WARNING: Never use pressurised water without a large
diffuser. Concentrated and/or rotating water jets are
strictly forbidden.
Never use a fluid with a temperature above 45°C to clean
the air heat exchangers.
Correct and frequent cleaning (approximately every three
months) will prevent 2/3 of the corrosion problems.
Protect the control box, the motorized ball valve and the
VFD during cleaning operations. Don't forget to remove
protections after cleaning operations.
11.7 - Evaporator maintenance
Check that:
•
The insulating foam is intact and securely in place.
•
The cooler heaters are operating, secure and correctly
positioned.
•
The water-side connections are clean and show no
sign of leakage.
11.8 - compressor maintenance
11.8.1 - oil separator
Check the correct operation of the heaters and check that
they are properly attached to the oil separator shell.
11.8.2 - Integral oil filter change
As system cleanliness is critical to reliable system operation,
there is a filter in the oil line at the oil separator outlet.
The oil filter is specified to provide a high level of filtration
(5 μm) required for long bearing life.
The filter should be checked after the first 500 hours of
operation, and every subsequent 2000 hours. The filter should
be replaced at any time when the pressure differential
across the filter exceeds 200 kPa (2 bar).
The pressure drop across the filter can be determined by
measuring the pressure at the filter service port and the oil
pressure port. The difference in these two pressures will be
the pressure drop across the filter, check valve, and solenoid
valve. The pressure drop across the check valve and solenoid
valve is approximately 40 kPa (0.4 bar), which should be
subtracted from the two oil pressure measurements to give
the oil filter pressure drop.
11.8.3 - Compressor rotation control
Correct compressor rotation is one of the most critical
application considerations. Reverse rotation, even for a
very short duration, damages the compressor.
The reverse rotation protection scheme must be able to
determine the direction of rotation and stop the compressor
within 300 ms. Reverse rotation is most likely to occur
when-ever the wiring to the compressor terminals is
disturbed.
To minimise the opportunity for reverse rotation, the follow-
ing procedure must be applied. Rewire the power cables to
the compressor terminal pin as originally wired.
For replacement of the compressor, a low pressure switch
is included with the compressor. This low pressure switch
should be temporarily installed as a hard safety on the high
pressure part of the compressor. The purpose of this switch
is to protect the compressor against any wiring errors at
the compressor terminal pin. The electrical contact of the
switch would be wired in series with the high pressure switch.
The switch will remain in place until the compressor has
been started and direction of rotation has been verified; at
this point, the switch will be removed.
The switch that has been selected for detecting reverse
rotation is Carrier part number HK01CB001. This switch
opens the contacts when the pressure falls below 7 kPa. The
switch is a manual reset type that can be reset after the
pressure has once again risen above 70 kPa. It is critical
that the switch be a manual reset type to preclude the
compressor from short cycling in the reverse direction.
11.9 - Variable frequency drive maintenance
CAUTION: Before any work on the VFD ensure that the
circuit is isolated and there is no voltage present. Note
that it may take 5 minutes for the circuit capacitors to
fully discharge after isolating the circuit. Only
appropriately qualified personnel are authorised to work
on the VFD.
In case of any alarm or persistent problem related to the
VFD, contact Carrier Service.
The VFDs fitted with 30XAV-ZE units do not require an
insulation test, even if being replaced; they are
systematically verified before delivery. Moreover, the
filtering components installed in the VFD can falsify the
measurement and may even be damaged. If there is a need
to test the insulation of the unit components (fan motors
and pumps, cables, etc.), the VFD must be disconnected at
the power circuit.