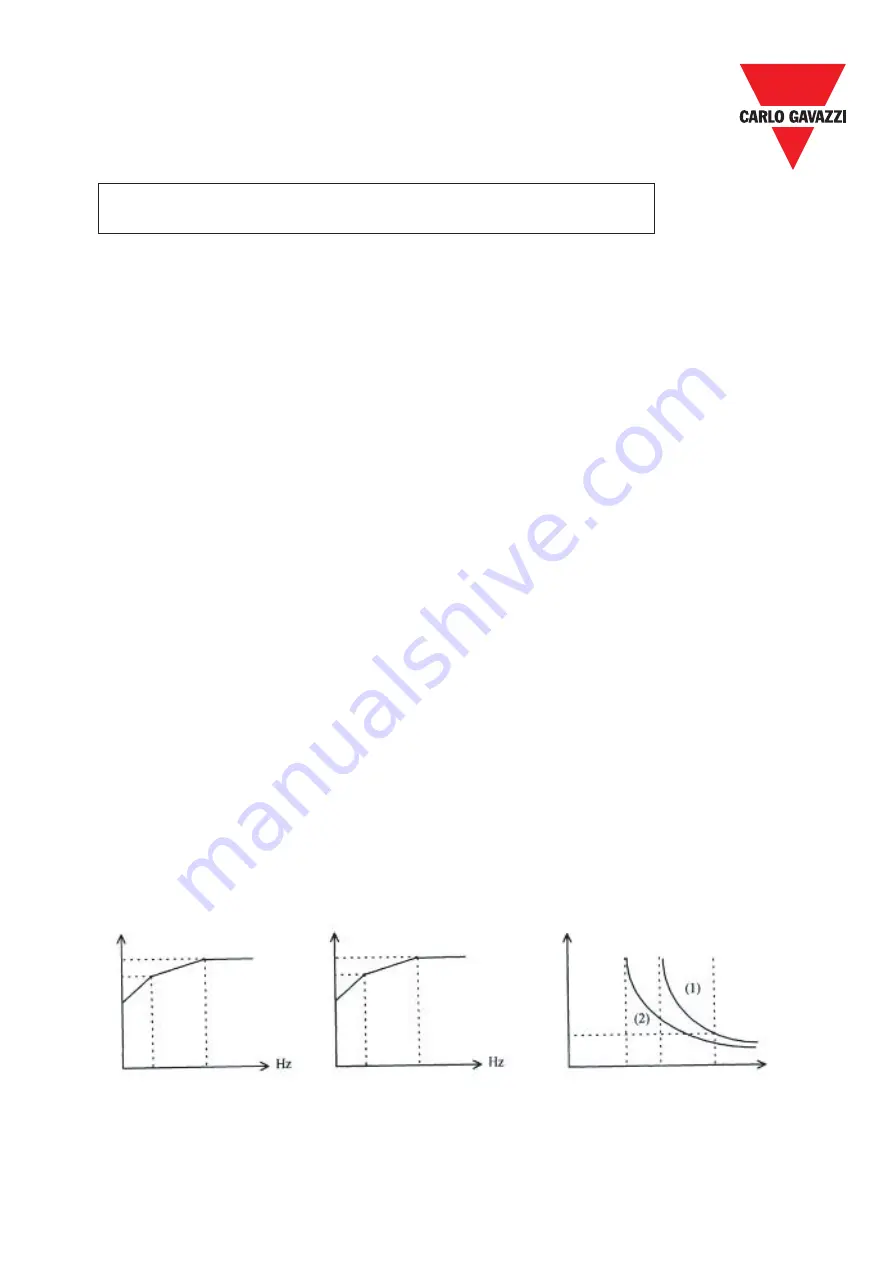
Specifications are subject to change without notice. Pictures are just an example. For special features and/or customization, please ask to our sales network. 23/03/2011
31
F_18: Motor rated current = 50~100 %(0~200%: CPU version
v1.9 and above)
1. The electronic thermal overload protection for motor:
(1) Motor rated current = Inverter rated current x F_18
F_18 = Motor rated current / inverter rated current
(2) When the load is within 100% of the motors rated current, the operation continues. When
the load reaches 150% of the motors rated current the operation is allowed to continue for
1 minute. (Refer to curve (1) in Figure 3)
(3) After protecting the motor with the electronic thermal switch activated, the inverter is cut
off immediately. The OLI light will flash. To resume operation, push the RESET button or
activate an external reset connection wired to terminal 2.
(4) When the motor is operating at low speeds, the heat dissipation efficiency is lower. The
electronic thermal activation level is also reduced. (to change from curve (1) to curve (2) in
Figure 3. Choose the appropriate F_05 setting according to the applied motor to reach the
desired performance.
2. The electronic thermal protecting for inverter:
(1) When the load is within 103% of the inverters rated current, the operation continues. When
the load reaches 150% of rated current of the inverter, the operation will continue for 1
minute. (Refer to curve (1) of figure 3)
(2) After the activation of the electronic thermal switch, the inverter is shut off immediately.
The OL2 light will flash. To resume the operation, push RESET button or activate an
external reset contact on terminal 2.
F_05 = 1,2, 3
50 Hz
s
tandard motor
s
%
F_05 = 4,5,6
60 Hz
s
tandard motor
s
0
0
0
100
90
60
Decay
20
50
(Figure 1)
20 60
100 150
(Figure 3)
In Percentage of Current
(Figure 2)
1.0
%
of
current
Minute
y
%
RVDF Advanced User Manual