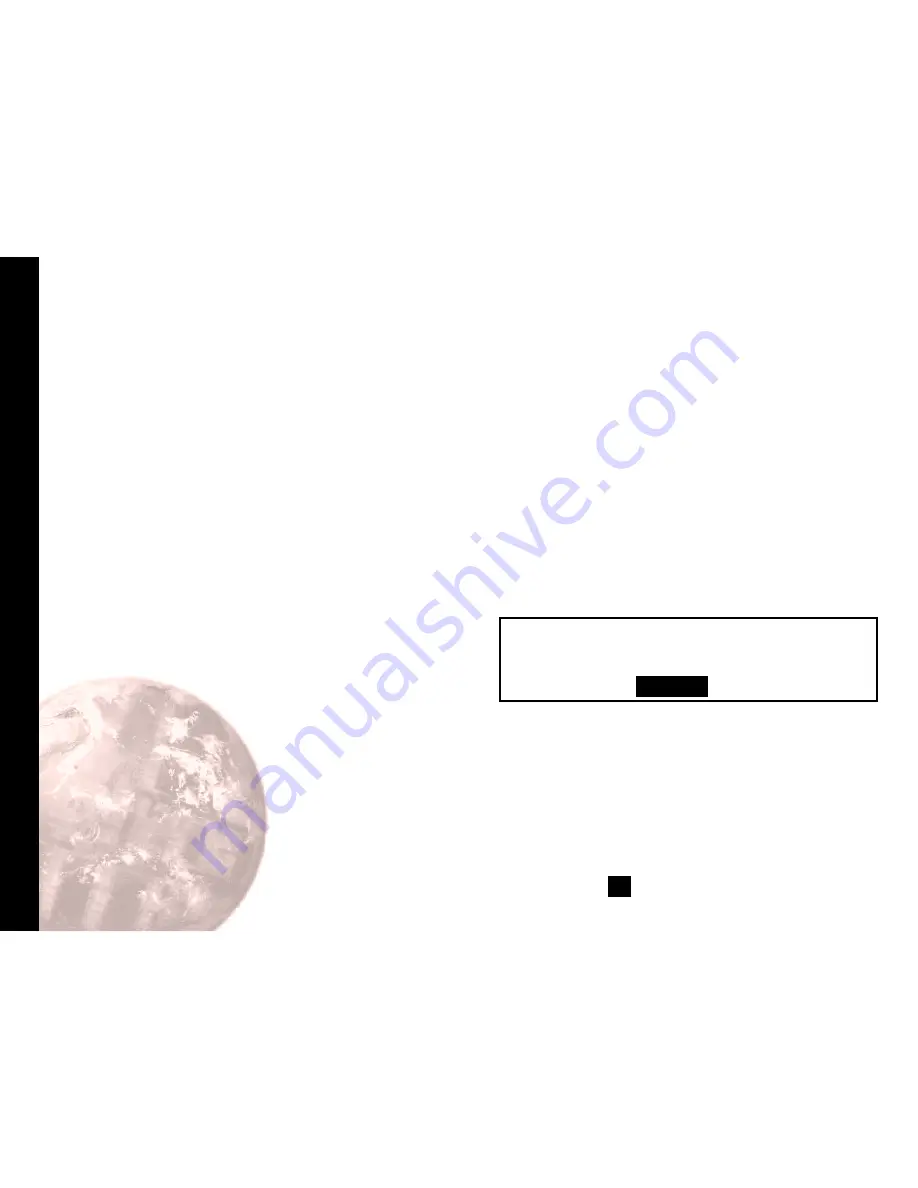
Overview
CYCLE-TIME
The choice of cycle-time is influenced by the external
switching device or load. e.g. contactor, SSR, Valve. A
setting that is too long for the process will cause oscillation
and a setting that is too short will cause unnecessary wear
to an electro-mechanical switching device.
Cycle-time selection methods
The following methods of cycle-time selection may be used:
Autotune calculated
After
Autotune
has been run and completed the calculated
cycle-time can be manually accepted or adjusted to suit the
switching device. For selection method see
Select Autotune
Calculated Cycle-time
.
Pre-select autotune cycle-time
The controller can be programmed to automatically accept
the calculated
Autotune
cycle-time. For selection method
see
Pre-Select Automatic Acceptance of Any Autotune
Cycle-time
.
Pre-select before autotune
The controller can be programmed manually with any
cycle-time between 0.1 and 81 sec. This cycle-time will not
be changed by any
Autotune
functions. For selection
method see
Pre-Select Cycle-time Before Autotune
.
Factory set
To use the 20 sec factory set cycle-time no action is
needed whether
Autotune
is used or not.
Further information can be programmed into the controller,
see
SECOND SETPOINT, RANGING AND SETPOINT LOCK,
IMPROVING CONTROL ACCURACY
Functions and options
The facilities of the controller are selected from the multi-
level menu using the front panel mounted buttons.
Note:
It is advisable to study this section before any
programming is undertaken.
Each level within the multi-level menu offers different
functions, see
FUNCTIONS MENU
for menu of main
functions. Each function has a range of user selections or
options, see
FUNCTION LIST
for functions and options
details.
Note:
Please note that in the manual, functions are
reversed out from a black background and options
are shown in bold italic;
eg.
TUNE
and
ParK
The controller has two modes, program mode and
operating mode. When in program mode the controller can
be programmed with settings and functions to suit the
application. When in operating mode the controller uses the
setting and functions entered in the program mode to
control the application and also displays the process
variable (temperature). For full details on how to program
the controller see
VIEWING AND SELECTING FUNCTIONS.
Note:
In this manual the letter k is represented by the
character
K
4