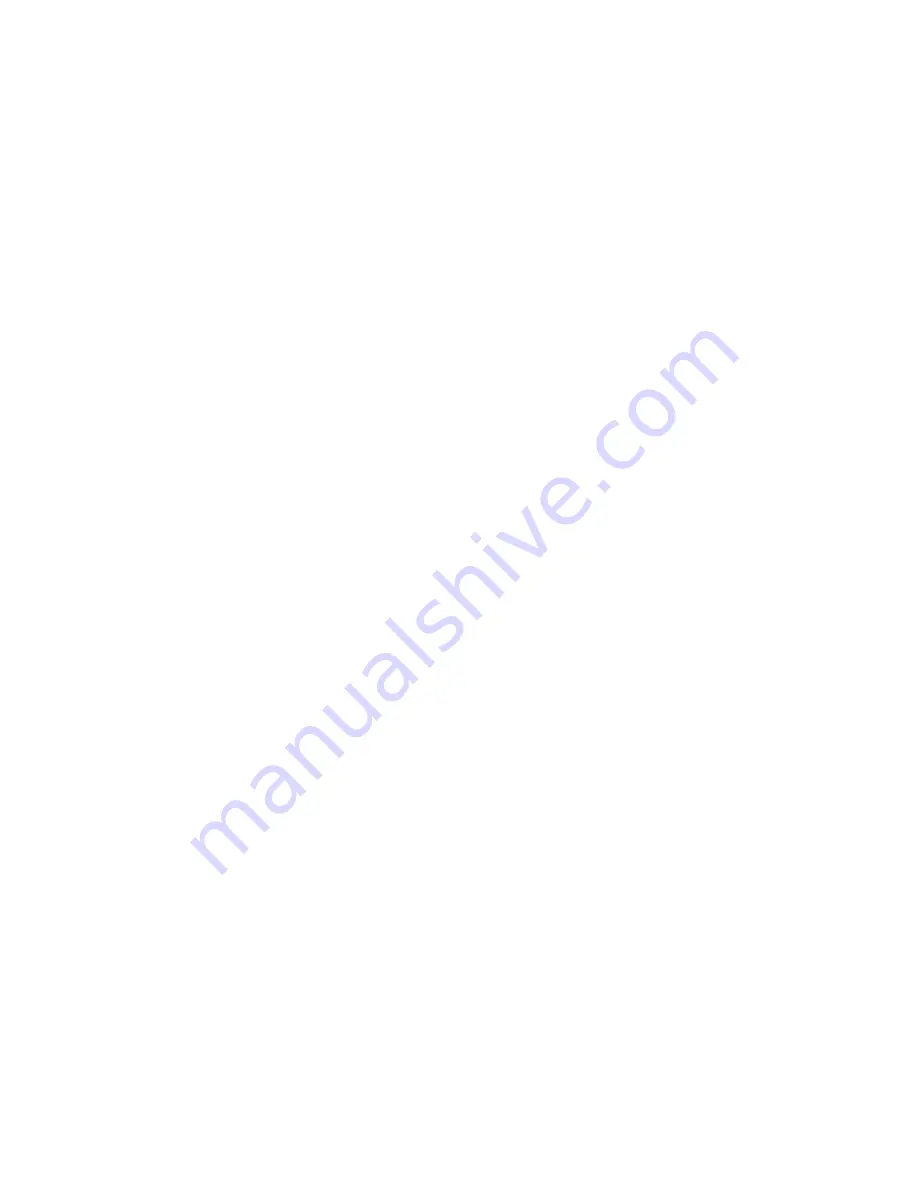
Page
11
of
35
The spray gun, static mixer and block assembly must be hand cleaned at the end of each
spray period using Toluene or Plasite Thinner #19.
5.6
TOPCOATING (Refer to 2.3 Topcoats)
Topcoating shall be applied in accordance with the project specification and manufacturer's
recommendations. The maximum allowable time to topcoat the THERMO-LAG 3000 is 7
days at 70˚F (21˚C). If this time is exceeded, the area should be sweep blasted or
mechanically abraded with 40 grit paper (or approved equal), then solvent wiped, prior to
topcoating. A topcoat is always required. The minimum topcoating times for THERMO-
LAG 3000 A is 10 hours, and for THERMO-LAG 3000 SA 48 hours.
5.7
RECORD KEEPING
The maintaining of proper records is an essential requirement for all THERMO-LAG 3000
projects. The minimum requirements will be established by the project. Refer to Appendix D
for typical application logs.
6.0
CLEAN-UP
The application area shall be maintained in a clean and orderly condition. Following the
application, all overspray, debris, and equipment shall be removed and the area left in a
condition acceptable to the Owner and Main Contractor.
7.0
REMOVAL AND REPAIR PROCEDURES
7.1
REMOVAL
The preferred method is to cut through the THERMO-LAG 3000 at right angles to the
substrate with a disc saw around the area to be removed. Make sure that the steel
substrate is not damaged. A power chisel can then be used to “chip” away the THERMO-
LAG 3000 from the substrate.
It is essential that proper safety precautions are taken during this operation. Reference shall
be made to the THERMO-LAG 3000 Material Safety Data Sheets (MSDS) and all site safety
requirements.
7.2
REPAIRS - GENERAL
In instances when THERMO-LAG 3000 has been damaged or is in need of repair the
following procedures shall be followed:
The primer system shall be reinstated to its original specification.
Remove all damaged material back to solidly adhered material. All edges can be left as butt
joints to a 90 degree angle or beveled to a 45 degree angle. All edges must be solvent
cleaned and allowed to dry before commencing application of THERMO-LAG 3000. It is
important that the newly applied THERMO-LAG 3000 blends into the existing material to
achieve a uniform appearance. The THERMO-LAG 3000 shall be troweled or spray applied
to the appropriate thickness for mesh placement. The specified mesh type shall be butted
up to the existing mesh (no overlaps required). The final specified thickness of THERMO-
LAG 3000 can then be applied, based on the project specification and fire test certification.
The specified topcoat system shall be applied, based on the original specification, in strict
accordance with Carboline’s written instructions.
8.0
IN SHOP APPLICATION – PRE-ERECTION
Содержание Thermo-Lag 3000
Страница 21: ...Page 14 of 35 APPENDIX A THERMO LAG 3000 ACCEPTABLE PRIMER LIST...
Страница 23: ...Page 16 of 35 APPENDIX B THERMO LAG 3000 ACCEPTABLE TOPCOAT LIST...
Страница 25: ...Page 18 of 35 APPENDIX C THERMO LAG 3000 ASTM E119 DESIGNS...
Страница 38: ...Page 31 of 35 APPENDIX D THERMO LAG 3000 TYPICAL APPLICATION LOGS...
Страница 40: ...Page 33 of 35...
Страница 41: ...Page 34 of 35...
Страница 42: ...Page 35 of 35...