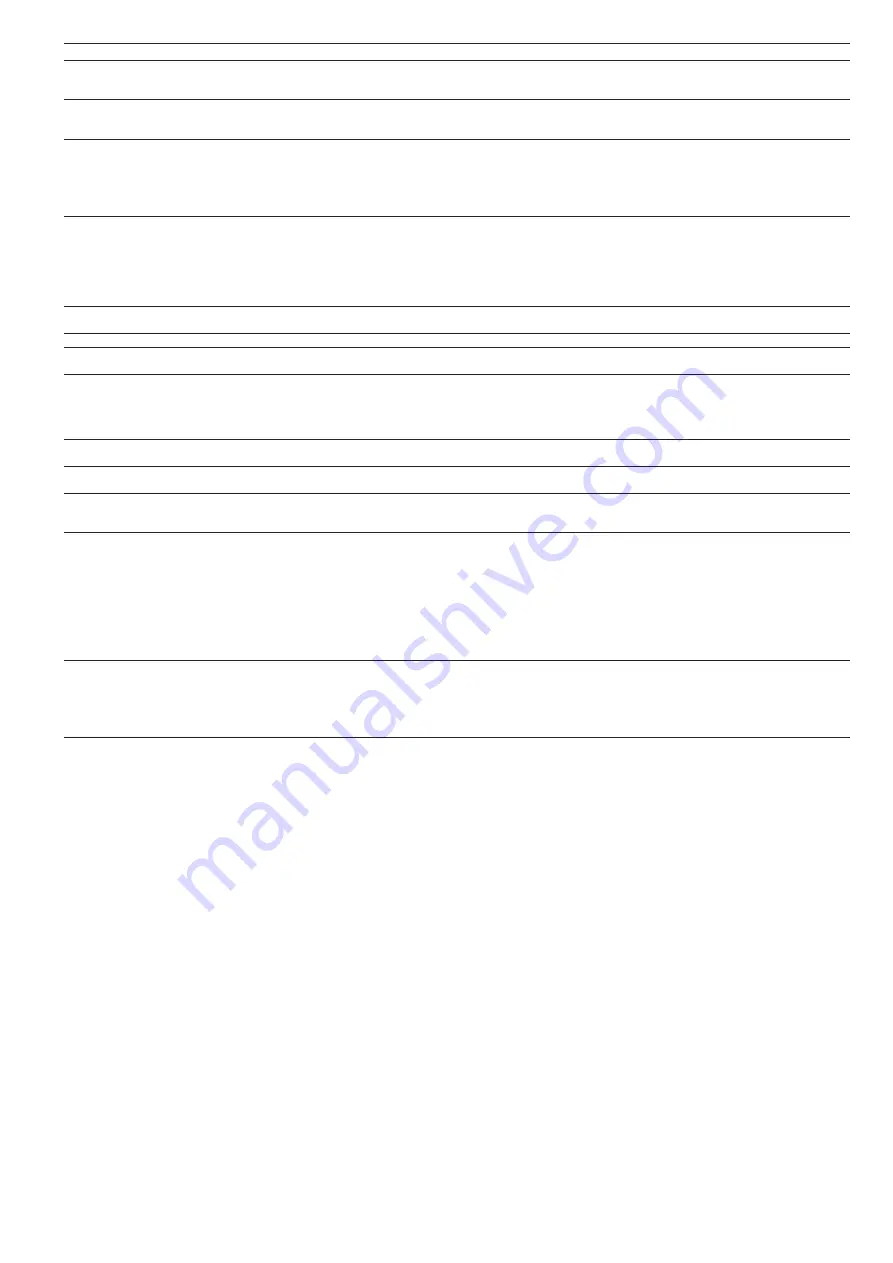
35
options
no.
description
avantages
Utilisation
Insulation of the evap. in/out
ref.lines
256
Thermal insulation of the evaporator entering/
leaving refrigerant lines with flexible, anti-UV
insulant
Prevents condensation on the evaporator entering/leaving
refrigerant lines
401-901
Low noise level
257
Sound insulation of main noise sources
combined with fans speed management
(includes option 279)
6 to 10 dB(A) quiter than standard unit (depending model
and size). Refer to the physical data table for detailed values
401-901
Enviro-Shield anti-corrosion
protection
262
Coating by conversion process which modifies
the surface of the aluminum producing a coating
that is integral to the coil. Complete immersion
in a bath to ensure 100% coverage. No heat
transfer variation, tested 4000 hours salt spray
per ASTM B117
Improved corrosion resistance, recommended for use in
moderately corrosive environments
401-901
Super Enviro-Shield anti-
corrosion protection
263
Extremely durable and flexible epoxy polymer
coating applied on micro channel heat
exchangers by electro coating process, final
UV protective topcoat. Minimal heat transfer
variation, tested 6000 hours constant neutral
salt spray per ASTM B117, superior impact
resistance per ASTM D2794
Improved corrosion resistance, recommended for use in
extremely corrosive environments
401-901
Welded evaporator water
connection kit
266
Victaulic piping connections with welded joints
Easy installation
401-901
Compressor enclousure
279
Compressor sound enclosure
3 dB(A) quiter than standard unit
401-901
Evaporator with aluminium
jacket
281
Evaporator covered with an aluminium sheet for
thermal insulation protection
Improved resistance to aggressive climate conditions
401-901
EMC classification C2, as per
EN 61800-3
282
Additional RFI filters on the unit power line
Reduces electromagnetic interferences. Increase the
variable frequency drive (VFD) immunity level according
to first environment (so called, residential environment)
requirements and allow its compliancy with emissions level
required in category C2
401-901
230V electrical plug
284
230V AC power supply source provided with
plug socket and transformer (180 VA, 0,8 Amps)
Permits connection of a laptop or an electrical device during
unit commissioning or servicing
401-901
Expansion tank
293
6 bar expansion tank in the hydraulic module
(require option 116)
Protects closed hydronic circuit from excessive pressure
Sizes 401/501
only
Fast Capacity Recovery
QM295 New software algorithms to allow quick restart
and fast loading while preserving unit-reliability
Full capacity recovery in less than 5 minutes after power
failure. Matches requirements of typical critical missions
applications
401-901
Carrier Connect link (only
European distributor company)
298
3G router board
NOTE 1: require option 149
NOTE 2: when more than one machine is
installed on site, only one of them shall be
equipped with option 298 while all of them must
be equipped with option 149
NOTE 3: If the Carrier
®
PlantCTRL™ is on site,
option 298 shall be integrated in the Carrier
®
PlantCTRL™ while option 149 is still mandatory
for each single unit.
Enabler for Carrier Connect service offer
401-901
Variable Water Flow control
299
Hydronic control function package that permits
control of the water flow rate based on different
possible logics (at customer choice): constant
∆T, constant outlet pressure and "fixed-speed"
control. For more details, refer to the dedicated
chapter
When variable-speed pumps on the primary circuit, the
VWF control modulates flow rate through the evaporator,
minimising pump consumption while ensuring safe/optimised
chiller operation
401-901