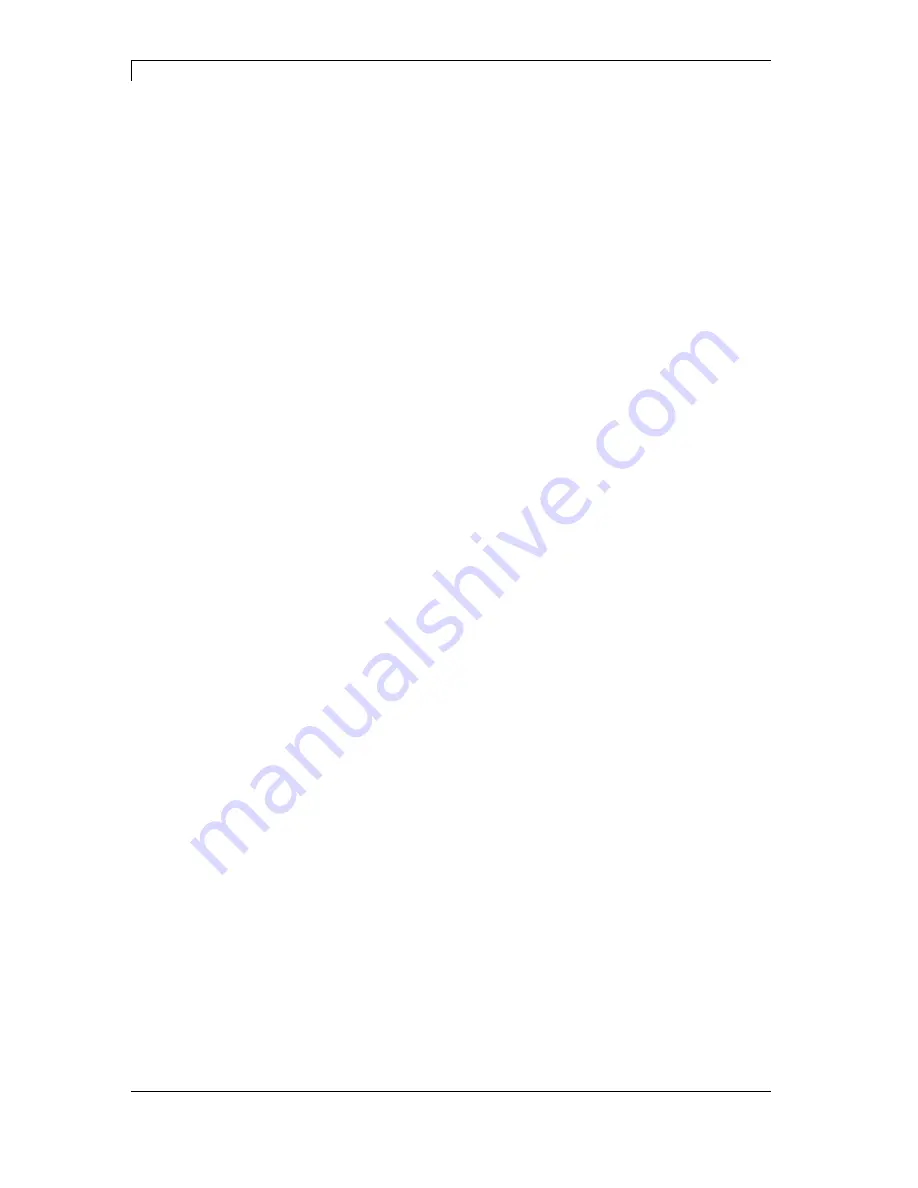
Safety Instructions
Applicator APL 100
12 Operating
Manual
11/13
To avoid inadmissible heating, free air convection has to be ensured.
Protection according IP: 20
Ambient temperature °C (operation): Min. +5 Max. +35
Ambient temperature °C (storage): Min.
−
25 Max. +60
Relative air humidity % (operation): Max. 80
Relative air humidity % (storage): Max. 80
(bedewing of printers not allowed)
We do not take any responsibility for damage caused by:
Ignoring our operating conditions and operating manual.
Incorrect electric installation of environment.
Building alterations of our printers.
Incorrect programming and operation.
Not performed data protection.
Using of not original spare parts and accessories.
Natural wear and tear.
When (re)installing or programming our printers please control the
new settings by test running and test printing. Herewith you avoid
faulty results, reports and evaluation.
Only specially trained staff is allowed to operate the printers.
Control the correct handling of our products and repeat training.
We do not guarantee that all features described in this manual exist in
all models. Caused by our efforts to continue further development and
improvement, technical data might change without notice.
By further developments or regulations of the country illustrations and
examples shown in the manual can be different from the delivered
model.
Please pay attention to the information about admissible print media
and the notes to the printer maintenance, in order to avoid damages
or premature wear.
We endeavoured to write this manual in an understandable form to
give and you as much as possible information. If you have any queries
or if you discover errors, please inform us to give us the possibility to
correct and improve our manual.
Air convection
Limit values
Guarantee
Содержание APL 100
Страница 1: ...APL 100 Operating Manual ...
Страница 18: ......
Страница 26: ......
Страница 38: ......
Страница 48: ......
Страница 52: ......
Страница 53: ...Applicator APL 100 Declaration 11 13 Operating Manual 53 12 Declaration 12 1 Extended Declaration ...
Страница 54: ...Declaration Applicator APL 100 54 Operating Manual 11 13 12 2 EC Declaration of Conformity ...
Страница 57: ......