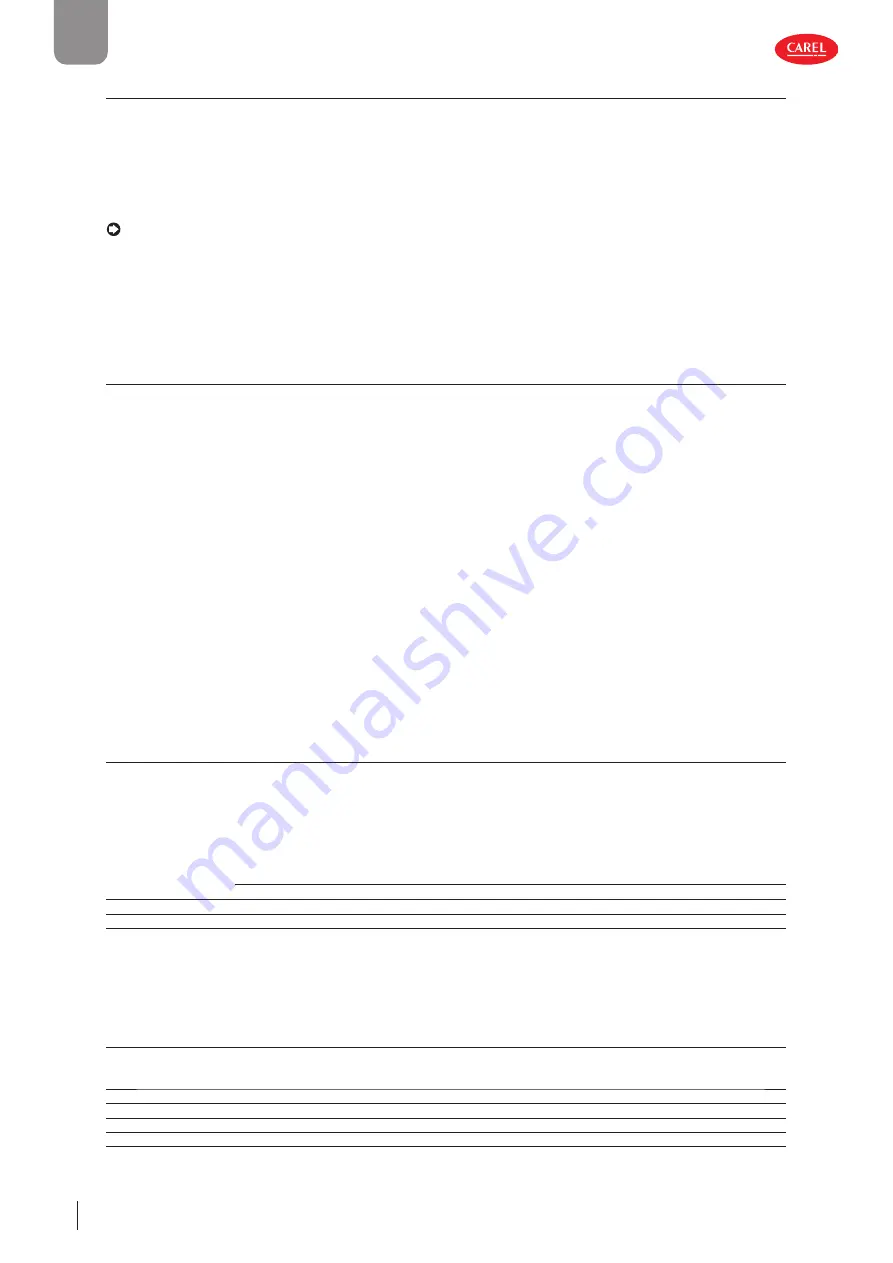
66
ENG
μc0300053EN rel. 2.2 - 14.12.2021
Functions
5.10 Expansion valve driver
The driver to manage the electronic expansion valve is a fundamental device for the μChiller controller. This is used to safely
manage the compressor and thus the circuit, constantly controlling the discharge temperature and the position of the working
point inside the compressor envelope. The solution provided manages unipolar valves up to a certain cooling capacity (Carel
E3V - cooling capacity up to 90- 100 kW) with the built- in driver (DIN model only) and bipolar valves with higher capacities, using
the external EVD Evolution driver. This must be connected to the FBus serial port on μChiller via the Modbus circuit 1 protocol
with a baud rate of 19200 bps. Use a specifi c cable for RS485 (AWG20- 22 with 1½ twisted pair plus shield). See the chapter
“Installation”.
Note:
• EVD Evolution is only used as an expansion valve positioner;
• if the ExV electronic expansion valve is used, the suction temperature probe is connected to input S3 (panel model) or S7
(DIN rail model). See the functional diagrams. For the installation guidelines, see do040010025, available at www.
carel.com.
5.11
C
ontrol of the expansion valve
The control logic manages various functions:
• communication with the EVD Evolution driver, if used (read/write parameters via FBus serial port);
• control of suction superheat (SSH);
• low superheat control and alarm (Low SH);
• minimum evaporation temperature control and alarm (LOP);
• maximum evaporation temperature control and alarm (MOP);
• control of cooling capacity, so as to position the valve correctly in the transient stages according to circuit control status;
• control algorithm that calculates the valve opening steps;
• valve opening value sent to the valve driver.
If the EVD Evolution driver is offl
ine, all the compressors are stopped immediately.
Dedicated electronic expansion valve parameters
Certain parameters relating to the electronic expansion valve vary according to the operating mode:
• chiller;
• heat pump. These are:
• superheat parameters (set point and PID);
• alarm thresholds and integral actions for protection functions: LOP, MOP and Low SH
5.12
S
ource pump
μChiller manages one source-side pump (water/water units only). In the same way as for the user pumps, the source pump is
activated when the unit is switched on, and a shutdown delay after the last compressor stops can be set.
The source pump can be activated:
• when the unit is switched on, and after a set delay for switching off after the unit has been switched off ;
• when the fi rst compressor starts, and after a set delay for switching off after the last compressor stops;
• via temperature control. Below is a table summarising the probes used for controlling the pump in each confi guration:
C
ircuit
Probes used for control
C
hiller
Heat pump
1
Condensing press./temp. circuit 1
Evaporation press./temp. circuit 1
2
Condensing press./temp. circuit 2
Evaporation press./temp. circuit 2
Tab. 5.j
μChiller manages:
• frost protection with the unit off : the pump is started so as to activate fl uid circulation (when the unit is on the function is
disabled).
• pump anti-blocking: if the pump is off for more than a week, it is activated for 3 seconds
User
C
ode
Description
Def
Min
Max
U
O
M
S
S072
Source pump activation 0=Always on
1= On with compressor on
2= Control on condensing press./temp.
0
0
2
-
S
S028
Source pump in cooling: set point
30.0
-999.9
999.9
°C
S
S029
Source pump in heating: set point
10.0
0.0
99.9
°C
S
S034
Source pump: diff erential in cooling
15.0
0.0
99.9
K
S
S035
Source pump: diff erential in heating
5.0
0.0
99.9
K
Содержание uChiller UCHBD00001230
Страница 2: ......
Страница 4: ......
Страница 6: ......
Страница 105: ...105 ENG chiller 0300053EN rel 2 2 14 12 2021 Release notes Notes...
Страница 106: ...106 ENG chiller 0300053EN rel 2 2 14 12 2021 Notes...
Страница 107: ......