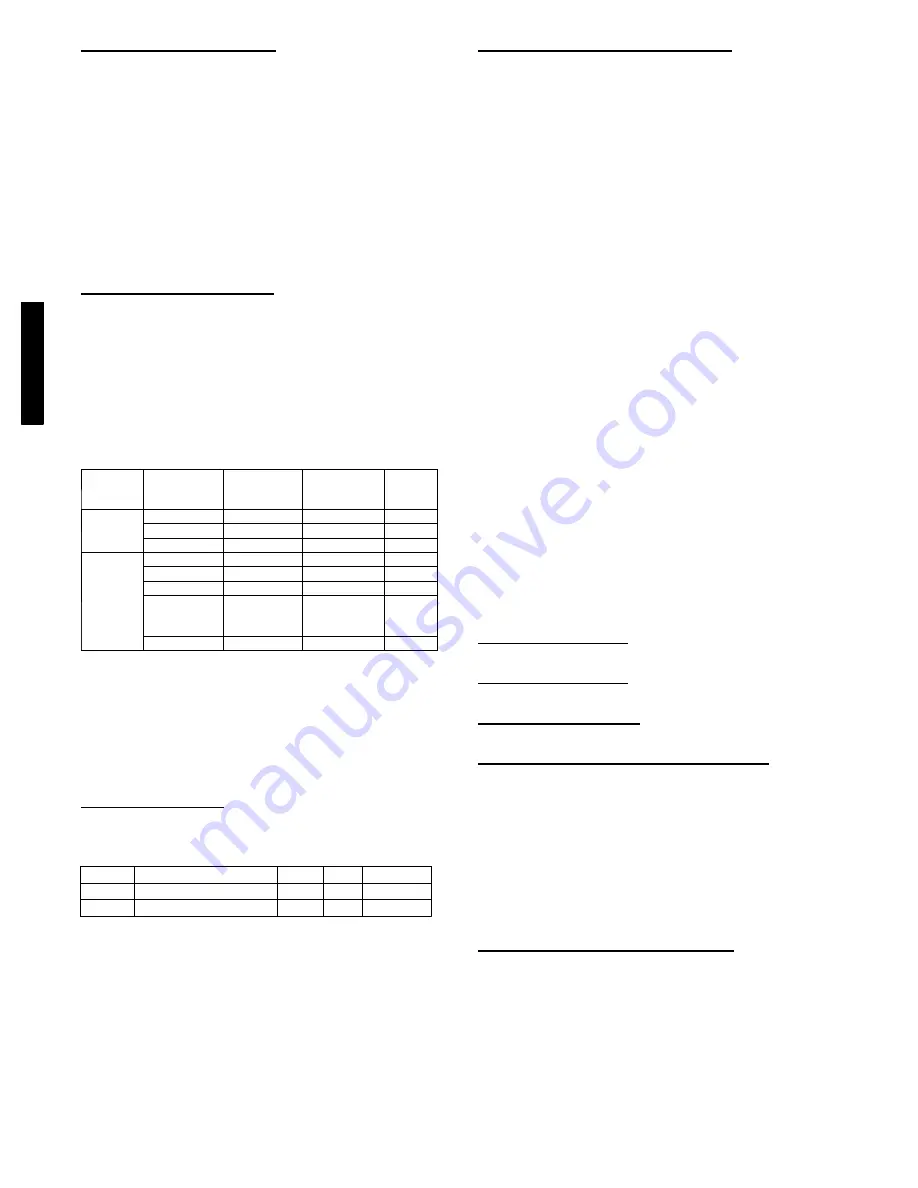
36
Fan Speed -- Reheat2 (FS.RH)
This configuration defines the fan speed used when Hot Gas
Reheat (reheat2) is being requested. Fan speed is based on how
many cooling stages the unit has, how many cooling stages are
being requested, and how many reheat stages are being requested.
If only reheat stages are being requested, then the fan speed will be
set to FS.RH. If the unit only has one circuit of cooling, then the
fan speed will be 100% when dehumidification and cooling is
being requested. If the unit has more then one circuit of cooling
and only one cooling stage is being requested, the fan speed will be
set to FS.CL. Any time more then one cooling stage is requested
the fan speed will be set to 100%. If only one cooling stage is
requested and reheat is requested, then the fan speed will be set to
the greater of the two configurations (FS.CL or FS.RH). (See
Table 11.)
Fan Speed -- Heating (FS.HT)
This configuration defines the intermediate fan speed used when in
heating mode. Fan speed is based on how many heating stages the
unit has and how many heating stages are actually on. If the unit
only has one stage of heat, then the fan speed is set to 100%
anytime the heat stage is on. If the unit has more than one stage of
heat but only one heat stage is on, then the fan speed will be set to
FS.HT. Any time more than one stage of heat is on, the fan speed
is set to 100%.
Table 11 – Cooling Fan Speed Determination
Number
of
Circuits
Cooling
Stages
Requested
Reheat
Stages
Requested
HVAC Mode
Fan
Speed
1
1
0
Cooling
100%
1
>0
Reheat1
100%
0
>0
Reheat2
FS.RH
>1
1
0
Cooling
FS.CL
>1
0
Cooling
100%
>1
>0
Reheat1
100%
1
>0
Reheat1/
Reheat2
FS.CL
or
FS.RH
0
>0
Reheat2
FS.RH
Temperature Compensated Start
This logic is used when the unit is in the unoccupied state. The
control will calculate early Start Bias time based on Space
Temperature deviation from the occupied cooling and heating set
points. This will allow the control to start the unit so that the space
is at conditioned levels when the occupied period starts. This is
required for ASHRAE 90.1 compliance. A space sensor is required
for non-linkage applications.
Setting Up the System
The settings for temperature compensated start can be found in the
local display under
Configuration
→
UNIT
.
ITEM
EXPANSION
RANGE UNITS CCN POINT
TCS.C
Temp.Cmp.Strt.Cool Factr
0 - 60
min
TCSTCOOL
TCS.H
Temp.Cmp.Strt.Heat Factr
0 - 60
min
TCSTHEAT
Temp Comp Strt Cool Factr (TCS.C)
This is the factor for the start time bias equation for cooling.
Temp Comp Strt Heat Factr (TCS.H)
This is the factor for the start time bias equation for heating.
NOTE
: Temperature compensated start is disabled when these
factors are set to 0.
Temperature Compensated Start Logic
The following conditions must be met for the algorithm to run:
S
Unit is in unoccupied state.
S
Next occupied time is valid.
S
Current time of day is valid.
S
Valid space temperature reading is available (sensor or CCN
network).
The algorithm will calculate a Start Bias time in minutes using the
following equations:
If (space temperature > occupied cooling set point)
Start Bias Time = (space temperature – occupied cooling set
point)*
TCS.C
If (space temperature < occupied heating set point)
Start Bias Time = (occupied heating set point – space
temperature)*
TCS.H
When the Start Bias Time is greater than zero the algorithm will
subtract it from the next occupied time to calculate the new start
time. When the new start time is reached, the Temperature
Compensated Start mode is set, the fan is started and the unit
controlled as in an occupied state. Once set, Temperature
Compensated mode will stay on until the unit goes into the
Occupied mode. The Start Bias Time will be written into the CCN
Linkage Equipment Table if the unit is controlled in DAV mode. If
the Unoccupied Economizer Free Cool mode is active when
temperature compensated start begins, the Unoccupied Free Cool
mode will be stopped.
NOTE
: The maximum minutes Start Bias can be is 180.
Carrier Comfort Network (CCN)
R
Configuration
It is possible to configure the
Comfort
Link
™
control to participate
as an element of the Carrier Comfort Network (CCN) system
directly from the local display. This section will deal with
explaining the various programmable options which are found
under the CCN sub-menu in the Configuration mode.
The major configurations for CCN programming are located in the
local displays at
Configuration
→
CCN
.
See Appendix A.
CCN Address (CCN.A)
This configuration is the CCN address the rooftop is assigned.
CCN Address (CCN.B)
This configuration is the CCN bus the rooftop is assigned.
CCN Baud Rate (BAUD)
This configuration is the CCN baud rate.
CCN Time/Date Broadcast (BROD
→
B.TIM)
If this configuration is set to ON, the control will periodically send
the time and date out onto the CCN bus once a minute. If this
device is on a CCN network then it will be important to make sure
that only one device on the bus has this configuration set to ON. If
more than one time broadcaster is present, problems with the time
will occur.
NOTE
:
Only the time and date broadcaster can perform
daylight savings time adjustments. Even if the rooftop is stand
alone, the user may want to set this to ON to accomplish the
daylight/savings function.
CCN OAT Broadcast (BROD
→
B.OAT)
If this configuration is set to ON, the control will periodically
broadcast its outside-air temperature at a rate of once every 30
minutes.
48/
50P
G
and
P
M
Содержание 48/50PG Series
Страница 32: ...32 C07009 Fig 20 Air Baffle Dimensions 48 50PG03 16 48 50PG and PM...
Страница 33: ...33 C08077 Fig 21 Air Baffle Dimensions 48 50PG20 28 and 48 50PM16 28 48 50PG and PM...
Страница 58: ...58 C08549 Fig 28 48PG03 16 Control Wiring Schematic 48 50PG and PM...
Страница 59: ...59 C08550 Fig 29 50PG03 16 Control Wiring Schematic 48 50PG and PM...
Страница 60: ...60 C08551 Fig 30 Typical 48 50PG03 16 Power Wiring Schematic and Legend 48 50PG16 460 3 60 Shown 48 50PG and PM...
Страница 64: ...64 C08471 Fig 34 Typical 48PG and PM16 28 Control Schematic 48PM16 28 Shown 48 50PG and PM...
Страница 66: ...66 C08557 Fig 36 Typical 50PG and PM16 28 Control Schematic 50PG20 28 Shown 48 50PG and PM...
Страница 67: ...67 C08064 Fig 37 Typical 50PG and PM16 28 with Humidi MiZert Control Schematic 50PM16 28 Shown 48 50PG and PM...
Страница 68: ...68 C08558 Fig 38 Typical 48 50PG and PM16 28 Power Schematic 48 50PM16 28 Shown 48 50PG and PM...
Страница 72: ...72 C08565 Fig 42 Typical 48 50PG20 28 Component Arrangement 48 50PG20 24 Shown 48 50PG and PM...
Страница 73: ...73 C08067 Fig 43 48 50PM16 28 Component Arrangement 48 50PG and PM...
Страница 74: ...74 C08562 Fig 44 48 50PM16 28 with Humidi MiZert Component Arrangement 48 50PG and PM...
Страница 208: ...208 48 50PG and PM...