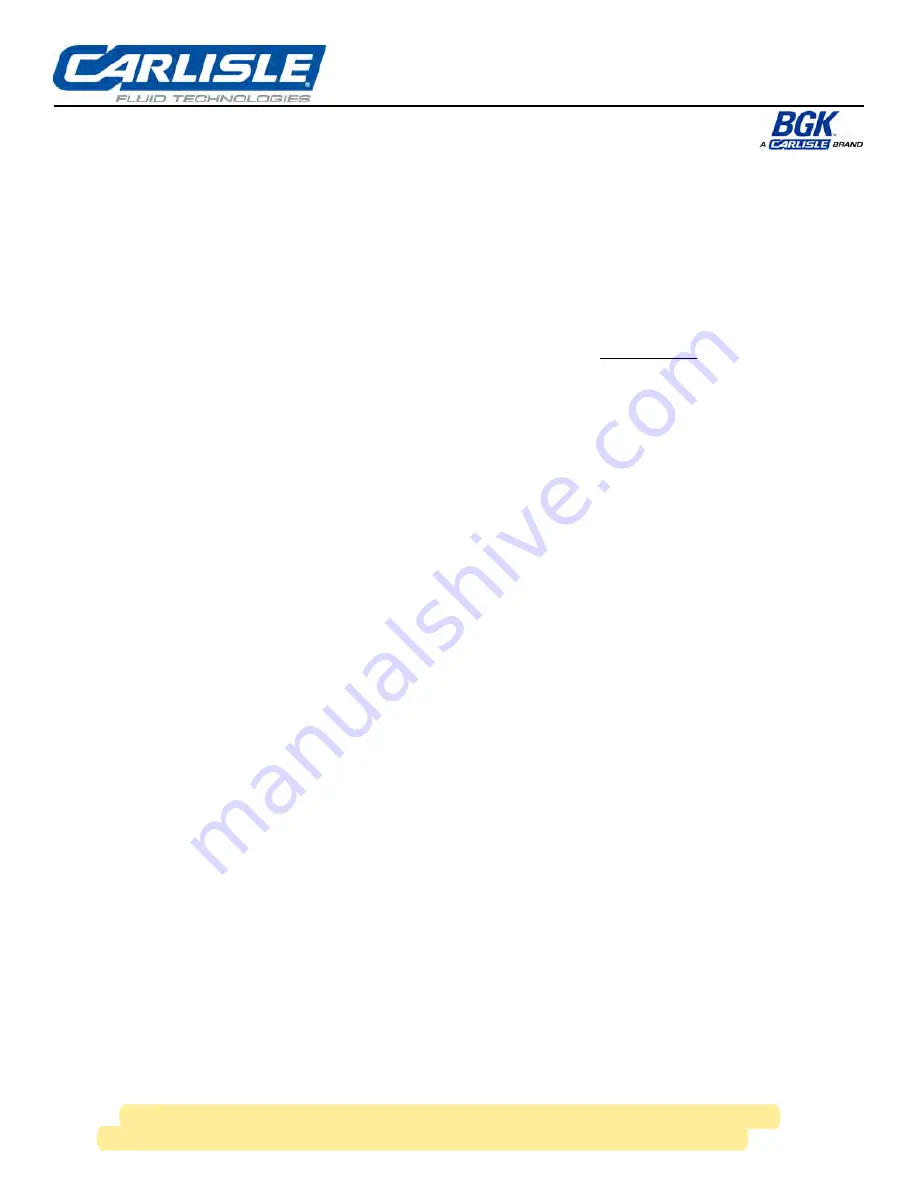
2. Equipment Safety Guidelines
(Read and understand this manual before operating equipment.)
CAUTION!!
1. Turn power off at source before servicing equipment or attempting any electrical or
mechanical maintenance, especially lamp replacement.
2. If the control panel main power switch is ON, voltage may exist at the lamps even
though the lamps are not emitting light. AN ELECTRICAL SHOCK COULD POSSIBLY
RESULT!
3. Heater head(s) contains high voltage. Do not insert metallic objects into cooling louver
openings.
4. Before applying supply power, make sure the AutoCure arm(s) are grounded properly
before equipment operation.
5. Before each operation of the AutoCure arm(s), inspect the repair arm(s) heater
lamp(s). If any lamps are broken or break at any time, shut the power off and
discontinue use. When the damaged or broken lamp(s) are replaced by the qualified
personnel, turn the power back on.
6. This is an automatic piece of equipment. Heater can very quickly come on to full
intensity without warning to unaware personnel.
7. Heater surfaces can become hot when used at high power for extended periods. Use
caution whenever handling heater head(s). The heater head(s) have black insulated
handles to use for moving or manipulating heater head(s).
8. Do not move heater when in operation because it will move the temperature sensor
viewing area and the heater head's distance to product. If the heater accidentally
moves, check temperature sensor viewing area with the "Positioning Beam" and
verify acceptable positioning of heater head.
9. Use care when manipulating or positioning heater head(s) and arms. Avoid possible
pinch points.
10. The positioning beam/pyrometer must be aimed at the surface target to be heated.
If it is not properly aimed at the surface target, (i.e. aimed into open air) the pyrometer
will read a lower temperature causing the unit to go to high lamp intensities for
abnormal time lengths. If used in this condition for extended period of time, it can
damage the unit.
11. When the unit is NOT in operation, the E-stop button MUST be pressed for safety
of personnel, unit, and other material/equipment in vicinity of the heater head(s).
Содержание BGK AutoCure 6000-2216
Страница 1: ...AutoCure 6000 2216 Overhead Heater Assembly and Operating Manual ...
Страница 22: ......
Страница 23: ......
Страница 37: ......
Страница 38: ......
Страница 41: ...A DETAIL J SCALE0 40 1 REMOVET1 11SBOLTAFTERINSTAI I ATION ...
Страница 43: ......
Страница 44: ......
Страница 45: ......
Страница 46: ......
Страница 47: ...AUTOCURE MODEL NUMBER AC6 2216 480 SP ...
Страница 48: ......
Страница 49: ......